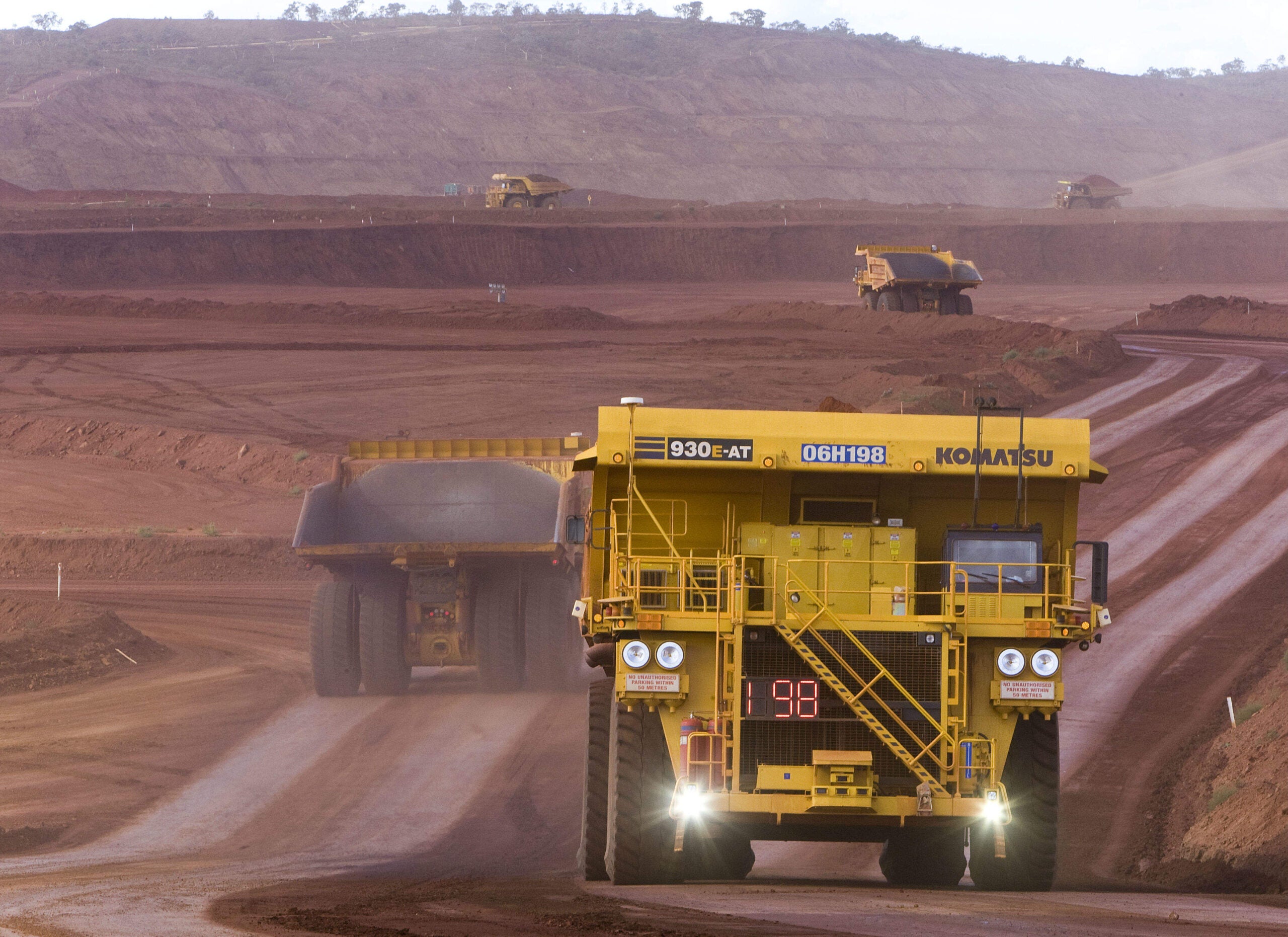
Rio Tinto driverless truck” />
Robots are increasingly taking roles traditionally performed by people in a wide range of sectors. Mining giant Rio Tinto’s mines Yandicoogina and Nammuldi in Pilbara, Western Australia, are the first two mines in the world to start moving all their iron ore using only automated driverless technology. The two mines, as well as the Hope Downs 4 mine, have 69 driverless vehicles in use, which are controlled by workers from 1,200km away in Perth with remote controls.
High-grade iron ore is mined at these sites and the driverless trucks are moving over 20 million tonnes of it per month. They have travelled more than 3.9 million kilometres since the first 150 were deployed across 14 of Rio Tinto’s mines, three ports and two railways in 2012. Now, iron ore is transported at Yandicoogina and Nammuldi solely by driverless vehicles.
“To the naked eye it looks like conventional mining methods,” Yandicoogina’s mining operations manager Josh Bennett told ABC News in October 2015. “I guess the key change for us is the work that employees and our team members are doing now. What we have done is map out our entire mine and put that into a system and the system then works out how to manoeuvre the trucks through the mine.”
Why go driverless?
A major advantage of using driverless trucks is that they can run continuously 24 hours a day, 365 days a year. In theory, having remote access to the lorries may also mean that operations could be controlled from anywhere in the world.
Moreover, without man-power, lunch and bathroom breaks are unnecessary, and when all those hours are added up, downtime is dramatically reduced. It is estimated that this technology could save around 500 work hours a year; a lot of money for mines facing depressed commodity prices and increasingly tight profit margins.
“One of the biggest costs we have got is maintaining mobile assets, so we spend a lot of time on our operator training, education,” said Bennett in the ABC report. “So, there is obvious capital savings, in terms of setting up camps, flying people to site, there is less people so there is less operating costs, but there are some costs that come into running the system and maintenance of the system as well.”
How well do you really know your competitors?
Access the most comprehensive Company Profiles on the market, powered by GlobalData. Save hours of research. Gain competitive edge.
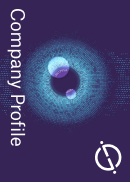
Thank you!
Your download email will arrive shortly
Not ready to buy yet? Download a free sample
We are confident about the unique quality of our Company Profiles. However, we want you to make the most beneficial decision for your business, so we offer a free sample that you can download by submitting the below form
By GlobalDataIn addition to operating costs, risks to workers are also reduced.
“We have taken away a very high-risk role, where employees are exposed to fatigue,” said Bennett. “It is quite challenging to get repeatability out of a human; one of the advantages we have had with autonomous haulage, particularly in the truck fleet, we notice we are getting consistency in terms of the way the machines are operating.”
Rio Tinto is also trialling unmanned trains and mining with robot drills, with the aim of rolling out the machines across as many of its mines as possible. The long-term vision is for most of the company’s supply chain to be remotely controlled from Rio’s operations centre in Perth.
The impact on workers
Labour costs continue to rise, so offsetting this with the increase in automation is important for the economic health of the mining industry. In contrast, those doing the labour aren’t likely to be pleased with the transition.
In general, automation has gained cautious support from unions. Mining representatives say that the shift to remote-controlled trucks will involve the creation of numerous new, highly skilled positions and there is huge potential to improve the safety of mining.
“There are some benefits to automating some of the work that’s been traditionally quite dangerous,” Unions Western Australia secretary Simone McGurk told Reuters back in June 2011 after Rio’s initial announcement to increase its driverless truck fleet. “We’ve still got an unacceptable number of deaths in the mining industry.”
However, the shift towards increased automation in mining could mean fewer hands-on roles and working hours for miners, with many having already lost their jobs in this sector due to falling stock prices and machines being better equipped for the tasks.
Bennett has noted that the shift towards automation also involves the creation of new, highly skilled jobs that should help offset the loss of more traditional work hours.
“We have got roles which are being created such as a central controller and a pit controller which are essential to running the autonomous system,” he told ABC News. “Those are jobs that did not exist five years ago.”
Rio’s lorries are a long way away from the kind of driverless cars that are currently being researched at Google and Tesla. At the mine, the trucks won’t be self-driving in the sense that they can operate themselves, but still require someone to man the remote control. Hence the claim that jobs aren’t being lost, just redistributed.
An automatic future
These plans are only the start of a mining future which will likely operate with a much higher percentage of automated and remote-controlled equipment. In 2011, Rio Tinto reached a deal with Komatsu to buy 150 driverless trucks over the following four years.
Rio also has its Mine of the Future programme, where fully autonomous trains are being tested, in which it has invested $518m to accommodate its expansion of iron ore production to 360 million tonnes a year across its mines. The company expects an entire autonomous railway line to be operational by the middle of 2016.
Rio isn’t alone in its plans. In 2014, BHP Billiton completed a trial of driverless lorries made by Caterpillar – the world’s largest heavy equipment manufacturer – at its coal mine in New Mexico. Fortescue Metals Group has also said that it has plans to implement automated trucks at its Soloman mine in Western Australia.
The opening of BHP’s Jimblebar mine corresponded with the announcement that it would expand the driverless truck fleet of six Caterpillar 793F autonomous trucks with another six to be tested at its neighbouring Wheelarra operation.
Western Australia is already a hub for mining software, with 60% of the world’s mining computer software products being designed and manufactured there. Many in the industry see the rise in automation as key to staying competitive in the market. With robotic systems taking over many labour-intensive jobs, it is to Rio’s advantage to stay ahead of the curve and welcome the inevitable progress towards automation.