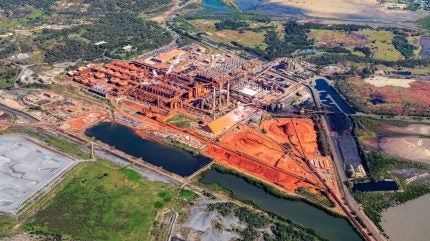
Aluminium is the second most used metal globally after steel, essential in everything from aviation and marine applications to electric vehicles, with usage expected to rise as nations double down on their electrification efforts.
However, its production is one of the most energy intensive, consisting of three steps; mining bauxite, refining to alumina and smelting to make aluminium, each of which requires massive amounts of electricity. According to the Australian Aluminium Council, the country is the world’s sixth-largest producer of aluminium and the largest exporter of alumina, with the industry identified as a key growth opportunity for Australia as global demand rises.
Discover B2B Marketing That Performs
Combine business intelligence and editorial excellence to reach engaged professionals across 36 leading media platforms.
Several government incentives have been introduced to target emissions in this sector; most recently a A$750m ($467.27m) grant in March for green metal technologies, and a new policy launched in January to fund mining companies using renewable energy in the aluminium smelting process
Yet decarbonisation of the aluminium industry is a mammoth task. Technological progress, as well as consistent government support, is required across the supply chain if the industry is to see true transformation.
Aluminium decarbonisation options
The Australian Government has identified four main decarbonisation technologies to clean up aluminium and help Australia on its pathway to net-zero emissions by 2050.
When combined, the technologies – mechanical vapour recompression (MVR), electric boilers, electric calcination and hydrogen calcination – are said to have the potential to reduce emissions from Australia’s six alumina refineries by up to 98%.

US Tariffs are shifting - will you react or anticipate?
Don’t let policy changes catch you off guard. Stay proactive with real-time data and expert analysis.
By GlobalDataDespite their potential, development of these tools is in varying stages of technological and commercial maturity, and significant scale in investment and technology adaptation has been highlighted as crucial.
Christopher Hutchinson, professor of material sciences and engineering at Monash University, says decarbonising aluminium can be addressed in two ways. The first option is to keep similar processes to those currently in use but replace fossil fuels with renewables where possible (as seen in the MVR approach). The second option is to change the way aluminium is refined.
The difficulty of both, as Alcoa highlighted in its progress report on a project to integrate MVR, powered by renewable energy at its Pinjarra Alumina Refinery, is the need to overhaul current infrastructure.
The report, published last November, found that the project needs more technological and infrastructure development than previously thought. It also identified a lack of key electrical engineering skills and pointed to the need for greater collaboration with contractors to design new equipment.
Decarbonisation difficulties
“It is not as simple as switching out the burners heating up the solution for electricity,” says Hutchinson. “You have to redesign the way you do refining. It is not a little modification, but a major change.”
Similarly, Alex Phillips, energy analyst at GlobalData, explains that retrofitting existing smelters or building new facilities can be prohibitively expensive.
“On top of this, it may negatively impact the electricity grid,” he adds. “The theoretical minimum electricity requirement for smelting with a carbon anode is 5.99 kilowatt-hours (kWh) per kilogram (kg) of aluminium, while for inert anodes, it is 9.03kWh/kg of aluminium. This is a valid reason for concern, especially as governments work to decarbonise the electrical grid with renewable energy while simultaneously electrifying a host of other sectors such as transportation.”
However, despite these hurdles, aluminium is particularly well-positioned to make the most of renewable power.
“For an industry like aluminium, 90% of the total energy consumption comes from electricity, and 10% is from a thermal source,” says Duttatreya Das, industrial decarbonisation analyst at think tank Ember. “That is why people call it low-hanging fruit to decarbonise.”
However, as aluminium facilities require 24/7 energy for both the refining and smelting processes, power sources to fill supply gaps are crucial.
Hydroelectric power has been identified as a potential means of bolstering the electricity needed for aluminium smelting. While there are some examples already seen in Australia – such as Tasmania’s Bell Bay smelter – sites suitable for hydropower are limited and other renewable energy sources face intermittency issues.
Back-up power supplies are essential, although scalability is again an issue, with current battery technologies impractical for use at an industrial scale.
“Right now, batteries aren’t big enough to provide the electricity needed,” says Hutchinson. “Battery tech at the moment is great for vehicles and even homes, but the amount of electricity needed for industrial processes means using them for these purposes is just not currently practical.”
Government incentives to scale up these tools are, therefore, seen as essential to the development of both green aluminium, and green metals more generally.
Australia’s green aluminium opportunity
Australia is one of few countries with an end-to-end aluminium industry, meaning its role in the sector is both one of the most significant, and one of the hardest to change. To truly make the most of the country’s industry and incentivise real change, consistent government action was highlighted as a main driver.
“I cannot imagine how we can decarbonise these production processes and make [aluminium] cheaper than it is today without government action,” Hutchinson states.
The need for proper government support is seen throughout the global aluminium industry, not just Australia.
“The need for more supportive government policies and financial incentives is certainly the main hurdle for the widespread decarbonisation of aluminium,” adds Phillips. “Whilst providing incentives for production is one avenue to do so, a wider outlook on the process of decarbonising aluminium is needed.”
Government investment in renewable energy and complementary energy storage solutions is “a necessity” if it is to reliably cater to the power requirements of the aluminium industry, while also meeting the rising power demand of other sectors, Philipps says. “It will also help catalyse private investment, as upfront costs of infrastructure development will not all fall on private companies.”
Indeed, in a global context, incentives for companies to switch to clean production methods are set to ramp up – not only for aluminium but also steel and other critical metals – as governments face the question of how to motivate industries to decarbonise.
Looking beyond subsidies
“One of the things we are likely to see is the EU requiring a report of carbon footprint of the metals it is importing, and even introducing an additional levy based on carbon footprint,” Hutchinson suggests.
Tax credits or subsidies on both an international and domestic level could prove to be the motivation needed for more companies to dive into decarbonisation tools and set the industry on its new path towards green aluminium, although Das highlights the need for an innovation framework to direct funding.
“It has to go beyond subsidies,” Das says. “Throwing money at the problem won’t achieve much; you need to have a framework in place to put the money towards the right things. You need regulatory bodies and probably private players engaging with technology providers to create an innovation ecosystem.”
For now, Das believes government attention should be focused on the short-term goal of ramping up renewable power while innovators work on longer-term technological advancements.
“A lot of technologies are not at readiness level,” he says. “What we know right now is that for the next five years, until 2030, governments should be focusing on replacing energy sources with renewables…. At the same time, innovators are working on cutting edge new technologies that could provide radical change within the industry, but which might take some time to develop.”
Australia’s natural abundance of both renewable power sources and bauxite means it is in a prime position to spearhead the development of green aluminium. However, industry sentiment shows that several challenges remain, with collaboration between the government and industry crucial to making it a reality.
“We are not just looking at decarbonising the energy used for processing aluminium,” asserts Hutchinson. “We are looking at the whole process that needs to change. It will be like reinventing the whole industry.
“However, one thing for certain is [that] we are going to see lots of changes in how aluminium is produced over the next 20 years.”