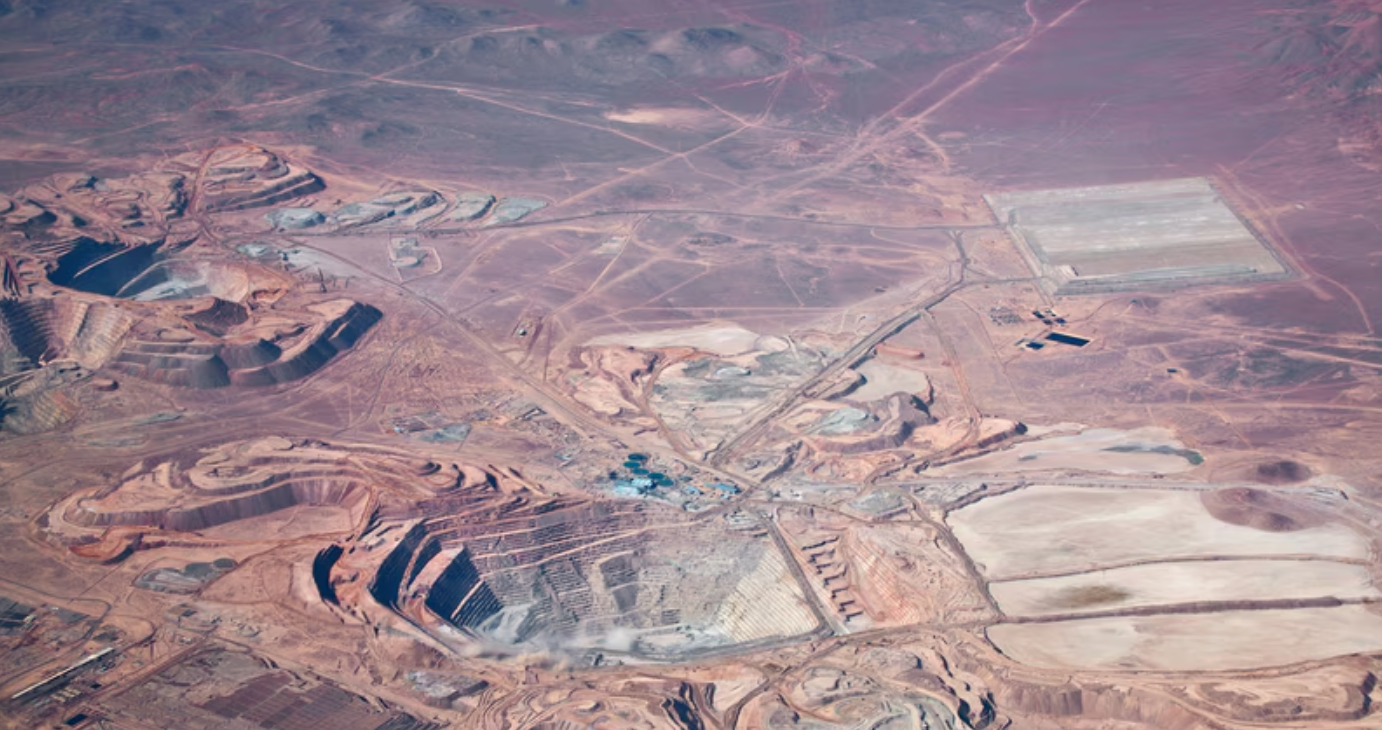
More reliable uptime and reduced maintenance time and costs
A copper mine in Peru underwent a major expansion of its concentrator plant to 360,000 metric tons per day in 2015. 14 conveyors with 72 pulleys are used to transport crushed mineral up to the mill’s high-pressure grinding roll.
Due to extreme contamination and abrasive wear, pulley bearings have to be replaced every 6 months to avoid breakdowns and excessive unplanned production stops.
To minimize downtime and production losses, the mine owners wanted to extend the service life of their conveyor pulleys. All open bearings were replaced with contamination-resistant SKF Three-barrier solutions including sealed SKF spherical roller bearings, a grease barrier in the housings and custom-machined seals for maximum protection.
Nowadays, the mine’s conveyor pulley bearing uptime is more than 26 months.
In addition, the SKF Three-barrier solution is virtually relubrication free.
Fewer and shorter stoppages
SKF replaced the chassis and provided a hydraulic system to move the motors back so that belts could be changed, tightened or adjusted quickly. SKF also supplied transmission belts, belt tension systems, a laser instrument for aligning pulley wheels, post-installation vibration testing and spares for key components.
Three months after installation, the mine had not suffered a single unscheduled stoppage. Management also estimates that any stoppage to change belts or ad-just the pulleys now takes 15 to 20 minutes, compared with up to 4 hours previously.