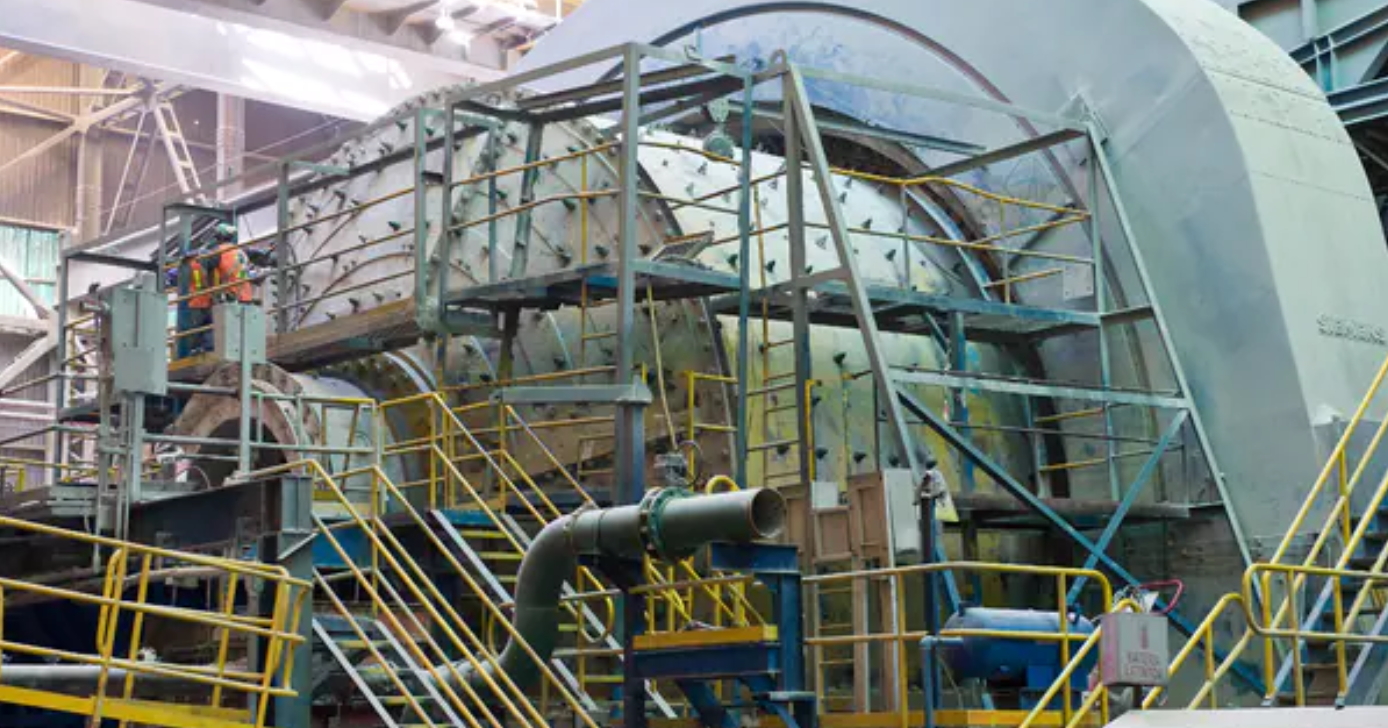
Finding the cause of unplanned shutdowns
A Latin American mining facility had been enduring repeated unplanned shutdowns in its SAG mill for years, with resulting lost production costs of $960,000 annually.
All the while, vibration levels in the mill were growing steadily worse. Unsure of the cause of the failures, even after consulting with several local experts, the company looked to SKF for answers.
SKF Engineering Simulation Services engineers captured a range of machine operating data, and applied it to a series of advanced analyses. These included Vibration Analysis, Operating Deflection Shape Analysis and Finite Element Analysis.
Increasing production by 2%
The investigation revealed that years of service under heavy loads had caused the pinion bearing housings to loosen and lose stiffness. Additionally, the steel frame embedded in the foundation of the electric motor was structurally weak. SKF proposed stiffer bearing housings for the pinion shaft and recommended stiffening the steel frame of the drive motor.
This solution eliminated the unplanned shutdowns and, following modifications, even boosted production capability by 2%, resulting in revenue of about $470,000 in the first year alone:
- Annual lost production costs: $667,000
- Total investment in SKF solution: $195,000
- Total ROI 243%