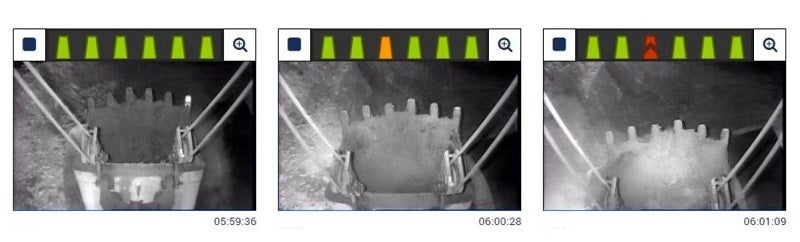
ShovelMetrics™ is our flagship solution that has been installed on over 250 shovels at over 50 mines around the world. An essential tool for maximizing the safety and productivity of mining operations, ShovelMetrics™ includes fragmentation analysis, payload monitoring, tooth wear monitoring and blind-spot monitoring capabilities. However, its main feature is missing tooth detection, which helps prevent dangerous and costly mining accidents such as a jammed crusher. ShovelMetrics™ provides round the clock surveillance of bucket teeth, alerting operators and mine management within minutes of a missing tooth incident.
Such incidents happen every day at mines around the world. A mine in Mexico recently experienced a missing tooth on one of its Bucyrus cable shovels. Luckily they had previously installed ShovelMetrics™, which was able to detect the problem within seconds.
Every digging cycle, in this case roughly every 40 seconds, the ShovelMetrics™ camera captures an image of the bucket teeth, which is instantly analyzed by an intelligent algorithm that determines whether each of the teeth are fully accounted for.
When the algorithm first detects a problem, it sends out a warning. The operator’s in-cab monitor shows this in orange, as can be seen in the image log from the recent incident in Mexico.
The system confirms whether the tooth is definitely missing, or if the initial caution was merely the result of a temporary obstruction from dirt, or boulders. In this case, ShovelMetrics™ determined right away that the tip of the bucket tooth third from the left had definitely broken off.
After this incident occurred, the tooth was recovered from the haul truck, preventing it from causing problems downstream, the shovel operator stopped digging and the tooth was replaced. The shovel was back up and running just over an hour later.
Missing tooth incidents such as this can result in a jammed crusher, which requires a potentially life-threatening tooth removal process and long periods of downtime that can cost a mine hundreds of thousands of dollars in lost productivity. In some cases, a tooth can even make its way through the crusher and cause severe damage to conveyor belts and other downstream machinery. Luckily, ShovelMetrics™ and its counterpart, LoaderMetrics™ can detect missing teeth in seconds, allowing mines to avert potential catastrophes.