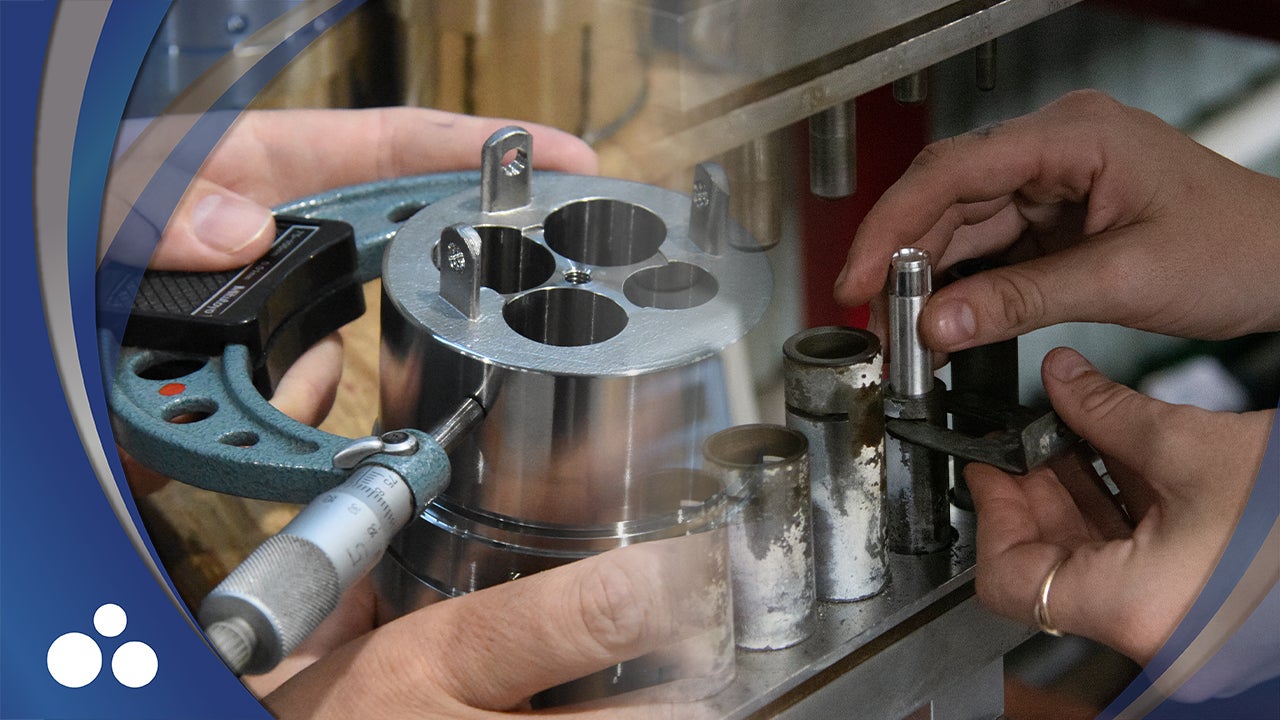
Committed to providing the mining, tunnelling and pumping industries with high and low voltage cable coupler solutions that are reliable, durable, and above all, safe, AusProof strives to ensure the highest level of quality for each and every product. In order to determine that this benchmark is being met, AusProof conducts various tests and checks to assess the quality of the overall product, as well the quality of each component.
These quality assurance tests and checks are carried out by hand throughout each stage of the production and assembly process. AusProof staff are trained to verify a product or identify possible faults using a variety of tools and techniques. During the production and assembly process, a fully assembled plug, coupler or receptacle can go through upwards of 30 different tests and checks that continue up until the point of shipment. Some of these checks are visual, some are carried out by hand using various measurement and assessment tools, whilst others are conducted through the use of machinery.
An example of the many quality assurance tests and checks AusProof carries out is a high-pressure water test. Applied to the body castings of both their high and low voltage ranges to assess their integrity, any pinpoint holes and hairline cracks not visible to the human eye are identifiable through this technique.
Another example of AusProof’s quality testing practices is during the assembly of its various high voltage couplers. After conducting a number of visual and mechanical assembly checks, AusProof completes an insulation resistance check. Following this, each individual coupler is tested in a high-voltage Faraday Cage by over-stressing it, with the insulation resistance check then reapplied. This is done in order to compare the results with the initial test and confirm if the applied high voltage has caused any damage to the coupler to ensure their quality and safety. It is during the high-voltage testing in the Faraday Cage that the LED Live Line Indicators also undergo electrical testing and visual inspection to assess functionality.
AusProof also regularly carries out dissection batch testing on their body castings in order to visually inspect the quality of these castings. These dissections are created at 20mm intervals along the body casting in order to assess and identify any potential defects.
As with any industry, some of the tests and checks carried out by AusProof are necessary in order to meet certain requirements. For AusProof, these requirements often include stainless steel compliances. Looking to assure the industry that no matter the product being received, whether it be stainless steel or aluminium, that they are of the same standard of quality, AusProof applies many of the exact same stainless steel tests to its aluminium products as well.
In order to continuously improve their quality assurance processes and practices, AusProof routinely utilises both internal and external audits to assess the effectiveness of their quality assurance tests and checks. The goal of testing the tests is to not only guarantee they can continue to provide the industry with products of the highest possible standard, but to assure members of the industry that if any mistakes are made, they are as infrequent as humanly possible.
For further information, AusProof contact details can be found on the company’s profile, their state sales representatives available to answer any queries you may have. More information can be requested using the ‘Make an enquiry’ button at the top of the page or visiting the AusProof website.