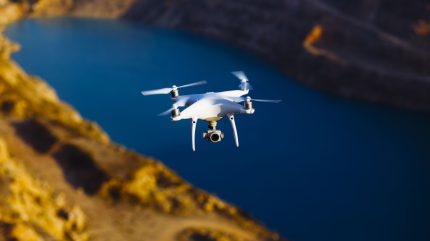
Advancements in automation and drones are rapidly transforming industries across the board, and mining is no exception.
From mineral exploration to transportation, site inspections and clean-ups, technologies such as drones, robotics and advanced sensors are increasingly being deployed to make mines safer and smarter than ever before.
Discover B2B Marketing That Performs
Combine business intelligence and editorial excellence to reach engaged professionals across 36 leading media platforms.
The integration of automation technologies is ushering in a new era of more efficient and sustainable practices and, as a leading player in the global mining sector, Australia is poised to feel the impact.
With this already blossoming industry set to continue booming, we look at some of the technologies leading the charge – and the challenges to overcome.
The rise of automation in Australia
Australia’s national science agency, CSIRO, predicts that by 2030, half of the country’s mining operations will be fully automated. According to its 2023 Mining Technology Roadmap, this shift will result in a 75% reduction in the number of human workers needed in hazardous areas and a 40% improvement in resource recovery through AI-optimised extraction.
Chad Hargrave, Mining Technologies Research Group lead at the organisation, says Australia has seen “significant uptake” of automation tools, driven by a strong mining workforce, a legacy of innovation and the sheer scale of its operations.

US Tariffs are shifting - will you react or anticipate?
Don’t let policy changes catch you off guard. Stay proactive with real-time data and expert analysis.
By GlobalData“These factors give the nation a strong advantage when it comes to developing, implementing and enhancing automation technologies that can be deployed directly into mines,” he adds.
Motivations for increasing automation
In terms of motivations for automation adoption, Hargrave points to the global demand for minerals, declining ore grades and pressure for sustainable development as key drivers.
“These combined factors represent a great opportunity for automation, as new methods will be required to meet demand, while deeper, less-accessible resources require extraction processes that remove human operators from the increasingly hazardous mining environment,” he says.
Similarly, Aidan Knight, associate analyst of Strategic Intelligence at GlobalData, notes that automation is increasingly necessary for productivity as miners move into deeper and more remote terrain.
“Labour, fuel, maintenance and wear-part expenses continue to drive the trend toward automation as robotics, autonomous equipment and autonomous haulage systems can mitigate human error and reduce costs,” he explains.
Knight also highlights maintaining safety standards as a motivation behind automation adoption, with the main technologies rolled out being autonomous haulage systems (primarily seen at above-ground mining operations) and drones, used primarily in underground mines.
Major operators in Australia are already putting these tools to use, and as miners contend with rising operational costs and intensifying productivity pressures, focus on these technologies is only expected to rise.
Mining industry automation examples
The robotics industry is projected to grow to $218bn by 2030, up from $63bn in 2022, according to GlobalData, MINE Australia’s parent company.
In addition, according to its mine site technology adoption survey, nearly half of mines surveyed have already significantly invested in or fully implemented drones.
Rebecca Kahrhoff, industry manager for mining at geographic information system company Esri, says these tools are being primarily used for surveying, mapping, monitoring and inspection purposes.
Esri’s own mapping tech is designed for integration with drones to plan flights, collect imagery and automatically generate 3D models, addressing pain points such as collating vast amounts of data and avoiding hazardous environments.
“Drones can go where it is risky for people, like pit walls or tailings dams, or into hazardous conditions,” she says. “What used to take days can now be done in a few hours and on an as-needed basis – and you get better, high-resolution, real-time data that helps you enhance decision-making.”
Drones are already being seen across Australian mine sites, with BHP conducting nearly 20 drone flights a day at its Western Australia (WA) iron ore sites for safety inspections. Meanwhile, South32 is trialling a fully autonomous drone platform at its Worsley Alumina site, its first multipurpose automated drone system.
Beyond drones, BHP has rolled out autonomous drills across its WA iron ore operations, while Rio Tinto has been running its fully automated train network, AutoHaul, in the Pilbara since 2019.
As technology rapidly advances, the types of tools being deployed are also set to continue expanding – adapting to a growing range of tasks as innovators look to reshape not just how minerals are extracted but how entire operations are designed and managed.
Advancing sensor technology
Gavin Paul, associate professor at the University of Technology Sydney (UTS) Robotics Institute, sees the integration of advanced sensing, robotics and real-time digital twins as one of the biggest technological shifts in mining automation.
“High-performance sensing, such as real-time ore grade analysis and live 3D environmental mapping, is now enabling better decision-making at the mine face,” he tells MINE Australia. “Extended reality technologies ─ such as virtual, augmented and mixed reality ─ are transforming human-machine interaction, making robotic systems more intuitive to operate.”
One example of these new systems can be seen in UTS’ own partnership with Australian start-up NextOre to develop a magnetic resonance (MR) sensor originally designed by CSIRO more than ten years ago.
Using the same technology as MRI scanners in hospitals, the device rapidly scans ore deposits, identifying the valuable material from the mining waste. The UTS team helped scale and automate the system, allowing it to scan “truckloads rather than conveyor belts” of materials, Paul says.
“To enable effective scanning, we used lidar [light detection and ranging technology] to capture detailed 3D point clouds of truckloads in real time, developed algorithms to model the ore load, and determined optimal MR sensor scan locations,” he explains.
The project also used digital twin technology to simulate the truck loading environment, allowing the team to conduct multiple tests of the tools without impacting the real-world equipment.
Previously, the UTS team participated in a project alongside Ausdrill and IMCRC using robotic systems and virtual reality for rock scaling – a process that traditionally requires human teams to abseil down walls to remove potentially unstable rocks. The project’s aim was to replace human workers with robotic systems to limit risks and improve safety standards.
As digital tools continue to advance, the mining supply chain is set to become increasingly connected and projects such as those by UTS will become more commonplace.
Yet while automation promises significant advancements in efficiency and safety within the mining sector, deployment of these tools is not without its challenges
Challenges facing widespread adoption of autonomous tech in mining
While many of the technologies needed to update mines are already on offer, Hargrave says that mine sites have typically proven difficult environments for rollout due to their often remote location.
“Implementation of new automation systems in an operational environment is always difficult, and mine sites present unique challenges,” he says. “Valuable infrastructure and equipment, operator safety and the critical importance of maintaining productivity all combine to create a very restrictive environment for innovation.”
Yet as digitalisation accelerates, focusing on streamlining automated tools and systems is essential for miners lest they get left behind.
Knight identifies four main pain points for automation’s deployment: connectivity; lack of robust cybersecurity infrastructure; interoperability between devices; and a lack of skilled operators.
Crucially, with mine sites becoming increasingly digitised, data security and ease-of-use have become priorities for companies looking to roll out these tools on a wider scale. For an industry typically slow to adopt change, proving the efficacy and benefits of these technologies is essential for industry-wide adoption.
“Beyond technical reliability, cultural and workforce barriers are also real,” says Paul. “Mining has traditionally been slow to adopt new technologies, and retraining or rethinking work practices can be difficult.
“Integration costs, perceived operational risks and the need to adapt legacy infrastructure are also major hurdles,” he adds. “For teleoperated and autonomous systems, ensuring intuitive, user-friendly control interfaces is critical, especially since mining operators are not typically robotics experts.”
The path forward to adoption
Despite the challenges, the general consensus seems to be that the obstacles are surmountable, with targeted training and collaboration between innovators and front line workers seen as key.
“It is not about replacing people – it is about upgrading skills,” Kahrhoff says. “Folks who used to be out in the field with a clipboard are now flying drones, working with 3D models, or building dashboards.
“Tech is being developed with usability in mind, and companies are increasingly investing in upskilling their teams with hands-on training in drone operations and geospatial workflows,” she adds. “The affordability of equipment and low cost of operations are also helping lower accessibility barriers. A lot is helping companies overcome these hurdles.”