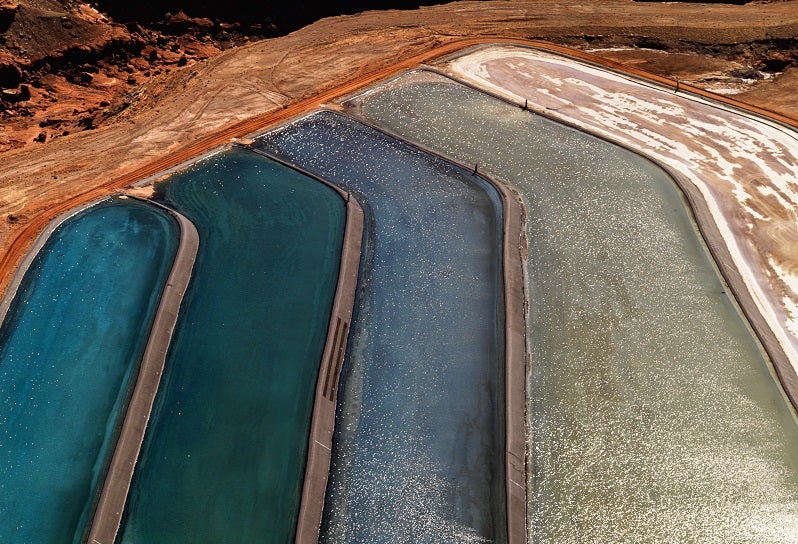
The recently launched Global Tailings Standards Review’s Principle Seven says that what must be addressed is wholescale, including the “design, implementation and operation of monitoring systems to manage risk at all phases of the facility lifecycle, including closure.”
The question regarding the best monitoring method can be answered for the three stages of tailings lifespan including: pre-construction and starter dam/embankment, operational stage, and rehabilitation and closure. All these stages have both similar and dissimilar aspects that require different monitored methods – all of which play a major part in the stability of a tailings dam’s structural integrity. But the most critical monitoring will be during operational stages of the tailings facility (performance-based monitoring) and the rehabilitation stage leading to closure, with the latter probably more involving surface water management and groundwater quality, from an environmental perspective.
Tailings properties that impact design, stability and drainage are in-place and relative density, plasticity, compressibility, consolidation, shear strength, stress parameter (Vick, 1990). These parameters can be monitored at different stages of tailings dam operation and combined with other considerations for monitoring techniques, an effective monitoring system can be determined, after scrutinizing the most specific parameters likely to affect a tailings dam. From that perspective, it then makes it difficult to recommend a “one-size fits all” kind of monitoring system as pre-construction, performance and post-construction monitoring strategies heavily depend on site specifics characteristic to the location of the tailings facility.
Some of the considerations for monitoring techniques according to Tailings Dam safety Guidelines (modified ICOLD Bulletin 74, 1989) are:
• Life of tailings facility
• Construction material and construction period
• Time-dependent material changes i.e. physico-chemical changes during the lifespan of the tailing’s facility
• Inadequate site investigations
• Inadequate knowledge regarding the physical properties of the tailing’s material (rheology properties)
• Chemical activities during different stages of the facility
• Inaccessibility to certain areas tata require monitoring
The monitoring plan for the tailings dam structure should account for rate of placement of lift stages, material rheology, expected embankment deformations, static and dynamic pore pressure, phreatic surface levels and dynamic changes due to hydraulic surcharge and/or surcharge capacity (Probable Maximum Flood, PMF), spillway capacity (catchment area, inflow design for lag time, stage storage design etc.), and freeboard components (wind setup, wave run-up). In general terms, basic monitoring of tailings facilities should include:
• piezometers in embankments to monitor the phreatic surface against agreed trigger levels to maintain embankment stability
• vibrating wire piezometers, standpipes, and bores to monitor groundwater mounding and outward movement beneath and surrounding the facility
• surface water and groundwater quality sampling both upstream and downstream of the facility to check against agreed trigger levels
• rehabilitation trials and monitoring of closure strategies, including slope treatments and covers, and revegetation performance.
In recent years, there has been increased use of interferometric-type of monitoring with ground-based radars (GB-InSAR), satellite-based radar (InSAR) and seismic interferometry, though the last one has not gained much popularity relative to the other methods. These systems are used to detect and record displacement, settlement trends over a period of time and passive seismic noise. The GB-InSAR also has the capability to alarm when set displacement and/or velocity thresholds have been triggered. Passive seismic interferometry which uses ambient noise to create a virtual source to continuously monitor a medium, measures the seismic velocity changes rate through the medium.
The seismic velocity changes can then be related to medium stiffness variation, which is relatable to pore pressure changes loadings, fracturing, internal erosion etc. (Rodrigues et al., 2019). Also, Distributed Fibre Optic Sensing (DFOS) for monitoring strain distribution, temperature, and seepage flow, which can be detected through seasonal temperature variations.
Other monitoring techniques that can be used include, time-domain reflectometry, inclinometers, settlement plates, point-monitors etc for monitoring displacement and/or settlement, flowmeters and /or V-notch drains for seepage monitoring,
Monitoring methods stated above have different role play toward monitoring effectiveness and no one type of monitoring can address all the different properties and elements that require monitoring in a tailing’s dam. Such complexity in material type and construction, characteristic to tailings dams, requires a high level of understanding of all the tailings facility characteristics and monitoring strategies cannot be decided upon ambivalently.
However, regarding tailings monitoring, most operations are found choosing the conservative approach, having all types of monitoring just to be on the “safe” side of monitoring the unknown, which might lead to a state of over-monitoring or rather unnecessary monitoring, subsequently leading to unwarranted outlays, considering that monitoring on a broad and large-scale of most tailings facilities does not come cheap. Yet, even in over-conservatism, the most critical items to be monitored might be missed and still end with an unwanted and “unexpected” consequence. Hence, it is critical to know exactly what needs to be monitored and to choose the most robust instrumentation to monitor those specific parameters.
In summary, the most effective type of monitoring system for a tailings dam facility is a combination of monitoring methods that address:
• Operational stage of the tailings facility i.e. pre-construction, performance during operations, rehabilitation, and closure
• Physical settings of the tailing’s facility i.e. climatic, topographical, and seismic settings
• Construction material and method of construction
• Tailings rheology
• Static and dynamic pore pressure in the tailings facility
• Accessibility to strategic monitoring locations