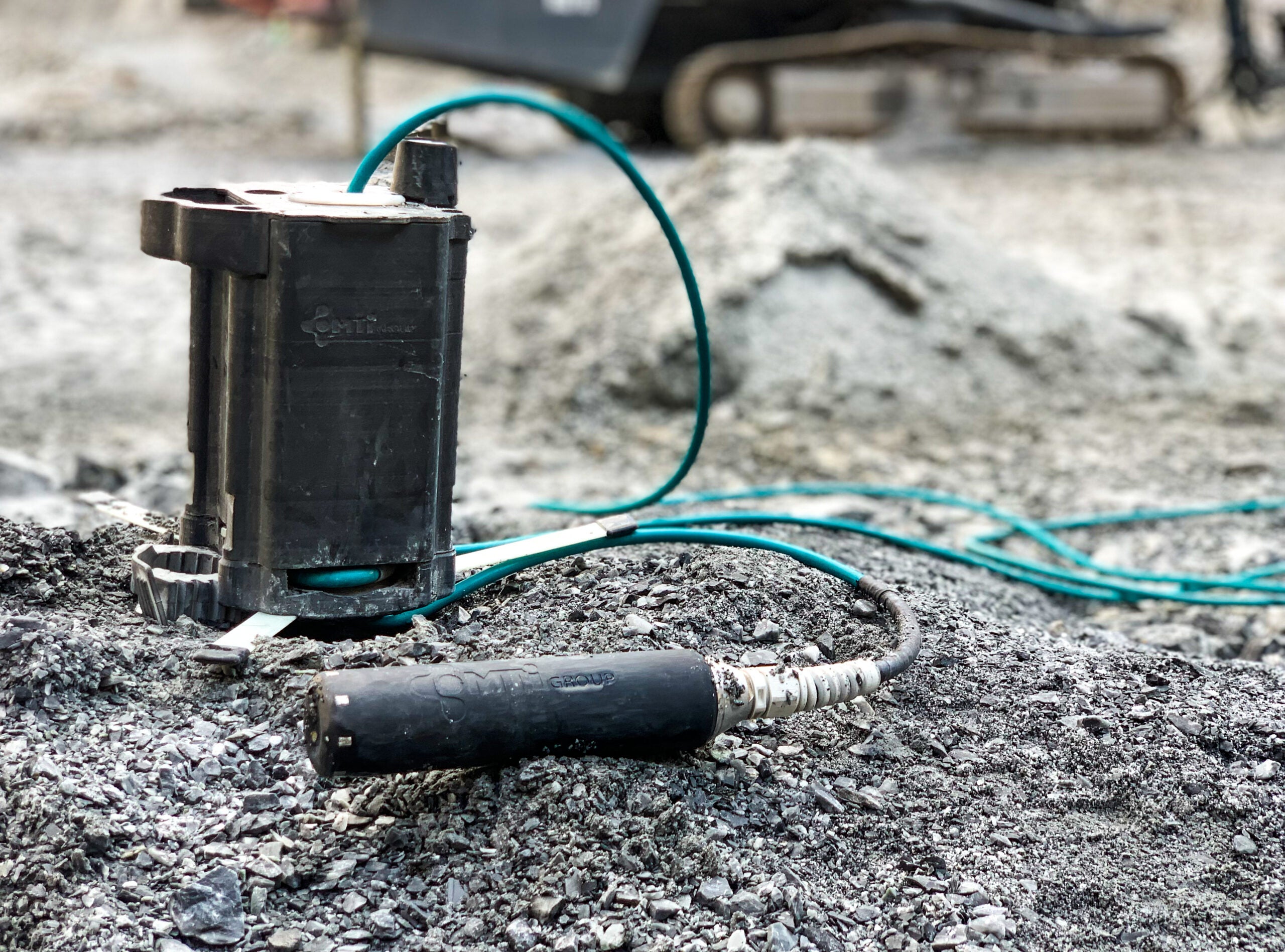
Uttering the seemingly innocuous phrase “there must be a better way” can often ignite a chain reaction of events that creates a wave of change; of progress, as so often is the history of modern innovation. For the better part of two years, this phrase has preoccupied the minds of the engineering team behind MTi Group’s BLASTSCOUT™ precision hole sensor.
A hole sensor designed to precisely map and illuminate the world of blastholes, BLASTSCOUT is an exciting advancement in digitising hole data with significant optimisation potential for blast designs and, in turn, better blasting outcomes.
For over two decades, MTi Group has been working as a close partner to drill and blast (D&B) operations around the world. Through these relationships and in consultation with the industry, BLASTSCOUT’s journey began. “Current hole dipping technology used on most sites involves a tape, dipping weight, pencil, and paper,” says Matthew Fitzsimmons, General Manager of Development at MTi Group.
Improving data quality

This presents several data quality issues in that measurements are style dependent and difficult to validate, “Measurements inherently have varying accuracy dependent on operator experience and “feel”, says Fitzsimmons. This problem is further compounded by the fact that data is often collected on pen and paper, slowing down an already manual process that may sometimes involve the rehandling of data up to three times. In short, data collected in this way has zero integrity, poor traceability, and no accountability.
This is significant because blast designs are informed by the data they receive; to design the blast and make adjustments when deviations to the plan occur. Without correct data, how can a blast design achieve its intended goal? How can a blast be optimised if the data is not a true reflection of the actual conditions in the ground?
From these pain points, the team got to work, developing BLASTSCOUT, a handheld probe that measures, records, and transfers data. Using wearable technology, the operator can simply dip the probe in the hole and, in real-time, get accurate GPS-tracked readings without the burden of data entry or the need to transfer data manually.
“BLASTSCOUT is the first phase of drill and blast QA/QC process automation, replacing tape and paper with a system that accurately captures critical hole parameters and transmits data wirelessly to the point of consumption.” The dipping action will feel familiar with ground crews but with the added benefit of clean data straight to your system. “This approach critically reduces the “barrier to change” as it can immediately be used in current QA/QC processes while remaining scalable”, says Fitzsimmons.
“System modularity was a key driver during the development. The BLASTSCOUT can be configured with the correct sensors and components to measure relevant data based on a site’s requirements”, explains Fitzsimmons. Modular components include sensors for hole height, void and cavity detection (currently in development), detection of water and several more currently in development. “The system is also designed to be easily integrated with a mine’s fleet. The subsequent implementation phase will likely involve mounting the system on LDVs or explosives provider trucks”
This ability to offer modularity and easily integrate into existing practices is part of MTi Group’s phased approach to make solutions accessible and compatible with users’ unique operations. With leading miners already progressing to a digitally connected future, and many other operators aspiring to do the same, easily integrable technologies like BLASTSCOUT are the bridge to this reality.
Shifting the Paradigm in blasthole QA/QC, BLASTSCOUT offers the path to better data, more effective blast designs and better blasting outcomes.