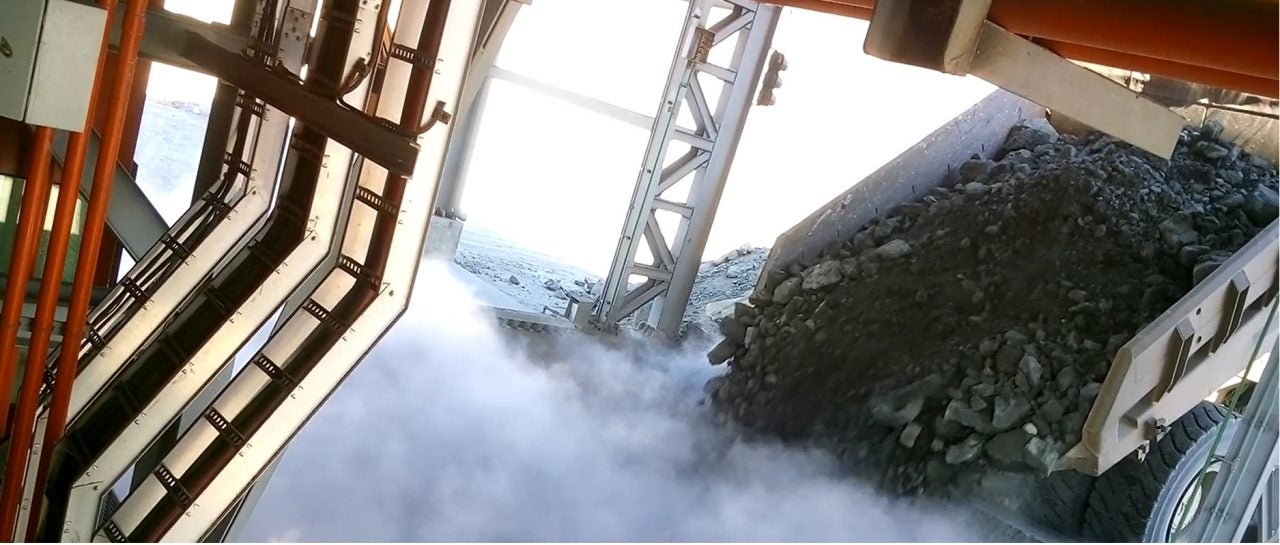
Dust Solutions Inc. (DSI) is a custom solution supplier that designs and manufactures dust suppression systems for a wide array of applications and industries.
We talked with DSI president Richard Posner about the company and its presence in the mining industry.
Tell us about the development of DSI and your dry fog solutions.
DSI was incorporated in 1984. The founder of our organization was part of the team that invented dry fog, in the 1970s.
When I took over the business seven years ago, we saw that there were a number of mining companies that either were unfamiliar with the technology or had a bad experience employing the technology.
Dry fog had been studied by various mining schools throughout the world and as a result, started to get implemented as an effective dust suppression technique, so it’s not a new technology – it’s been around for a while. But there have been some significant system improvements around dry fog, which we have helped innovate.
What separates your products from those similar to the market?
What we’ve done, is we’ve taken into consideration what seems to be one of the biggest problems in these types of systems, which is water quality, and of course, particularly in mining applications.
We’ve put a lot of thought into how we’ve internally done the filtration in our systems and enhanced those systems to prevent situations related to nozzle blockages or poor water quality.
We’ve also made some additional design improvements on the nozzles themselves and some of the adapters around the nozzles thus creating a self-cleaning mechanism. For example, we patented a retractable nozzle assembly that reduces the amount of material build-up and, as well can clean the nozzle tips during the retraction process.
The combination of some of these improvements and a real focus on the filtration system has allowed us to have a system that we believe is more robust and effective in the demanding environments found in mining applications thus reducing the maintenance time for the clients.
Can you tell us about any further developments in your solutions?
We’re in constant R&D and a lot of our stuff is buyout components. So, some of the PLC stuff and everything we’re relying on, you know, big suppliers like Siemens, Allen Bradley, to do some of the design development stuff and then we can implement that into our systems electronically and from a PLC cut type of capability. The modular design of our system allows us to easily incorporate best in class components as part of our offering. For example, we are able to accommodate whatever PLC a customer may require as an interface to their plant computer system. Similarly, if plant conditions dictate heavier filtering, cold weather operation, UV filtering etc., DSI can accommodate components to satisfy those requirements.
We’re in an R&D project right now for more robust nozzle designs that can handle different types of aggressive environments such as high silica content, which damages the nozzle tips.
Only two years ago, we launched our patented retractable nozzle assembly, the Reno, which is a system currently used in the field that allows the nozzle to retract when not in use. So those are the types of things that we’re constantly looking at as an organization to essentially improve the systems and reliability.
Another project that we’re working on right now, for example, is an improvement of our flow control modules in our systems to make them more modular. So, if a client has a failure inside that flow control module, instead of having to replace the entire flow control module or individual components, they can use an off the shelf subassembly to replace the failed device, therefore, facilitating maintenance and installation.
Due to the focus on efficiency, how have these been received in the industry?
Well, I think it’s been a lot of education for us. We’ve gone out and spoken to many of the large mining companies to educate them on the technology along with what we’re doing in the filtration side.
For people who aren’t familiar with the technology, our education is about how the technology works and its effectivity. In the cases that users had a bad experience with dry fog, it’s about showing them what we can do with the filtration packages that would overcome the problems they had with previous systems they purchased.
We’ve done systems for some of the world’s leading resource companies such as Freeport-McMoRan, BHP, Rio Tinto, and some of the largest mines in the world are using our systems effectively, which has allowed us to gain traction in some of the other mining companies.
The reception our systems have received has been gratifying. Since operations are typically suspended when dust mitigation isn’t working, our systems have provided increased uptime resulting in more efficient operations. Furthermore, a benefit of dry fogging unlike other technologies is that the material lost to dust is minimized since the dust that’s captured by the fog falls back onto the material that created the dust. This contributes to overall plant efficiency as well.
You’ve mentioned a couple of key players in the mining field, bhp and Rio Tinto – have you experienced any notable challenges that you’ve had to address with your solutions and what was the outcome?
I think we’ve always had to address challenges – of course, specific to every industry, area and location of the industry is about what kind of responsibilities, they have from a dust mitigation perspective.
Two years ago, we acquired a company called the National Environmental Service Company (NESCO), which was a big player in water sprays. By combining our two technologies [dry fog and water sprays], we’ve been able to provide a more complete package because there are some applications where dry fog isn’t the best solution.
In acquiring NESCO two years ago, we felt we completed our product portfolio as a complete solution provider in combination with our other technology, which is wind fences.
So, with these acquisitions, you’ve become a more comprehensive supplier to the field?
Correct. There are a lot of dust mitigation companies in the sector and there are quite a few technologies, but the core technologies are dust extraction or dust suppression. Dry fog, standard water and high-pressure water sprays would all fall into the dust suppression category
We have not chosen to enter the extraction portion of the dust mitigation market and instead are focused on the suppression side. As a result, our acquisition of NESCO expanded our reach into dust suppression with a complementary technology.
We aim to give our clients a more complete opportunity to work with a supplier that can provide the best solutions for their applications. When the solution dictates a technology we have in-house, we have also partnered with other companies in the past to provide our customer with the optimal solution to their application.