
Have you ever asked for a hydrocyclone selection recommendation, only to receive just one option from the manufacturer? It’s important to know that there are at least two options of hydrocyclone diameter sizes for most of the applications in mill concentrators, in addition to the many other features that could be considered for your particular application.
Primary considerations
The primary considerations during the hydrocyclone sizing and selection process is generally given to the different options to achieve operating performance targets. However, the non-performance objectives should also be taken into account. For example, in a mill circuit you may need to consider:
- Capital budget and ease of maintenance: Is the plant looking for the lowest capital cost option involving the minimum number of operating hydrocyclones?
- Equipment footprint: Is the size of the equipment limited by the space available in the plant for installation?
- Operational budget: Is the plant looking at an option to maximise hydrocyclone wear life and minimise energy costs?
- Day-to-day flexibility: What is the expected fluctuation in feed conditions? Will any fluctuations be significant enough to require hydrocyclones to be turned on or off to accommodate this change? What will be the impact on hydrocyclone performance from any turn down?
- Long-term flexibility: Is the ore hardness expected to change at some point of the operation? Will the mine location affect the circulating load and the new mill feed rate? Will the targeted classification size be revised at some point during the operational life of the plant?
Considerations for desliming applications
Non-performance objectives for desliming applications also exist and may include some of those mentioned for mill circuits as well as others that are specific to the application. For example, these could include:
- Sustainability: Is minimising energy or water consumption a factor?
- Operational flexibility: Will the size classification change for berm wall building and dam construction? What other non-performance objectives may be considered for sand – slimes classification around flotation circuits?
- Mobility: Will the equipment be moved around to different locations?
- Maintenance: How will the cyclones be handled for maintenance? Are there any weight limitations? Is the installation location accessible by crane?
Different sizes for different needs
Global hydrocyclone manufacturers fabricate at least eight or more different size diameters of hydrocyclones to choose from. The graph below illustrates the offering of a typical hydrocyclone equipment manufacturer for mineral processing applications. In this case, the graph is showing the capacity range for cyclones 100 mm in diameter to 800 mm in diameter. Sizes are available outside this range, but this provides the capacity for the core sizes generally available.
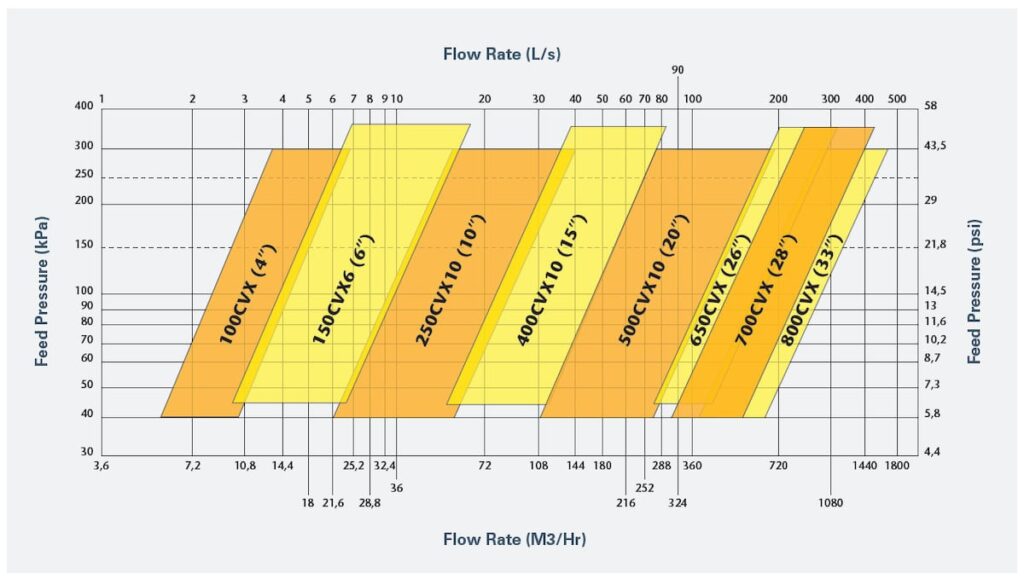
The diagram illustrates the wide range of volumetric flows and operating pressures that a single hydrocyclone size can handle. In this graph, the volumetric capacity is shown in cubic meters per hour along the x-axis, and the operating pressure (kilopascals), is along the y-axis. Note the overlap of volumetric flows that different sized hydrocyclones share. The wide range of flows and operating pressures is made possible because every hydrocyclone size can have a variety of different sized internal fittings – such as feed chamber liners, vortex finders, and spigots/apexes). This is a primary reason why more than one option of hydrocyclone size can be selected for nearly every application.
During selection, and also once installed, there are mechanical and process parameters that can be adjusted to obtain a given hydrocyclone classification size. Although a little more extensive once the equipment is installed, changes to cone sections can also allow hydrocyclone manufacturers and users to adjust performance. Process adjustments to performance generally include the use of feed dilution water and operating pressure to influence changes to the hydrocyclone classification size target.
A mill grinding circuit example
Let’s run through an example. The plant wants to size and select hydrocyclones for the following primary mill grinding circuit duty:
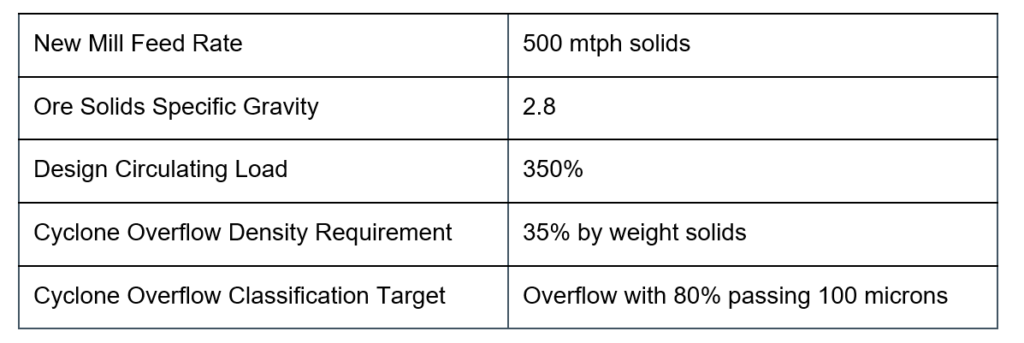
The first option for selection would be based upon the lowest capital cost and the fewest number of operating hydrocyclones. Based on this selection criteria and the feed conditions, it would be customary to offer seven operating 500 mm diameter cyclones to meet these performance requirements. Typically, applications would allow for a few installed spare cyclones, therefore a 10-place cluster of the 500 mm cyclones, as shown below, would be a potential selection.
The second option for selection would be focused upon achieving extended wear life in the liners, lowering energy costs and having the ability to produce finer classifications (if the mill has sufficient power). Based on this selection criteria it would be common practice to offer 12 smaller 400 mm diameter hydrocyclones to meet the performance requirements. Through the reduction in pressure and the use of specific sets of cyclone fittings, the smaller hydrocyclone will cut coarser allowing it to meet the classification target in the overflow. This reduction in pressure allows for the opportunity for lower energy costs as well as extending the wear life in the cyclones, cyclone feed pumps and the piping system. With more operating hydrocyclones, the step change during turn down would also be reduced.
Finally, if we consider a few installed spare cyclones and blanked off feed nozzles, such as in the image shown below, we would offer a 16-place cluster of the 400 mm diameter hydrocyclones. This cluster is potentially more expensive from a capital equipment standpoint than the smaller 10-place cluster, but it’s worth comparing and considering the prices of the two options for the non-performance benefits.
A desliming example
Now, let’s consider a plant desliming application. In this example the plant wants to size and select hydrocyclones for the following desliming application:
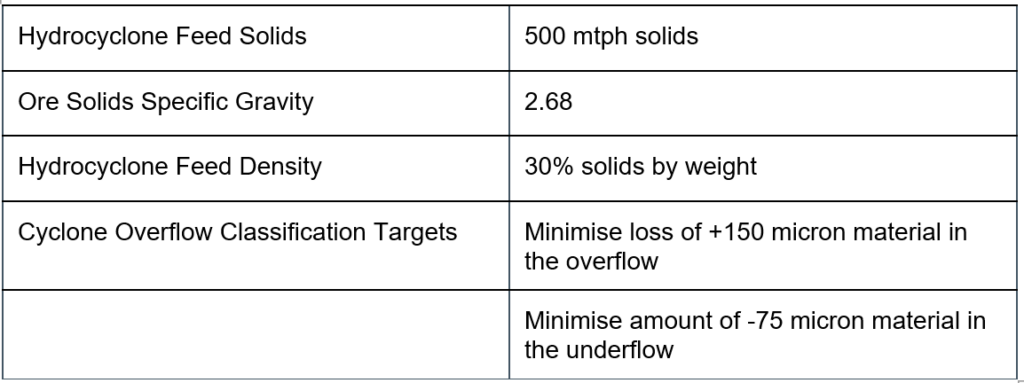
There are five different options of hydrocyclone sizes to consider. The following table shows the results for hydrocyclones from 500 mm in diameter all the way up to 900 mm in diameter.
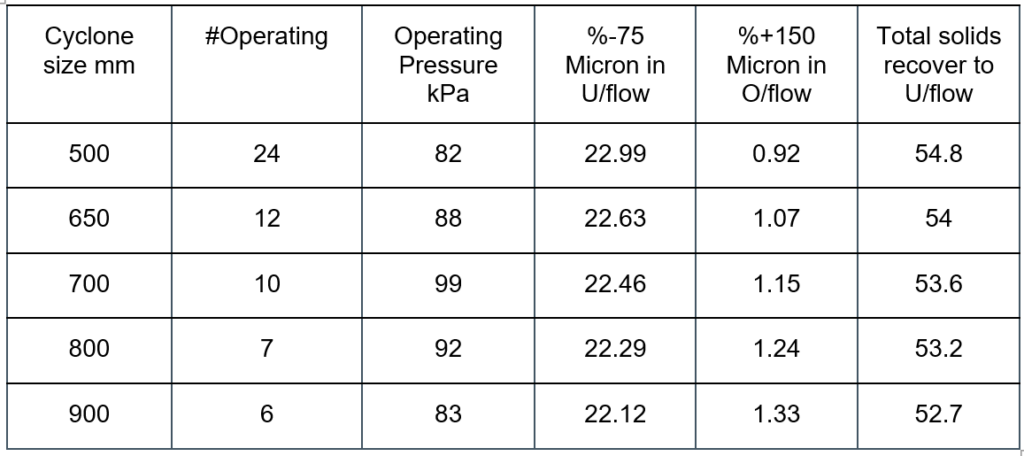
Using the large diameter cyclone size, such as the 900 mm diameter, results in a fewer number of operating cyclones and possibly a lower capital cost. The 900 mm hydrocyclone can also produce an increase in the amount of +150 micron material reporting to the hydrocyclone overflow, and a decrease in the amount of -75 micron material in the cyclone underflow product.
If the smaller hydrocyclone diameter is used, the total solids recovery of material to the hydrocyclone underflow would be higher.
In all five options, the equipment will meet the specification provided, however when you consider all of the non-performance objectives, the best selection may not be either the lowest capital cost or the hydrocyclones that deliver the highest total solids recovery – it may be somewhere in between.
It is important to encourage the practice of getting a variety of options for the use of different hydrocyclone sizes during the selection process. Identifying both performance and non-performance hydrocyclone objectives is crucial to achieving complete hydrocyclone operational flexibility in the plant. Hydrocyclone manufacturers can bid based upon what they believe is typical, but every application tends to have its own requirements. By maximising operational flexibility, you ensure that best practice principles are employed in everyday operation.
To find out more, download the whitepaper below.