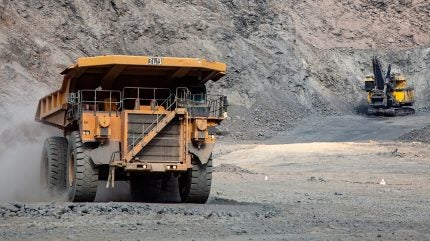
Using the correct lubrication is vital in the mining industry, as it significantly impacts the efficiency, reliability, and longevity of equipment and trucks. By minimising wear and tear, equipment lasts longer especially in the harsh operating conditions typical of mining environments. Mines can be hazardous workplaces, and so lubrication is also an essential ingredient in helping to reduce accidents. By extending component life and reducing the frequency of maintenance tasks, the need to have technicians working on equipment is minimised, decreasing the risk of accidents or injuries.
In a recent GlobalData survey of mining executives from the world’s biggest mining companies[i], 69% said energy was responsible for the steepest price rises, while 65% of respondents said maintenance and repair bills were a big concern, up from 47% the year before. By maintaining optimal performance levels, lubrication plays a pivotal role in helping reduce downtime and lowering operational costs.
Discover B2B Marketing That Performs
Combine business intelligence and editorial excellence to reach engaged professionals across 36 leading media platforms.
The importance of lubrication
One critical benefit of using the correct lubricants is the enhancement of fuel efficiency. For instance, Mobil’s synthetic lubricants help drive fuel efficiency among mining equipment, which is crucial for companies aiming to meet their sustainability ambitions. According to data supplied by Mobil, this can lead to an improvement in fuel economy of up to 5.1% and a huge reduction in waste oil consumption.*
Mining machinery also often operates under high temperatures due to friction and heavy loads. This is where specialised lubricants function as coolants, effectively removing heat generated during operations and preventing overheating, contributing to the overall reliability and performance of the machinery.
While not unique to mining, equipment and machinery in mines are usually subjected to extremely hostile operating conditions, including high temperatures and humidity and sometimes corrosive substances. Specialised lubricants are formulated to provide enhanced wear protection and corrosion resistance, which is critical in prolonging the life of mining equipment. Lubricants are also designed to carry away contaminants and neutralise harmful substances that can accumulate in machinery. In a mining environment, where dust and debris are prevalent, this feature is vital for maintaining the integrity and functionality of the machinery.
The selection of appropriate lubricants
For miners, the selection of the correct lubricants can not only extend the longevity of their machinery and enhance safety, but by ensuring the machinery is running at its full potential and at its most efficient, the mine can cut costs*, both in fuel savings and in maintenance.
Mauricio Lozano Villaseñor spent twenty years supervising field engineers at Mobil, but he now supports the mining industry as Mobil’s Chief Engineer for Latin America and South American countries. Villaseñor says that when it comes to selecting the correct lubricant, the goal is to maximise lubricant performance while minimising unnecessary usage, through strategic selection, monitoring and maintenance approaches.
“All the equipment should be registered and have manuals,” explains Villaseñor. “Miners have a lot of information for their equipment, so it’s critical to integrate all of that information in one platform, like an asset management tool, to access it. Some are just technical manuals, however, sometimes providers will add additional recommendations to improve efficiency and/or to protect equipment.”
When it comes to lubricant selection, choosing high-performance synthetic lubricants or premium products specifically designed for extreme conditions, is key, says Villaseñor, as are predictive maintenance techniques such as implementing regular oil analysis, conducting frequent equipment inspections (often using IoT devices for real-time performance monitoring) and tracking lubricant performance and degradation.
Optimising machinery and processes to cut costs
Improving overall efficiency is critical in optimising mine machinery to prevent excessive equipment stress, as is incorporating technologies, such as digital monitoring systems and data analysis methodologies for lubricant management.
This is also where extended oil life strategies can make a huge difference, says Villaseñor, as well as implementing filtration systems to minimise contamination risks, using advanced lubricant technologies and developing precise oil change schedules.
Best practice is critical, too. “Most of our products are recommended by major OEMs around the world,” says Villaseñor, highlighting Mobil’s international networking ability. “We have strong connections – from Canada to Peru, Australia to Chile, US, Mexico and Colombia.” This ability for cross-regional learning helps to facilitate global best practice and support a continuous improvement culture, adds Villaseñor, emphasising that best practice is not static but represents a systematic approach to achieving consistent, high-quality performance across mining operations.
Villaseñor emphasises that reducing lubricant consumption is not just about using less oil, but implementing a comprehensive, technology-driven approach that maximises lubricant performance while minimising environmental impact. Using the right lubricants at the right time ensures both optimal performance and reduced maintenance.
Download the free factsheet below to discover how your mine operations can benefit from Mobil’s expertise.
[i] GlobalData Mine Site Surveys, August and September 2022 and October and November 2023; Mine-Site Cost Survey, Q4, 2023, December 2023, page 3
* Results are based on the experience of a single customer. Actual results can vary depending upon the type of equipment used and its maintenance, operating conditions and environment, and any prior lubricant used.