
In 2012, Normet launched the world’s first virtual reality (VR) training simulator in mining and tunnelling. It was developed in conjunction with the firm’s customers to improve the skills of sprayed concrete specialists. Apart from wanting to enhance worker safety underground, saving on material waste and costs was also a priority for Normet, a mining innovator at the forefront of driving electrification, digital transformation and emissions reduction in the industry. Concrete spraying is budget intensive and excess material consumption can be an issue.
The simulator, which has been repeatedly upgraded in line with advancing technology capability, was designed to mimic the sprayed concrete application in minute detail so as to provide new operators the unique opportunity to get real-world training in a completely risk-free environment.
“A highly skilled and motivated sprayed concrete operator is an expensive investment, but an unskilled and demotivated operator is far more expensive,” says Panu Oikkonen, director of underground process excellence at Normet.
“The operator is the individual having the most impact on the process costs, safety, and quality of the equipment. No matter how carefully all the other factors in the process are taken care of, the operator either makes it or breaks it.” Normet has said that the concrete spray VR simulator training, on average, has been able to improve customer operator efficiency by almost a quarter.
Normet’s scaling VR simulator launches in 2023
Building on the concrete spraying simulator success, Normet has now added a second application for VR simulator training – another historic first. This one is for scaling, also a vital operation that carries a high level of risk for mining workers.
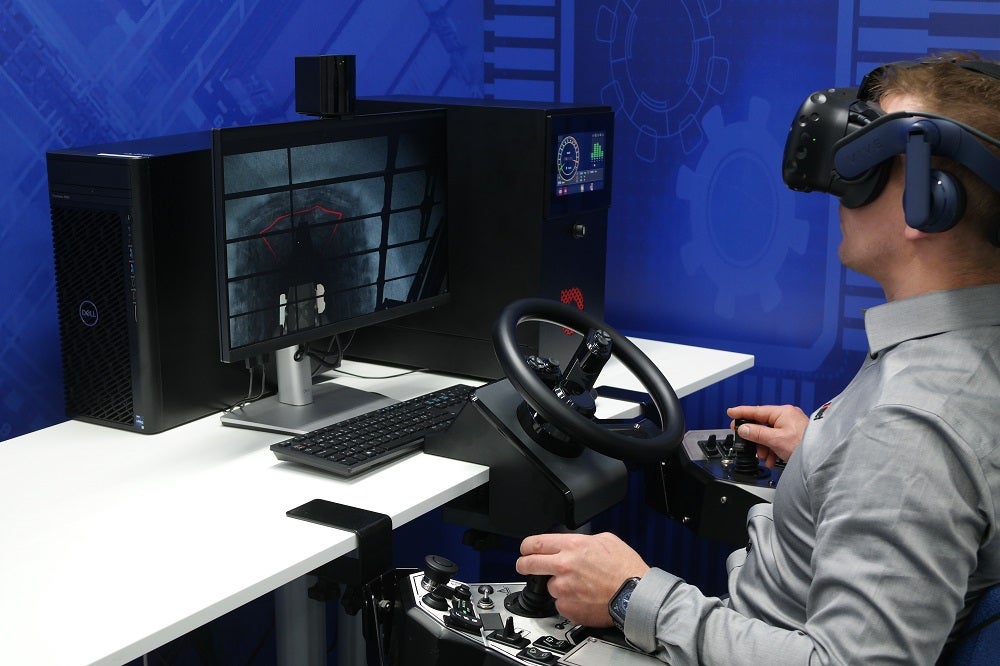
“After blasting, scaling removes loose material from the rock surface,” says Oikkonen. Scaling loose rock is an essential part of safe underground excavation, but it is challenging and dangerous work. Normet’s latest simulator is a digital twin of its flagship Scamec LC Thor, which has an effective vertical reach of up to 9.5 meters and fits tunnels measuring 4 meters wide and 2.4 meters high.
Charging equipment could be next to undergo the digital twin treatment, as the methodology, underpinned by AI, 5G, machine vision and internet-of-things (IoT) sensors is increasingly being used by Normet in product R&D and prototyping to save time and money.
“As a result of that process, we have an exact digital twin of a new piece of equipment which then turns into a training simulator. So, it’s an end-to-end process from R&D, through training our own personnel and to operator training,” says Harri Sonninen, Normet’s global product manager.
What is a digital twin?
Simply, a digital twin is a virtual representation of a physical object, process, or system. They employ artificial intelligence (AI), real-time analytics, visualisation, and simulation tools to identify, prevent, forecast, and optimise the physical environment. In mining, digital twins are being used to model everything from individual equipment to entire mining operations. In 2022, Anglo American partnered with Siemens’ COSMOS platform to create a digital twin of its Quellaveco copper mine in Peru, taking advantage of the growing deployment of 5G, sensors and AI capability to boost efficiencies, performance and worker safety.
Canada’s Teck Resources Ltd in collaboration with LlamaZOO, an interactive 3D visualisation solution provider, developed a virtual reality replica of the Galore Creek development area, which was forecast to save the company between US $100,000 and US $250,000 in site visit costs, while accelerating the project timeline.
For Normet, Sonninen says digital twins are “incredibly useful” because they enable the firm to make mistakes, correct them, and learn from them even before they have begun manufacturing the actual equipment.
“In fact, we get a huge amount of data from our R&D processes, digital twins and VR simulators that we can use to assess all kinds of performance indicators,” he says. “Normet is saving a lot of time during product development, as we don’t have to use materials to build prototypes for testing. We can build a product in a digital world, which means that we can fail, learn and act fast to develop our products.”
He adds: “When we’re collecting the data from the equipment, we can be more efficient with our equipment and related tasks like maintenance. We can really understand how the equipment is being used and how the process can be improved. The performance of the simulator informs the real machine, and vice versa. Digital twin technology is definitely going to enable new opportunities and improve mining processes.”