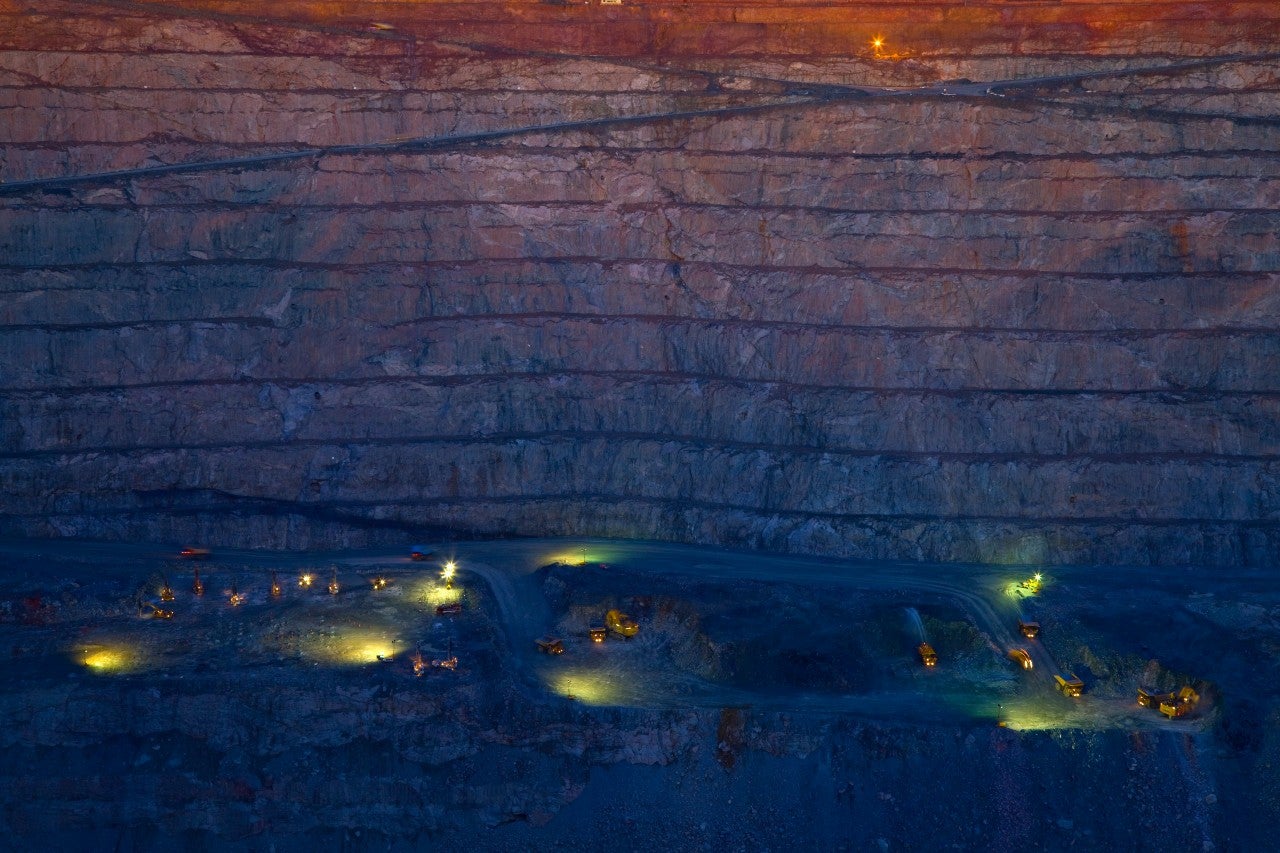
Over the past 18 months, some of the world’s largest mining companies have published commitments to reach net-zero carbon emissions by 2050 – if not before – in order to meet the goals of the Paris Agreement. But as some of the most carbon-intensive companies in the world, how possible is this shift?
“Some miners become disillusioned when assessing how hard or expensive decarbonisation may be,” admits Richard Fenton, Vice President Global, Distributed Energy Systems and Networks at Worley. “There are simple measures that companies can implement to reduce emissions such as improving energy efficiency in mass movement, improving vehicle maintenance and building or buying renewable energy from the grid. However, to make deeper cuts to site emissions, miners need to go beyond a business-as-usual approach and will need to reduce, and ultimately eliminate, the use of fossil fuels from their operations.”
There is growing evidence that there is a sound business case for taking this seriously. GlobalData’s Sustainability in Mining report found companies that embrace all three elements of sustainability – environmental, social and governance – will outperform their peers. It also concluded that if CEOs are too slow to improve their company’s approach to sustainability, they risk losing customers and will see a drop in profits far sooner than they imagine.
Kicking the diesel habit
According to a report by the Australian Renewable Energy Agency, the Australian mining sector uses 10% of the country’s energy use. And it consumes approximately five billion litres of diesel each year. For a large open-cut mine, this could amount to AU$1 billion of a project’s annual operating expenditure across their mining portfolio.
“Diesel fuel is expensive. It’s a finite resource and reliance on its long-term use is counterintuitive to the mining industry’s goal to be carbon neutral in the next 30 years,” explains Fenton. “While some site operators may be comfortable with using diesel for their fleet despite the carbon emissions generated, it’s fast becoming incompatible with the direction of their company.”
Ultimately, Fenton says, miners will have to reduce diesel consumption to achieve Scope 1 and Scope 2 emissions targets. This will lead to either electric mining vehicles or vehicles fuelled by hydrogen or biofuels. So how might miners break the reliance on diesel efficiently and with little disruption? Fenton is clear that while there is a roadmap, it will be complex.
Three steps to displacing diesel
Fenton suggests that looking at decarbonisation as one huge project can be intimidating for those running mine sites. Instead, he recommends a staged approach. “Something like the three horizons model takes miners through a logical transition of fuel reduction, replacement and elimination,” he says. “It provides a strategy that breaks the diesel reduction transition into manageable time periods.”
However, these horizons aren’t stand-alone parcels of work. They are intricately interconnected. Crucially, what’s decided in horizon one sets the foundation for successful decarbonization over following decades.
Horizon one: reduce use
Horizon one applies careful considerations of options, with research and development to build the foundation for emerging technologies as they become viable. The key to this phase, says Fenton, is to concentrate on a “no-regrets policy”.
“Between now and 2030, miners need to decide what technology they can implement today that will transfer to horizons two and three. It can’t be something they’ll regret in a decade’s time,” he explains.
This means considering all equipment that’s used in a mine to make this transition successful. “We work with customers to assess their fleet of diesel-powered equipment. From drilling rigs and large trucks to bucket excavators and loaders. We also consider
ancillary equipment like bulldozers, water trucks and graders. Overall, this ancillary equipment can make up 20% of a mine’s total diesel consumption.”
Currently, the technology options for miners include electrifying the mining fleet and using hydrogen fuel cell electric vehicles. As a step toward electrification, trolley assist is a technology that’s already being implemented.
These diesel electric drive haul trucks receive the power to run the wheel motors from catenary/overhead electric wire lines constructed on specified routes. When running on external electricity it produces more power compared to a generator coupled with a diesel engine, which results in higher truck efficiency. This means increased productivity per machine, lower fuel consumption and increased engine life.
“By using trolley assist, we can reduce diesel use by approximately 90% while driving up the ramp from the floor of mine”, explains Fenton, adding that some miners are also spending a considerable amount of their R&D budget on hydrogen fuel cell vehicles. “As an industry, we need to understand whether this technology can carry forward into horizon three,” he says. “We need to determine if enough renewable energy can be generated to produce hydrogen at a scale that eliminates diesel entirely.”
Horizon two: avoid or replace diesel
Technology is mining’s biggest enabler of transformation and as advances are made in technology, more and more options will become available to pioneering companies in the sector working towards larger fleets of electric vehicles.
As Fenton points out, by 2030 to 2040, there should be viable options to remove diesel engines and their cooling systems from heavy mine vehicles and replace them with batteries. A battery for that size and scale will need to be 1.5 to 1.6 megawatt (MW) hours. While batteries in trucks and road vehicles are currently up to 1 MW (1,000 kWh) hour, they’re still not small or powerful enough to fit in mining haul trucks.
“The move to create a 1.6 MW battery that will fit inside a truck’s engine bay is further in the future. But looking at the projections, battery prices are going down, and their capacity is increasing,” continues Fenton. “This means electric mine vehicles starts to look economic, with an additional advantage of a three-ton weight saving for haul trucks.”
What’s more, adds Fenton, these batteries could be recharged through the trolley assist electrical system, which is why choosing the right technology in the first place is so important.
Elsewhere in the sector, miners are developing hydrogen-based haul systems, integrating hydrogen fuel cells and batteries into surface mining trucks. According to GlobalData, some companies have started installing photovoltaic solar panels to power electrolyzers for hydrogen production (the electrolyzer splits water into hydrogen and oxygen using electrical energy, generating the hydrogen required to fuel the equipment on site).
Miners have set haul truck manufacturers and technology providers the challenge of building the trucks of the future that combine both hydrogen and battery energy systems. Anglo American are set to commence trials into this technology in a platinum mine in South Africa, and if successful, there are plans to extend this further into other mines around the world.
To take advantage of new and emerging technologies such as 100% hydrogen powered excavators, miners could also broaden their horizons and consider alternative equipment manufacturers. “Alternative suppliers such as Volvo are engaging in research and development for zero emissions equipment at the quarry scale. While this technology may not yet be at the size and scale needed for large open cut mining operations, it’s demonstrating the possibilities and the need for other OEMs to increase their investment to help reach the scale large miners need,” said Fenton.
Horizon three: eliminate diesel
If miners have followed horizons one and two then, between 2040 to 2050, they should be primed to eliminate diesel from their mining and transport fleet – pit to port.
Innovation is always occurring, and new technologies are constantly emerging. In horizon three for example, miners might be able to start using inductive technology – or wireless charging – which could help end diesel use in mine sites. Think of it like charging your iPhone on a wireless platform because it works for moving vehicles, too, suggests Fenton.
“It’s currently being explored in the Formula E racing circuit where safety cars charge while stationary. The manufacturers of the Dynamic Electric Vehicle Charging (DEVC) system have also built and tested a system that can charge a vehicle while traveling at 100km/h with 20kW rate of charging. Similar systems are also used in passenger bus services in Washington. This technology is currently in its infancy, but it’s a research and development opportunity.”
The race to net zero
The timetable is not without its challenges, though, warns Fenton. “Electrifying the mining process adds the need for increased renewable energy generation, whether behind the meter on-site or from large scale generators off-site. Ensuring that renewable energy is available and has enough capacity to power transmission and distribution networks is critical in the to shift from diesel to electric or hydrogen use. External investments may need to be made by third parties and communication between miners and energy suppliers needs to start in Horizon 1 and 2.
Miners worldwide are investing billions to reduce their environmental footprint and help combat climate change with a view to becoming carbon neutral by 2050. Zero emissions fleets will play a crucial role. “The vision for achieving net zero needs to be set today,” says Fenton. “But like any momentous change, it’ll take a series of well-planned steps to reach the end goal. The next few years are critical, and miners will need to set staged horizons to pave a clear path toward a diesel-free future.”