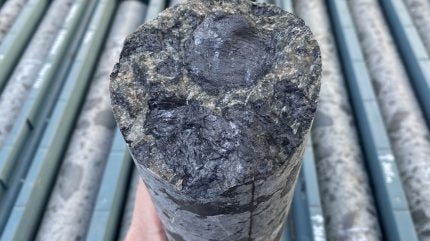
Supplies of battery minerals and rare earths are under pressure as governments and businesses around the world compete for resources to build critical tech. Supply chains for a single product can cover several countries and multiple commodities. As demand increases the importance of sourcing minerals that are socially and environmentally sustainable is becoming a high priority for governments and consumers alike.
Queensland has major advantages in critical minerals, with abundant resources and optimal geology. Crucially, the state has an internationally respected mining industry with mature infrastructure and expertise in extraction and processing. Alongside this is the necessary support in place from the state government, as well as a well-regulated sector that upholds environmental and social standards in mining and processing.
This powerful combination means that many are turning to Queensland to seek solutions for the materials required for critical tech.
Graphite production growth in Australia
Graphite is commonly used in battery anodes for electric vehicles. The material is also used in other areas of critical tech such as semiconductor production and electronics due to its stability, high temperature resistance, and conductive properties.
Due to intense demand for resources, the global graphite production market is projected to experience major growth, according to GlobalData figures, rising by 18.1% in 2025.
China dominates global graphite supplies, with GlobalData estimating production of 1,282.7kt in 2025. This is substantially ahead of the next country, which is Mozambique with an estimated production of 247.5kt for this year.
Between 2027 and 2030, China has projected graphite production growth of 4.14%, rising from 1,419.5kt to 1,478.3kt. However, GlobalData predicts that Australia’s 278% production growth rate of natural graphite will far exceed that of China over 2027 and 2030. It should be noted that the quantities in Australia are far smaller at 45kt in 2027 and 170.3kt in 2030. However, it is very much a case of quality over quantity in Australia – especially in Queensland.
The performance advantages of Queensland graphite
Typically, natural graphite must be heated at approximately 2,400°C for around 15 minutes to achieve the high purity and the necessary crystalline structure and crystallinity. These processes are energy intensive.
However, Queensland possesses a type of volcanic graphite, limited to only a few deposits in the world.
As Queensland graphite was formed differently, it can hold more energy than any other type of natural graphite available due to its crystalline structure. The graphite holds this distinctive structure as it was effectively heat-treated in the ground, meaning it does not require the same levels of energy-intensive processing for purification as other types of natural graphite.
“What we produce outperforms all our peers,” says Art Malone, managing director of Graphinex. “We’ve now made hundreds and hundreds of batteries over the last three years and really proven what our graphite and anodes can do.”
Independent lab results back this up. “That’s shown it goes down to the molecular level measurements and proves that our graphite has ideal morphology,” adds Malone.
Queensland possesses some of the world’s highest-grade graphite deposits, with estimated graphite resources of 5,900kt and a product value of A$300m.
Graphinex is conducting drill hole tests to determine the extent of the graphite orebody at the Esmeralda Graphite Project, which is the largest graphite resource in Australia and covers nine tenements. The company is also building one of the first graphite processing plants in Australia for active anode materials, receiving A$3m from the Australian Government’s A$40m International Partnerships in Critical Minerals Program.

Vanadium and alternative battery materials
With soaring lithium demand for batteries predicted to exceed supply, alternative materials are required to ensure the energy transition remains on track.
Vanadium is emerging as a viable option to address issues with the materials required for battery storage. However, the material is unlikely to appear in electric vehicles any time soon. Vanadium batteries require a stationary position and are fast-emerging as a viable option for grid-scale energy storage. Crucially, the technology is established and well-understood.
The vanadium battery was invented in Australia and Queensland hosts significant deposits at shallow depths, making them more cost-effective to access than deeper deposits and reducing emissions from more intensive mining processes.
While lithium batteries degrade over time and can be a challenge to recycle, this is not an issue for vanadium. The material has an estimated service life of 30 years and can be fully recycled after use. This material could help address issues with grid-scale storage and also support the decarbonisation of off-grid mining operations.
“There’s a huge market opportunity and we need to unlock the vanadium we have now to enable that opportunity to progress,” says Jeremy Peters, general manager of energy at Queensland-based Vecco. “It’s also a relatively low-cost process to make the material for the battery.”
“You can really see the growth of the industry coming and the need for vanadium,” adds Peters.
Progress in vanadium mining and processing
Australia possesses one of the largest known vanadium reserves in the world. Queensland’s main vanadium resources are in the Julia Creek region. Mining companies and the Queensland government are working together to kick start mining operations in this region sooner rather than later.
Vecco is one of these companies. The company has made rapid progress in a relatively short timeframe, with a business model that integrates mining and manufacturing. Vecco discovered its globally significant vanadium resource in 2017, which was followed by the assessment of local electrolyte production in 2020. In 2022, the company signed its first contract for a vanadium battery with Energy Queensland.
A year later, the company began operations at the first vanadium electrolyte plant in Australia. The same year, the company applied for mining lease applications and continues to progress its approvals though streamlined Coordinated Project Status granted by the Coordinator-General. Then in 2024, Sumitomo commissioned a vanadium flow battery utilising Vecco’s processed vanadium.
This significant progress is set to continue over the next couple of years. In north-west Queensland, the company’s operations will include a vanadium mine and refinery. Vecco Critical Minerals Project is worth an estimated A$1.9bn ($1.2bn). Over an expected 17-year mine life, the project will extract an estimated 6.7 million tonnes per annum (tpa) of ore.
Within this total, the project could produce as much as 9,000tpa of vanadium, with 4,000tpa of high-purity alumina, and molybdenum totalling 600tpa. The project is expected to begin operations in the near future. Vecco has production facility in Townsville but a larger commercial scale facility is also being built. Covering 3.2ha, the facility will support large-scale manufacturing of electrolytes in Queensland, with manufacturing locations also primed for Europe and the US.
The support available from the Government of Queensland has been integral to Vecco’s progress. “The state’s set up, the government’s ready, and willing to get these minerals out of the ground and help companies to be as successful as they can in this environment and make the most of the opportunity,” says Peters.
Reliable supplies of rare earth elements
Rare earth elements (REEs) are essential to the technologies shaping our future — from electric vehicles and offshore wind turbines to smartphones, MRI machines, and defence systems. As global demand for high-tech and low-emission industries surges, pressure on secure, sustainable REE supply chains continues to grow.
Queensland is emerging as a strategic player in the rare earths sector, with an estimated 8,800kt of reserves across five major prospective projects. A standout is Ark Mines, an Australian company developing the Sandy Mitchell Rare Earth Project in northern Queensland. As the first surface-expressed rare earth deposit with a JORC-compliant resource listed on the ASX, Sandy Mitchell represents a significant new domestic supply opportunity for magnetic rare earths such as neodymium and praseodymium, critical inputs for clean energy and advanced manufacturing.
The project covers an estimated 1.3 billion to 1.6 billion tonnes of monazite-rich sands, with no overburden, blasting or underground development required. Mining is simple, low-cost, and can be undertaken with a conventional loader. Beneficiation test work has confirmed that the deposit can be upgraded via low-energy gravity separation to produce a concentrate with up to 51.9% total rare earth oxides (TREO), using a closed water circuit and generating no tailings dam or permanent waste piles. The landform can be returned to its original state post-mining, aligning the project with leading environmental and social standards.
A key enabler for downstream processing is RZ Resources’ Mineral Separation Plant (MSP) in Brisbane — the only facility of its kind on Australia’s east coast. With capacity to process 400,000 tonnes of heavy mineral concentrate annually, the MSP can produce high-grade titanium, zircon and rare earth concentrates domestically, helping reduce reliance on offshore processing and strengthening Australia’s critical minerals supply chain.
With pre-feasibility work underway and strong ESG credentials, Ark Mines is actively seeking offtake agreements, investment, and strategic partnerships to bring Sandy Mitchell into production. Together with emerging infrastructure such as the RZ MSP, the project could help establish Queensland’s first commercial rare earth production— delivering a secure, ethical, and globally competitive supply chain for the energy transition and next-generation technologies.
Support for mining and processing critical minerals and rare earths
In the drive for critical tech, there are multiple challenges ahead in the battery minerals and rare earths. In Queensland, collaboration is essential to overcoming these obstacles and facilitating progress, with opportunities to partner with universities to further research and develop new concepts.
Critical Minerals Queensland (CMQ) can also help to remove many of the hurdles with critical minerals, build contacts, and connect investor with Queensland opportunities. CMQ supports the industry and investors to engage with the Queensland Government in this specialist field.
“You’ve got people that you can rely on and that you can build relationships with to help grow the company,” says Peters.
Alongside the abundant resources is Queensland’s world-renowned mining industry, which is backed by robust government support and business-friendly policies. In the last two decades, Queensland Government investments in R&D and innovation have exceeded A$8bn. In addition, the private sector has invested more than $139m in mining R&D.
Townsville is a key area of focus for investment. Based there is the Queensland Resources Common User Facility (QRCUF), which is being set up to accelerate commercial projects for Queensland critical minerals projects
Already with a highly skilled workforce in the state, the Queensland Government is also investing to expand the skills base further.
“It’s something we do well in Queensland. We know how to mine with, we’ve exported resources for a very long time, and we have a good infrastructure,” says Malone. “We’ve got an effective way to do it. We’ve got good policies – we’re built around that, and there’s a lot of support for critical minerals in Queensland.”
“Queensland has a long history in mining materials. We’ve got the skill set, we’ve got the capability, we’ve got the approvals pathway. The state is ready for business,” adds Peters.
To learn more about the opportunities in battery materials and rare earths for critical minerals, download the document below.