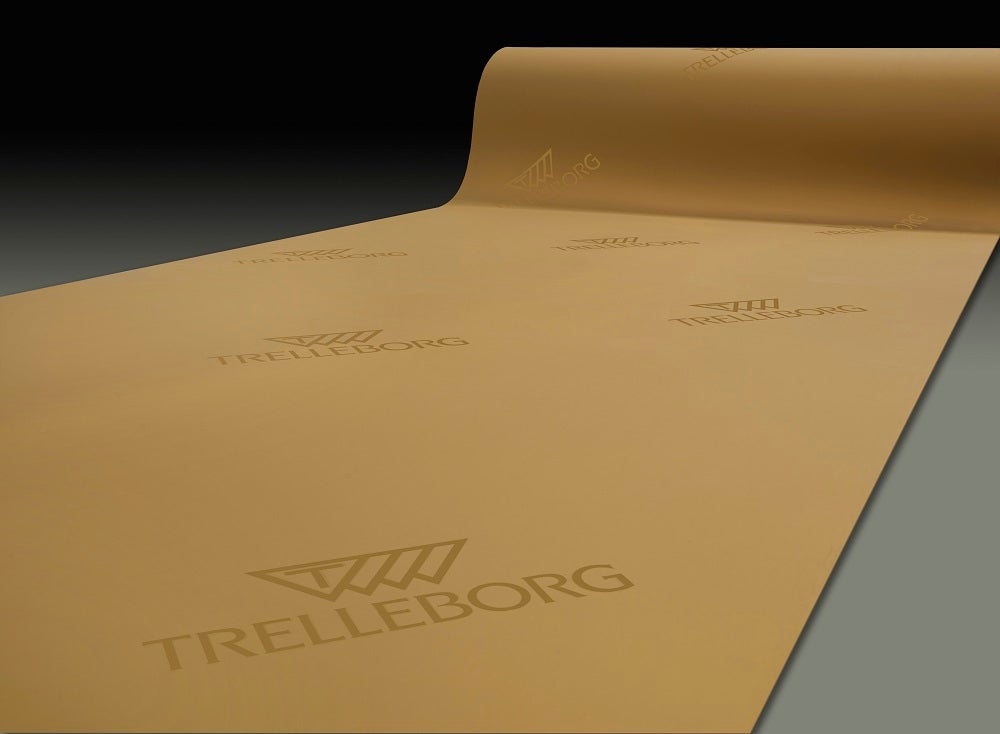
Selecting and specifying abrasion resistant sheet rubber to protect carbon steel piping systems, chutes and launders from slurry abrasion is a complex challenge. Volumetrically, mineral processing plants need to treat greater slurry volumes when processing lower grade ores, the design and footprint of modern processing plants are compact leading to turbulent slurry flow and the abrasive profile of mineral laden slurry is governed by so many variables that interact with each other causing abrasion.
The objective is to minimize abrasion to extend service life, reduce downtime and improve equipment availability, according to Trelleborg business development manager Keith Jones. “We aim to avoid process plant operators having to shut down outside scheduled maintenance periods to perform remediation work on equipment or rubber that has worn out prematurely,” he explains. “Improving this element is a way to add value to operations by extending service life, reducing downtime and improving equipment availability.”
Strength and resilience
Traditionally, the mining and mineral processing industry has adopted and specified sheet rubber that is high in natural rubber content to line and protect carbon steel piping systems that transfer slurry from one stage of mineral processing to the next. Lining rubbers, high in natural rubber content do provide extremely good elastic properties. They deal with a range of entrained slurry particle impingement angles, are relatively soft on the Shore ‘A’ hardness scale, have good compressive strength, rebound resilience, tear strength, and elongation at break properties.
These rubber attributes have a track record in abating slurry abrasion in mineral slurry processing circuits and providing the necessary protection to carbon slurry pipe spools, chutes and launders when bonded to their internal surfaces.
Over many years, international rubber abrasion testing standards have helped engineers and specifiers to assess rubber loss and rank sheet lining rubber compounds with high natural rubber content based on discrete laboratory tests. These days, the general performance theme associated with rubber selection for slurry service follow many of the physical and mechanical rubber attributes mentioned above and how well rubber compounds rank relative to each other based on laboratory abrasion test campaigns.
Indeed, rubber sheet high in natural rubber content is used extensively throughout mineral processing circuits to protect mill discharge equipment, screen undersize chutes, cyclone feed piping, launders, tails thickening equipment and tailings pipework.
Premium natural rubber
Trelleborg has long understood the limitations of sheet rubber compounds with high natural rubber content operating above room temperature and the need to provide mineral processing operations around the world with improved abrasive solutions. The effect of elevated temperature on the abrasion loss values used to historically rank these class of rubber compounds for service is largely inadequate. Modified rubber abrasion loss test methods prescribed in ASTM D5963 and ISO DIN 4649 with water lubrication are routinely the go to test methods that have helped engineers and rubber specifiers through the sheet rubber compound selection process.
These test methods are run at room temperature and Industry has adopted these tests and results as the barometer to rank rubber loss and loosely correlate laboratory results to likely rubber performance in abrasive mineral slurry service. The validity and reliance on data generated must be assessed with caution. For example, mineral processing plants operating in temperate, arid, and tropical environments for the most part have mill discharge slurry temperatures significantly higher than laboratory room temperature abrasion test campaigns
Over the past decade, polymer scientists at Trelleborg have dedicated much of their time, research and expertise towards the formulation and compounding of premium natural rubber sheeting to deliver high levels of abrasion resistance at elevated temperatures. GoldLine® Premium 38 abrasion resistant natural rubber sheeting ticks all the boxes. It possesses all the physical and mechanical attributes expected of an abrasion resistant sheet rubber compound. However, GoldLine® has a significant advantage compared to competing premium abrasion resistant sheet rubber alternatives. It has exceptional abrasion resistance not only at room temperature but more importantly for engineers, technical specifiers, production, maintenance and reliability personnel, exceptional performance at elevated temperatures too.
“Arguably, the largest challenge we faced during the development of GoldLine® Premium 38 was finding an international standard that would allow us to test and verify rubber abrasion loss values at elevated temperature. There just aren’t any,” says Jones. “So, in parallel with our sheet rubber formulation, compounding and product development programme for GoldLine®, we embarked upon an extensive review of known standards and their abrasion loss test methods all of which resulted in Trelleborg designing and building our own abrasion loss equipment now known as Submerged Elevated Temperature Abrasion Testing or SETAT® for short. The addition of the SETAT® test cell helped us to optimise the GoldLine® compound formulation and balance the abrasion properties we wanted to achieve at elevated temperatures,” concludes Jones.
A Comparison of Abrasion Test Standards and Methods
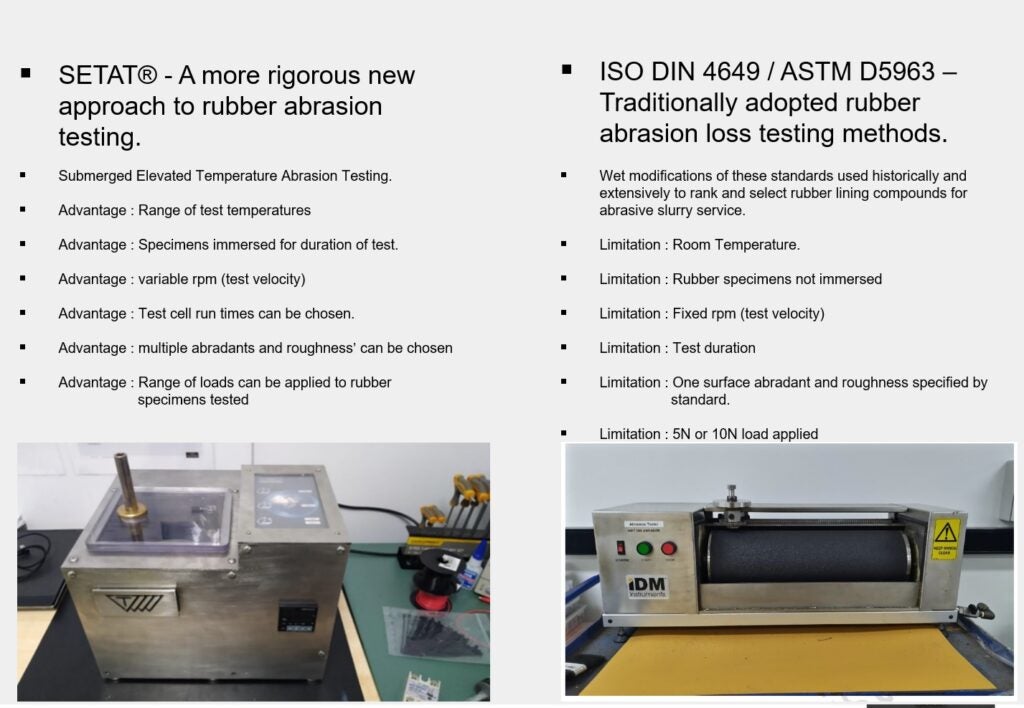
Abrasion Test Results
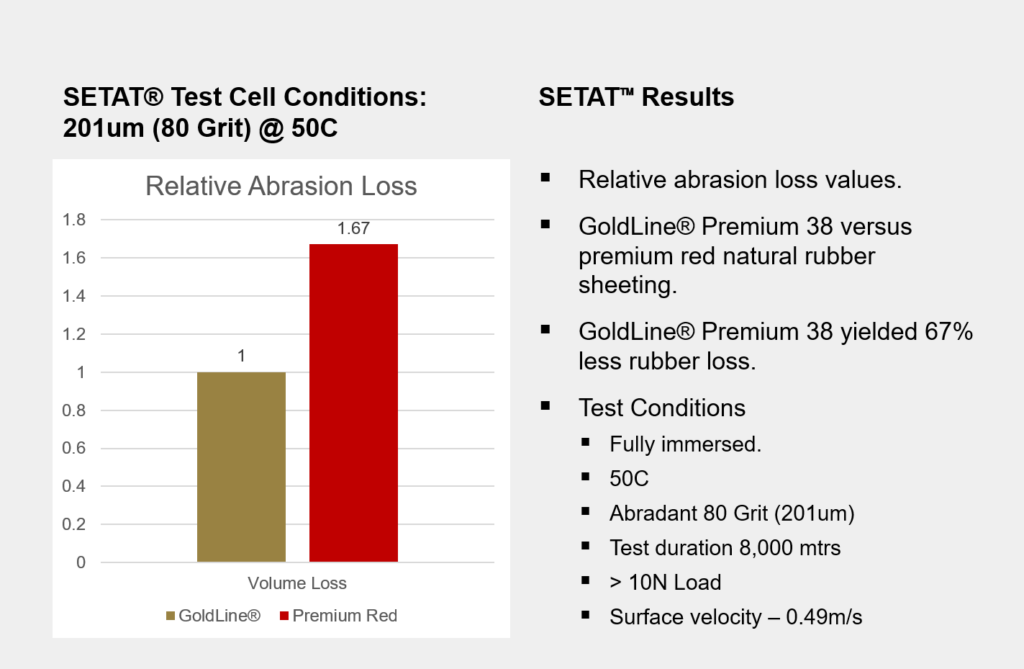
The flexibility to vary abrasion test parameters is providing engineers, rubber specifiers, maintenance, production, and reliability engineers with far greater insight into performance of abrasion resistant sheet lining rubbers in different areas of their mineral processing plants. SETAT® is proving to be a valuable tool in assessing current plant wide rubber selection philosophies to ensure fixed and rotatable assets are more appropriately protected from slurry abrasion and premature failure.
GoldLine® Premium 38 is also delivering and helping 24/7 mineral processing operations to contain costs and stay ahead of the cost curve by reducing $/tonne of ore processed by reducing unplanned and costly downtime associated with replacing equipment lined in less abrasion resistant rubber compounds outside scheduled maintenance periods.
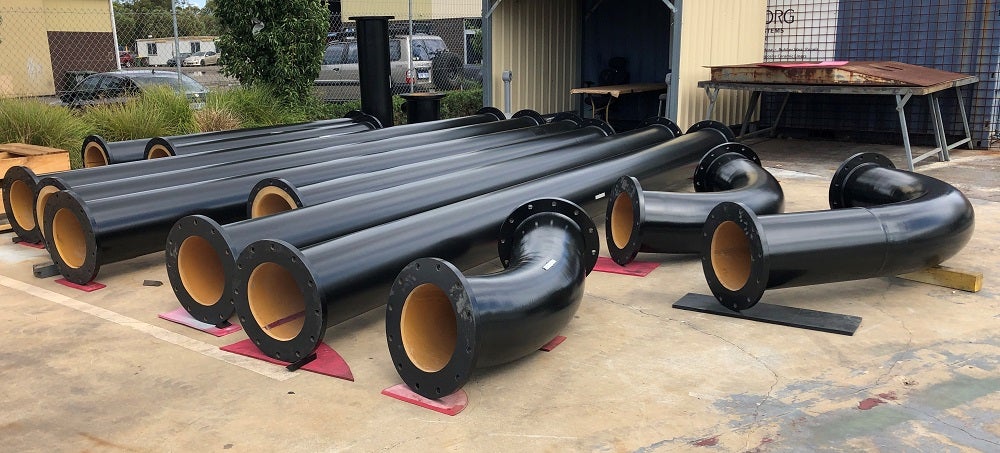
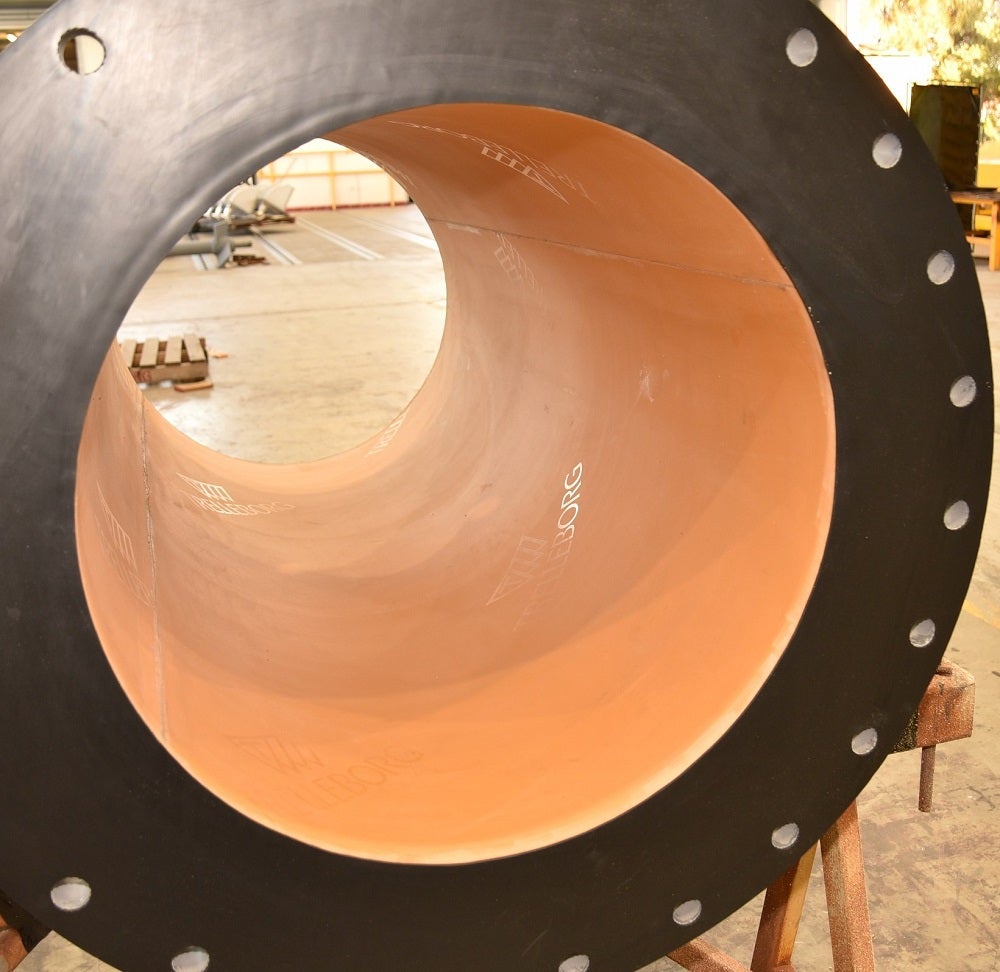
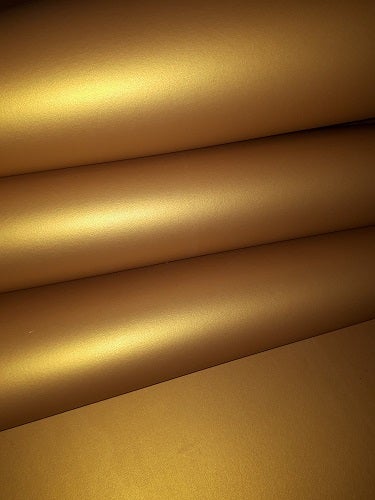