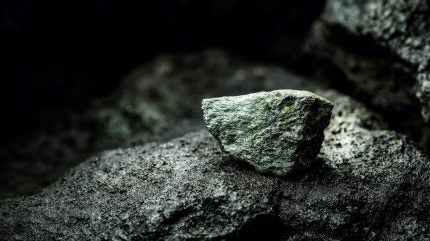
When it comes to next-generation battery technologies, lithium dominates discussion. Yet an equally important and sometimes overlooked element in the creation of these essential technologies is graphite. Crucial for both safety and performance, graphite can make up as much as half of every lithium-ion (Li-ion) battery’s weight.
According to the International Energy Agency, graphite demand will double by 2040 in the stated policies scenario, with 49% of demand expected to come from energy technologies.
Yet the global supply chain remains reliant on time-consuming and high-emitting production methods, the bulk of which are performed in China. Meeting the supply-demand gap is an acknowledged necessity in scaling up batteries, but doing so will require cleaner, faster and more scalable methods of production.
Enter RapidGraphite, a Perth-based start-up co-founded by Curtin University materials scientist Dr Jason Fogg. The company has developed a novel method that turns waste carbon from biomass feedstocks into high-purity synthetic graphite, in a faster and more sustainable way than ever before.
Last year, the company received a grant to scale up its tech as part of Curtin University’s A$18.6m ($12.2m) Venture Studio initiative, with the process to commercialisation well under way.
We spoke to Fogg about the company’s innovation and what it could mean for Australia’s graphite supply chain.

US Tariffs are shifting - will you react or anticipate?
Don’t let policy changes catch you off guard. Stay proactive with real-time data and expert analysis.
By GlobalDataScarlett Evans (SE): Why is graphite important?
Jason Fogg (JF): Graphite has been used throughout history, but today, demand is being driven almost entirely by Li-ion batteries. Around a quarter of every Li-ion battery’s weight is graphite, and that is actually looking conservatively at it – you can get batteries with up to 50% of their weight being graphite. When you look at a typical electric vehicle battery, you are looking at roughly 70kg of graphite.
Graphite is the main component that makes it safe enough for us to use Li-ion batteries in our everyday lives. Without it, the batteries are actually quite explosive.
As with most critical minerals, or those minerals we need for batteries in particular, the demand is far outpacing our supply capabilities.
SE: What are the current challenges with producing graphite?
JF: There are two main ways to get graphite. You can use conventional mining processes to dig it out of the ground and get natural graphite, but this then has to be purified to make it in batteries, which need material at more than 99.95% purity. Graphite mines are usually at a few tens of per cent purity, so you lose a massive amount of what you dig before getting something appropriate for a battery.
The main way graphite is purified uses an extremely dangerous acid called hydrofluoric acid. While it is a cost-effective purification approach, it is extremely dangerous for workers and causes catastrophic environmental damage.
Alternatively, a synthetic graphite can be manufactured by heating specific carbon materials to 3,000°C, which is about half the surface temperature of the sun. This is an incredibly energy-intensive process that emits 15–25kg of CO₂ for every kilogram of battery graphite produced. It requires significant baseload power, which also makes it really hard to integrate renewables, which are inherently intermittent.
How the world currently gets graphite is really an ugly underbelly of what is an incredibly important battery mineral.
So this is the context. We simply need more and more batteries, they are the key to unlocking renewable energies, but we need cleaner ways of doing it – and that is where RapidGraphite comes in.

SE: How does RapidGraphite hope to meet this challenge?
JF: We have developed a catalyst approach that allows us to make a sustainable synthetic graphite using less energy than conventional techniques and in a far faster process. We use a bio feedstock, such as wood chips or leaf litter, which is a sustainable and abundant feedstock that we source as a waste product from Australia’s existing wood supply chain. Our catalyst then essentially converts the carbon from this waste product directly into battery-grade graphite.
Typically, there are a lot of defects in most feedstocks that prevent the carbon from ever turning into graphite. Our new catalyst allows us to target the key defects, remove them, and therefore allows the feedstock to be converted into high-purity graphite.
SE: What stage is the project at now, and what are the next steps toward commercialisation?
JF: We are in the scaling-up phase. We have proven our technology in the lab and are now progressing to battery-scale testing.
We have negotiated with the university to spin the tech out as RapidGraphite, and with support from the Resources Technology and Critical Minerals Trailblazer we are gaining access to larger furnace facilities to test the technology at a pre-pilot scale. From there, we are raising capital to push towards a full pilot and bring our synthetic graphite product to market.
SE: What are the main challenges when looking at scaling up the technology into a commercially viable product?
JF: Timely access to scale-up facilities is the largest hurdle. Given that RapidGraphite is only just spinning out of the university setting, it is fair to say we are in quite an early stage. So, we recognise that to take our place within the market we need to move through the scale-up stages quite quickly.
Being so early can also be a unique advantage, though, as we can be quite nimble in developing and refining our approach to synthetic graphite manufacturing.
SE: Does Australia have any particular advantages in deploying this tech?
JF: A unique point about Australia is that we receive the highest amount of year-round solar irradiance in the world. Most Aussies would see this by the number of clear sunny days we get, even in the peak of our winter.
Given the short processing times used in RapidGraphite’s technology we could utilise Australia’s world-leading solar energy potential to power our synthetic graphite manufacturing.
However, given the power supply is simply a plug-in to the RapidGraphite process, we can also see how the technology can be deployed around the world to rapidly develop graphite supply capabilities using locally available feedstocks.
SE: Is there strong investor interest in sustainable graphite technologies like yours?
JF: Battery-grade graphite supply chains have seen considerable instability due to geopolitical tensions. Chinese supply dominates more than 90% of the global market, and export restrictions have raised sovereign risk questions. We know that Li-ion batteries are at the core of our energy future; this places a secure and sustainable supply of graphite at the forefront of the conversation.
In this context, we have seen a lot of investment interest in creating new ways of producing graphite, and there are government incentives to push out new tech. However, the road to market is still a tough one, and over the next few years in graphite we will really need to answer some hard questions about how we can supply battery graphite in a clean way.
In the past, we may have been able to overlook how things were made, but that is no longer sustainable – ethically, environmentally or economically. We have to rethink how we source and manufacture the materials powering our future.