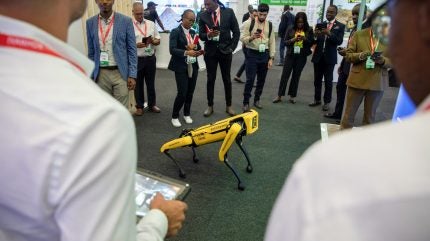
Analysis from GlobalData suggests that the use of robotic dogs is becoming widespread in emergency use cases, but it also highlights other mining applications.
Since early trials started around 2020, quadruped robots have been demonstrated at several mines globally. Equipped with sensors such as light detection and ranging (LiDAR), thermal cameras, gas detectors and portable X-ray fluorescence, the robots can carry out tasks such as remote inspections, environmental monitoring, equipment surveillance and spatial data acquisition with high precision.
Discover B2B Marketing That Performs
Combine business intelligence and editorial excellence to reach engaged professionals across 36 leading media platforms.
Nasser Madani, associate professor at Nazarbayev University School of Mining and Geosciences in Kazakhstan, explains that “the ability of quadrupeds to navigate complex and hazardous terrains such as underground tunnels, unstable slopes, or tailings facilities makes them ideal for tasks that would be risky or impractical for humans”.
Additionally, the robots also provide continuous and repeatable data collection ─ something that is becoming increasingly important to miners for applications such as predictive maintenance.
Predictive maintenance is a near-term investment focus for almost to half of the mines surveyed by GlobalData, Mining Technology’s parent company, last year.
Using robotic dogs in mines
Several mining majors have tested or are already using robotic dogs in their mining or processing operations.

US Tariffs are shifting - will you react or anticipate?
Don’t let policy changes catch you off guard. Stay proactive with real-time data and expert analysis.
By GlobalData“At Glencore’s Kidd Creek mine in Ontario, Canada, Boston Dynamics’ Spot assists in conducting inspections in hazardous underground areas, reducing the need for humans to undertake dangerous tasks,” says GlobalData.
Spot has also been demonstrated at LKAB’s Kiruna mine in Sweden, in collaboration with the Luleå University of Technology. Through that project, Spot helped to produce digital twins of the mining tunnels using LiDAR scanning, becoming an integral part of inspections.
The robot acted as a mobile base for a drone, enabling scanning of areas that are inaccessible by foot to ensure the safety of tunnels.
Over the past three years, Dwyka Mining Services, which operates across Africa, has also worked with Spot in what it describes as “some of the dirtiest, darkest and dustiest corners of mining”.
Jamie van Schoor, CEO of Dwyka, says early adopters such as Anglo American’s Amandelbult Tumela platinum mine and Rosh Pinah Zinc “have helped catalyse a mindset shift in Africa”.
Dwyka sees three typical use cases for robotic dogs: inspection of ‘no go areas’ such as post-blast or unstable areas; manoeuvring in constrained crawl spaces and legacy stopes that defy traditional human and drone access; and routine and repetitive inspection tasks that can benefit from automation.
“As mining operations go deeper and conditions become more extreme, robotic platforms like Spot bridge the widening chasm between data requirements and safe access,” says van Schoor.
Meanwhile, Julian Mackern, senior go-to-market manager at ANYbotics, another developer of quadruped robots, explains how its system can be used to inspect active conveyor belts, which is often too dangerous for a human.
“ANYmal can safely navigate alongside an active conveyor belt, identifying faulty parts of the belt, pulleys and rollers, to identify any issues before they become costly equipment failures,” Mackern says.
ANYbotics is working with Vale at its Cauê iron ore mine in Brazil. There, ANYmal has been used to inspect belts, machine rooms and milling machinery, collecting thermal images, audio samples, and photographs of gauges, dials, levers and other equipment.

In research and fieldwork, such as in legacy tailings projects, robotic dogs have been considered for collecting geochemical data to support resource modelling and improve estimation accuracy, especially in locations where conventional sampling is limited.
Earlier this year, LTU revealed it had tested its autonomy stack at the Grecian Magnesite underground mine to collect LiDAR point cloud and visual data on an abandoned area of the mine. The data collected as part of the EU-funded PERSEPHONE project offers valuable insights into the unique conditions of abandoned mines, characterised by narrow passages and complete darkness, a significant contrast to active underground production areas.
Evolving use cases for quadrupeds
Since their initial trials at mine sites several years ago, Madani says the adoption of quadruped robots in the mining sector has “grown steadily but remains in the early stages of widespread implementation”.
Furthermore, since the initial proof-of-concept demonstrations that mainly focused on safety inspections in hazardous areas, the role of robotic dogs has expanded. This is largely thanks to improvements in sensor integration, autonomy and ruggedisation, the associate professor says.
Madani explains that majors are now exploring the use of quadrupeds in operational environments “for tasks such as geotechnical monitoring, ore control, and data acquisition in tailings and underground areas”. These applications are supported by the robots’ ability for live offloads, real-time maps and route-based data collection offered by many systems.
Mackern explains that ANYmal has come a long way since its first deployment, after years of training its AI models. “Thanks to significant computational improvements, ANYmal can also translate visual information, like reading a gauge, into data with much greater precision and speed,” he adds.
Overcoming challenges from dirt to data
Deploying robotic dogs in mining environments presents several challenges including navigating rough terrain, maintaining stability in wet or loose-ground conditions such as tailings or muck piles, limited battery life, and communication issues in underground or remote settings.
Dust, humidity and temperature extremes can also affect sensor performance and hardware durability.
To address these issues, Madani says manufacturers are enhancing locomotion algorithms for better terrain adaptation, integrating swappable high-capacity batteries and using ruggedised enclosures to protect electronics.
For example, ANYmal is IP67 rated, meaning it can operate in dusty and humid conditions – a common challenge in mining operations.
Also, while quadrupeds can traverse dusty, slippery or muddy surfaces and climb stairs, “near-vertical ladders”, “large water bodies” and “deep mud” still pose issues, according to Dwyka.
Manufacturers are enhancing locomotion algorithms for better terrain adaptation, integrating swappable high-capacity batteries and using ruggedised enclosures to protect electronics.
Network constraints pose another hurdle, as van Schoor explains. “While Spot can operate offline on pre-programmed AutoWalks, the real power comes alive with Orbit [Boston Dynamics’ fleet management and data analysis software], and pervasive Wi-Fi or LTE [long-term evolution] to enable rerouting, data offload, and mission oversight and alerts.”
For underground use, mesh network systems and autonomous return-to-base functions are being developed to improve connectivity and reliability, Madani adds.
Mackern, however, says it is not necessarily the performance of the robots themselves that customers struggle with, it is managing the data collected.
“After ANYmal gathers information from numerous points of interest, visualising and sharing that data becomes a real challenge,” he says, adding that this led to the launch of Data Navigator, an asset management platform that can help miners develop preventive maintenance strategies.

The outlook for quadrupeds in mining
Over the next three to five years, the use of quadruped robots is likely to evolve from being a niche application in mining to a more widespread one.
Madani suggests that as sensor payloads become more specialised and integration with mine digital twins improves, quadruped robots will enable high-frequency, high-resolution data collection in areas that are unsafe or inefficient for human access.
“Their role will likely expand into routine pre and post-blast assessments, tailings monitoring and real-time mapping of inaccessible zones, supporting more adaptive and predictive mine planning,” says Madani.
“We can also expect tighter integration with AI-driven analytics to automate data interpretation, making quadruped robots essential for safer, smarter and more efficient mining operations.”
Van Schoor also believes the next three to five years will “mark a tipping point, not just in adoption but in how we design mines for technology, not just with it”.
He sees this future comprising pervasive connectivity (with Wi-Fi and LTE deployed throughout mining operations) as well as cobot ecosystems (where drones scout verticals and quadrupeds explore horizontals, resulting in a unified digital twin).
“As digital toolboxes evolve, we will see swarms of ground and aerial robots working in tandem, each purpose-built for a different job,” concludes van Schoor. “This isn’t automation replacing humans; it is augmenting them with a flexible, responsive fleet of helpers that makes mining safer, smarter and more sustainable at extreme depths.”
Frequently asked questions
-
What are quadruped robots and how are they used in the mining industry?
Quadruped robots, often referred to as 'robotic dogs', are advanced robotic systems designed to navigate challenging terrains and perform various tasks in mining operations. These robots are equipped with sophisticated sensors, including LiDAR, thermal cameras, and gas detectors, enabling them to conduct remote inspections, environmental monitoring, and equipment surveillance with high precision. Their ability to traverse hazardous and complex environments makes them ideal for tasks that are risky for human workers, thereby enhancing safety and efficiency in mining workflows.
-
What benefits do robotic dogs provide for mining operations?
Robotic dogs offer numerous benefits to mining operations, including improved safety, efficiency, and data collection capabilities. By performing inspections and monitoring in hazardous areas, they reduce the risk to human workers. Additionally, these robots facilitate continuous and repeatable data collection, which is crucial for predictive maintenance and operational planning. Their integration into mining workflows allows for real-time mapping and data acquisition, enabling miners to make informed decisions and optimise their operations.
-
How do quadruped robots enhance safety in mining environments?
Quadruped robots significantly enhance safety in mining environments by taking on tasks that are dangerous for human workers. They can navigate unstable terrains, such as underground tunnels and post-blast areas, reducing the need for personnel to enter hazardous locations. By conducting inspections and monitoring equipment in these high-risk zones, robotic dogs help prevent accidents and injuries, thereby fostering a safer working environment for miners.
-
What challenges do quadruped robots face in mining applications?
While quadruped robots are effective in mining applications, they do face several challenges. Navigating rough terrain, maintaining stability in wet or loose conditions, and managing limited battery life are some hurdles. Additionally, communication issues can arise in underground or remote settings, potentially affecting their operational efficiency. Manufacturers are actively working to address these challenges by enhancing locomotion algorithms, improving battery technology and developing robust communication systems to ensure reliable performance in demanding mining environments.
-
What does the future hold for quadruped robots in the mining sector?
The future of quadruped robots in the mining sector is promising, with expectations of widespread adoption over the next three to five years. As technology advances, these robots will likely play an increasingly vital role in routine inspections, tailings monitoring, and real-time mapping of inaccessible areas. Enhanced integration with AI-driven analytics will automate data interpretation, making robotic dogs essential tools for safer and more efficient mining operations. The evolution of co-bot ecosystems, where these robots work alongside drones and other technologies, is expected to further transform mining practices, leading to smarter and more sustainable operations.