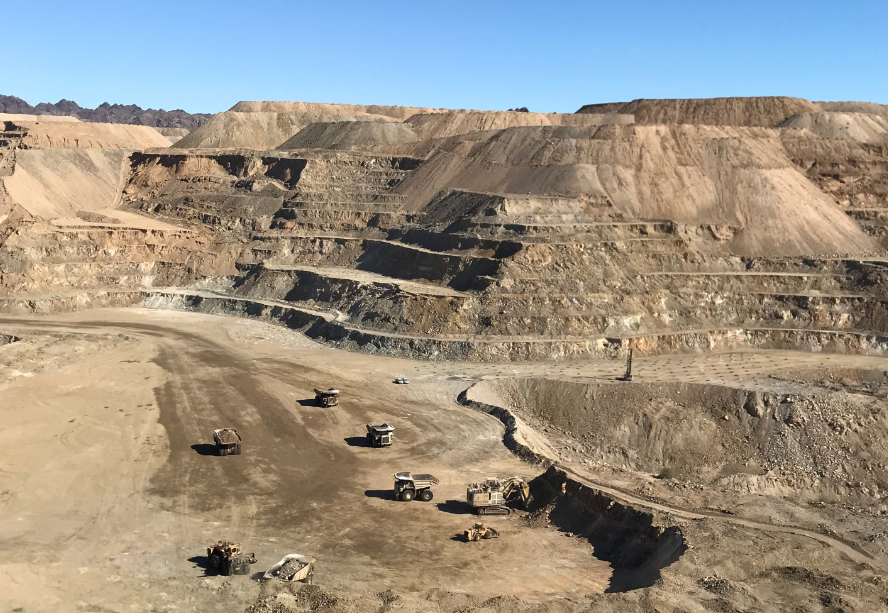
Equinox Gold is a multi-asset mining company that produces gold from its Mesquite Gold Mine in California. The company also operates mines in Brazil and at its Castle Mountain project in California.
Demetra Johnson has worked in the safety department at Mesquite Mine since 2007. In her current role she spends her time developing and improving safety management systems, working with employees, keeping senior leadership informed and up to date with regulatory changes.
Please tell me about the company’s ethos and approach to keeping its miners safe?
Demetra Johnson (DJ): At Mesquite Mine we believe in doing it right the first time and every time. Our general manager, Jeff Fuerstenau, ends every meeting with every group asking: “how do we do things?” and the group responds: “safe and right!”
Part of doing it right is doing it safely. We have multiple employee-level committees that empower the front line to be involved in making changes, setting direction and identifying opportunities for continual improvement of the safety program. We are very committed to safety training and believe compliance is the floor not the ceiling. We often bring in outside trainers and send our own employees to become trainers to ensure the best training is provided across all departments.
In your opinion, what has been game-changing for improving safety at mine sites?
DM: Having a core group of employees at a site who want to work as a team, who want to see the mine succeed and who take pride in the company’s safety record is vitally important. Leading by example is very important, but everybody needs to buy in to the safety program and there needs to be a culture of shared responsibility.
There have also been several industry shifts that have improved mine site safety. For example, an increase in regulatory oversight and frameworks over the last 50 years, which has increased the onus on companies to place a high importance on safety.
Furthermore, the safety profession has focused more on human behaviour, recognising that the number one cause of incidents is unsafe behaviour rather than unsafe conditions. This has encouraged site level management and safety professionals to focus on training,
Additionally, the change toward using safety management systems has also had a positive impact. These systems have come a long way in recent years and encouraged companies to look at safety from an integrated perspective, with every team in putting their goals, planning implementation process, and measuring their performance.
It’s often said that people are the biggest hazard at a mine sites, how do you get employees to consistently act in the safest way possible?
DM: Fatigue and lifestyle, long work hours, long travel to and from the site, long hours driving at work, poor nutritional habits, family life and lifestyle practices while away from work all affect safety at the mine site.
This is why we include health and safety training on topics well beyond our compliance obligations and our employee’s day-to-day job responsibilities. We take a holistic approach to worker safety, with the mantra that a healthy worker is a safer worker.
Complacency gets people hurt. Our workers must remain vigilant and focused, assessing each task and each trip from a fresh perspective. At the beginning of every shift we must ask ourselves “what could hurt me today” and “what could hurt my co-worker if I leave this for the next shift.”
Thinking to the future, what new developments could make mining safer?
DM: I am excited to see what technology does for mining in the next 5-10 years such as fatigue management systems, emergency simulation for mine rescue or firefighting. We, as a mining community, have a pretty good grasp on what can hurt and injure us today. But it’s what we can’t see that we need to be extra careful of, and I think that’s where technology will improve over the next several years.
I’m expecting advances in industrial hygiene technology and better ways to protect employees from chemicals and hazards in the air and water. Mesquite is located in southern California and it can get really hot at site. Improvements in PPE, with cooler vests, uniforms, boots, hard hats and safety glasses for those working in extreme heat for long hours would be great developments.
What are your plans for the year ahead for mining safety procedures or equipment?
DM: Reviewing procedures and not letting them become stale or irrelevant is important. In the coming year we plan to review key safety programs with all end users, looking for feedback on use, relevance, and adequacy, and then we’ll implement changes as needed.
We will also continue to assess the behaviours and decision-making processes that take place onsite for everyone, including contractors, and focus on our objective of sending everyone home safely at the end of each shift.
Mining Technology’s Mining Safety content is supported by USA mining safety specialists Carroll Technologies Group.