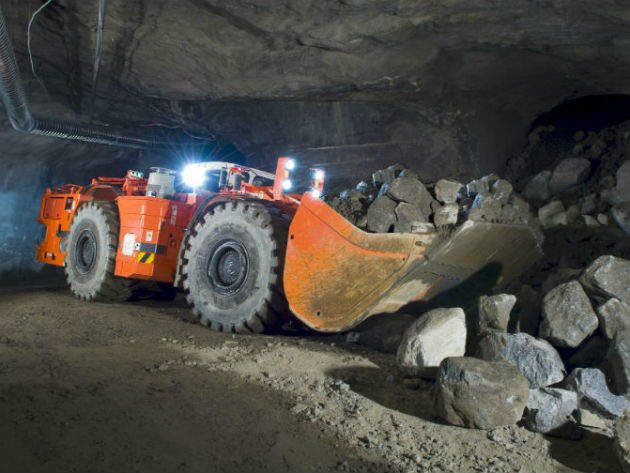
The days of pit ponies and caged canaries – the stock in trade images of the mining industry until well into the twentieth century – are long gone. Since then, new technologies began and are continuing to transform the industry. From today’s ‘digital mine’ that’s redefining approaches to analytics and dynamic scheduling to integrated automation and cloud-enabled mobility, mining companies are increasing productivity and reducing costs at an unprecedented rate.
But one area that has eluded automation for years is the loading process of the underground LHD vehicles themselves. The challenge has always been how to create an automated system with the ability to effectively gauge the difference in size and configuration of rock piles as the loads are continually dispersed. Progress is also being stalled by underground conditions, which typically render camera technology ineffective by preventing the system from being able to ‘see’ the rock piles.
Robotic tactile technology
A radical new technological breakthrough called auto-tunable robotic loading (ATRL), which is due to be rolled out later this year, may finally have cracked the problem.
The technology is the result of a unique collaboration between Queen’s Mining Systems Laboratory (MSL) in Canada; Örebro University‘s Centre for Applied Autonomous Sensor Systems in Sweden; and Atlas Copco Rock Drill, also of Sweden. The key difference is, ATRL allows automated LHD vehicles to ‘feel’ rather than ‘see’ the rock pile, and make their adjustments accordingly.
The ATRL system is based on a new development pioneered by MSL researchers, led by Joshua Marshall and Heshan Fernando, which uses admittance control. This views robotic loading from the perspective of modulating the admittance, i.e. the force / velocity relationship between the loader and rock pile. This tactile solution empowers the machine to work in dark and dusty environments without the need for camera technology.
Half-way to sorting automation
Marshall explains that, “The feeling is done by the existing sensors in the machine’s hydraulic cylinders. As the bucket moves in, forces push on it and the pressures change on the cylinders and we use those pressure signals to tell us about the level of bucket / rock interaction.” The aim is to ensure there is just enough bucket / rock interaction for the bucket to be filled. If there is too much force the bucket will get stuck: too little and it won’t be filled properly.

US Tariffs are shifting - will you react or anticipate?
Don’t let policy changes catch you off guard. Stay proactive with real-time data and expert analysis.
By GlobalDataThe challenge facing the team cannot be underestimated. LHD automation is complex and, typically, a remote-steered LHD vehicle can be equipped with up to 150 sensors. An MSL source said: “We are now half-way there and so far we have had some really great success. Our achievements are in no small part due to generous and unprecedented access to Atlas Copco’s Kvarntorp underground test mine and use of their fully equipped and automation-ready ST14 and ST18 LHD machines.”
When rolled out, the system will be available as a software upgrade for all Atlas Copco LHDs. It will include the capability to collect data on each dig for operators to compare the results of manual and autonomous digging.
Parallel developments in underground mining tech
ATRL is just one of three areas of research into automated mine technology being carried by MSL and Örebro University. Work is also underway into how to use unmanned aerial vehicles (UAVs) in underground mining applications as, hitherto, UAVs in mining had been mostly limited to surface applications.
Harsh underground environments with restricted space and reduced visibility generally place similar operational constraints on the use of UAVs as LHDs. But now, a new auto-rotating cavity scanner concept is being developed. Prototyping and initial field testing is taking place on the Örebro University campus.
Meanwhile, another area of research that could be highly promising is the development of high-speed, autonomous driving of underground mining vehicles; a development based on an iterative learning path-following concept. Work is currently being carried out using Atlas Copco ST14 and ST18 underground loaders at Kvarntorp.
Atlas divests automotive arm
The mining industry is, by tradition, a conservative one and for years has been cautious about going down the automation route. However, the decision taken in January by Atlas’ board of directors to split the group into two listed companies, Atlas Copco and NewCo AB (the current working name), could propel the new company to the forefront of automation. NewCo will focus on mining and civil engineering customers and hold the existing Mining and Rock Excavation Technique business area, as well as the Construction Tools division and related automotive service operations.
On the other side, Atlas Copco will focus on industrial customers. The intention is to list NewCo AB on the Nasdaq Stockholm stock exchange, in the second quarter of 2018. In a note, Morgan Stanley commented that a separate, new mining equipment supply listing could become “the crown jewel of the industry…We see Atlas as one of the most significant beneficiaries of this theme”.
Rio Tinto’s ‘mine of the future’
Mining majors such as Rio Tinto and equipment giant Caterpillar are also starting to pick-up the gauntlet of automation. Under its ‘Mine of the Future’ programme, Rio Tinto has established a large fleet of autonomous haulage systems (AHS) trucks, autonomous drilling and an autonomous long-distance train haulage system at its Pilbara iron ore operations in Australia. The company is the world’s largest owner and operator of AHS trucks, having 69 in operation at Pilbara, which is set to increase over the coming years.
Caterpillar, meanwhile, is looking to expand its profile in the supply of autonomous mine equipment technology and is going head-to-head with its main rival Komatsu to be frontrunner in future autonomous-machine fleet tenders. Komatsu is already reaping the benefits of a huge, multi-year deal with Rio Tinto on fleet deployment.
Last year, the Japanese company stepped on to Caterpillar’s home turf with a $3.7bn takeover of US-based mining equipment supplier Joy Global. The transaction was first announced in July and received enthusiastic approval from Joy Global’s shareholders in October. Komatsu only makes surface-mining equipment, while Joy Global is the largest independent manufacturer of underground mining equipment.
In response, Caterpillar announced the expansion of its mine-automation programme in January. As well as developing autonomous mining truck technology, Caterpillar plans to increase focus on its capacity to retrofit Cat autonomous systems for competitor equipment. At the company’s facility in Arizona, it unveiled a project to adapt hardware and software for retrofitting the Komatsu 930E mining truck with Caterpillar’s autonomous technology. Caterpillar hauling product manager Sean McGinnis said several of the company’s current global fleet of 70 Cat 793F autonomous trucks have now been retrofitted to operate autonomously.
EU funds autonomous technology to 2020
The European Union is keenly interested in developing autonomous underground mining technology as part of its drive towards robotics under its Horizon 2020 work programme. It believes that autonomous machines can provide an improvement potential of 40%-80%.
“Mine Automation makes it possible to run an underground mine 24/7 and enhance the face utilisation”, according to the European Minerals Resources Confederation (Eumicon). At present, face utilisation in underground mines can be as low as 25%. An EU budget of €120m has been set aside for the Berlin-headquartered Knowledge and Innovation Community (KIC) activities in 2018, under a European Institute of Technology (EIT) initiative.
The EU’s larger SPARC programme, established in 2012 and running to 2020, is the union’s largest civilian robotics programme. It received €700m of funding from the European Community for 2014–2020 and triple that (€2,100m) from European industry for the same period. The remit, it says, is “to develop solutions which can give Europe the technological leadership in resource-efficient production of raw materials and create future perspectives for extractive industry with newly manufacturing technologies”.
Autonomous underground mining is one of the six areas of focus for SPARC. It overlaps and follows on from the EU’s 2011-2015 intelligent mine initiative. The various work packages aimed to develop innovative methods, technologies and machines to enable the efficient and safe extraction of minerals from deep-laying deposits.
These are undoubtedly exciting times for mining as emerging technologies are combining to make for a far less hazardous and more cost-effective industry. However, optimism needs to be tempered by the reality that mining companies’ capex is heavily dependent upon raw materials prices. And should the robust prices that started this year off once again slump for an extended period, it could negatively affect investment decisions on costly automation technologies.