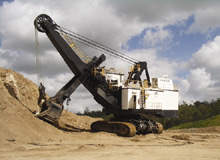
Anyone who has spent even the shortest amount of time in a working mine will know the adversity of the conditions that can exist. An often hostile climate combines with the localised tempests of dust, heat and mist caused by the processes of digging or drilling into the earth to create some challenging environments. Decisions made in such conditions where senses are severely limited (sight especially) have always been subject to significantly increased risk. There is now a universal desire to reduce that risk.
Lasers have found regular but limited use in mining automation applications (such as Load Haul Dump vehicles) and applications of millimetre-radar are under trial with some promise. However, difficult mining conditions still threaten the widespread use of both technologies. CSIRO’s ICT Centre identified the need to extend the potential use of these tools by establishing the performance parameters of scanning range sensors under adverse environmental conditions.
The goal is to be able to prove that the much wider and more sophisticated sets of data that can be gleaned from such conditions could be used to construct accurate digital models of the mine environment and, subsequently, to make accurate and appropriate control decisions for the operation of machinery.
Lab to field
CSIRO scientists, through the Minerals Down Under National Research Flagship, joined forces with CRCMining and the Australian Centre for Field Robotics (ACFR) to conduct a series of controlled laboratory experiments to examine the performance of three scanning range devices, two scanning infrared laser range finders and one millimetre-wave radar.
These experiments were undertaken as a requirement under an ACARP-sponsored Shovel Swing Loading Automation Project directed by CRCMining. The performance of the devices was tested in rain, mist and dust-cloud conditions far worse than any ever experienced in nature. Then the sensors were sent into the field and installed on a P&H 2800BLE electric rope shovel at the Bracalba Quarry, near Caboolture in Queensland.
The aim of these tests was to establish the relative merits of lasers and radar technologies under the environmental conditions likely to be encountered in a working mine, in order to perform mapping operations and data segmentation into the terrain surrounding the shovel, trucks in the vicinity of the shovel and the relative location of the dipper and truck tray.

US Tariffs are shifting - will you react or anticipate?
Don’t let policy changes catch you off guard. Stay proactive with real-time data and expert analysis.
By GlobalDataIn other words, the researchers needed to know if these sensors could provide enough accurate data to build a clear 360° digital model of the environment around the machine so a remote operator could ‘see’ clearly enough to make decisions for controlling the operation of the machine.
First results
According to Dr Eleonora Widzyk-Capehart, one of the authors of ACARP’s Minerals Down Under Stream Leader for Geologically Intelligent Surface Mining, lasers do appear to glean benefits.
“It was found that the lasers showed accurate and reliable target detection when visual targets were no longer discernible by passive means, such as video imagery,” says Widzyk-Capehart.
CSIRO ICT Research Scientist Adrian Bonchis, however, says there are boundaries to the technologies used.
“There is a limit to the level of obscurity through which the lasers were able to provide accurate ranging information. This limit was similar for both the Riegl and SICK lasers at a transmission of 92.5% per metre for bright targets closer than 25m,” says Bonchis.
Widzyk-Capehart adds: “The laser sensors can be blinded by the build-up of obscuring media, such as mud or dust film, on the sensor lens. The radar return was unaffected by the generated conditions of the controlled environment testing, showing robust behaviour. However, as a sensing technology, due to its wider beam-width, radar provides low range and angular accuracy by comparison to the laser systems.”
The research results show that the two sensing technologies are complementary and should be combined to provide a more robust representation of the surrounding terrain using the following:
- Radar returns to provide a rough draft of the surrounds in which significant obstacles (greater than 2m in size) are clearly identifiable as an obstruction (although not necessarily classifiable) and that is robust to adverse weather and dust
- Laser information to provide the detail of the surrounds, and other information required for tasks such as volume estimation, segmentation and classification of objects and obstacles
- Radar returns to determine when information provided by the laser sensors have been degraded by adverse environmental conditions such as rain, mist and dust
Widzyk-Capehart says it would be desirable to observe and assess the sensors’ performance over an extended time period in a production environment.
“Furthermore, it is suggested that any such testing should aim to incorporate as varied operating conditions as possible, including operation in significantly different ore types, for example, coal and iron.”
The gear
The three scanning range sensors tested as part of this study were:
- A Riegl LMSQ120 scanning laser rangefinder
- A SICK LMS291S05 scanning laser rangefinder
- ACFR’s prototype 95GHz millimetre-wave radar (2D HSS)
The two sensing technologies investigated in this study are considered complimentary because radar generates point-cloud type information that is robust to adverse environmental conditions, including heavy mist, rain and dense dust clouds. The measurements are of (relatively) low accuracy but sufficient for the provision of structure and large object segmentation.
A laser also provides a more easily interpreted measurement that is ideally suited to the creation of digital models of the surrounding terrain with high precision and accuracy.
The team’s ACARP report is called Performance of Laser and Radar Ranging Devices in Adverse Environmental Conditions and is the combined work of CSIRO scientists Nicholas Hillier, Julian Ryde, Eleonora Widzyk-Capehart and Mike Bosse, ACFR scientists Graham Brooker and Javier Martinez, and Andrew Denman from CRCMining.
This article first appeared in earthmatters, the magazine of CSIRO Exploration & Mining.