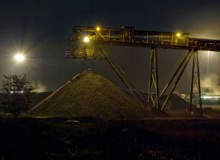
Each year, the global mining industry produces several billion tonnes of solid inorganic wastes or by-products through its mineral processing and metal production operations.
As a result, already enormous stockpiles of waste are growing exponentially as dwindling reserves push miners into increasingly diluted ore bodies. At the same time the environmental impact of mining operations is coming under intense scrutiny.
The global mining industry produced more than 80 million tonnes of red mud (a ferric hydroxide by-product of smelting and refining of some ores) in 2004 alone. Since 1979, more than 1.2 billion tonnes of red mud has been accumulated, posing serious challenges to alumina refineries and in some cases raising the ire of community and environmental groups.
In Australia, the CSIRO (Commonwealth Scientific and Industrial Research Organisation – the nation’s peak government research body) is working closely with the Centre for Sustainable Resource Processing (CSRP) on its ‘Towards Zero Waste’ project. The project aims to make the minerals and energy sector adopt a policy of zero emissions and zero waste by 2020, a target it says is required for living standards and environment to stay sustainable in Australia.
The concept is very much dependent on collaboration between different mining disciplines as well as range of other industries, governments and community organisations. The project runs off the premise that better education is needed to increase industry awareness of the potential for waste reduction.
For instance, it has been noted that producers often have only very limited knowledge of their sulphide tailings beyond that which they are required to know by law. A major shift in attitude is clearly required.

US Tariffs are shifting - will you react or anticipate?
Don’t let policy changes catch you off guard. Stay proactive with real-time data and expert analysis.
By GlobalDataProperly addressing waste in the tailings stream demands a big commitment on the part of producers to understand the individual characteristics of each of their various streams. While the alumina industry has been praised for its research into understanding the various properties and behaviour of its by-products, notably bauxite residue, other sectors are trailing way behind.
Making the most out of waste
Overall, waste management is emerging as a broad and multi-disciplined field. Researchers at the CSIRO and CSRP have been pulled from such areas as high temperature processing (bath smelting, melt chemistry, thermodynamic modelling), hydrometallurgy, mineral processing (mineralogy, characterisation, beneficiation), techno-economic analysis and life cycle assessment.
Experts in areas such as strategic analysis and application of methodologies helped to develop a decision support framework (DSF).
A methodology based on DSF was developed for prioritising various waste streams. A three-pronged selection criteria emerged: techno / economic; environmental; and social / political.
According to Dr Sharif Jahanshahi, with the CSIRO’s Minerals Down Under National Research Flagship, while technologies for extracting economic value from waste are in their very early stages, there are some positive signs emerging.
“Generally use of waste/by-products by the construction industry has been a successful practice,” he says. He notes for example that currently the Australian construction industry takes on average two million tonnes per year of slags from the steel industry to use either as substitutes for cement or aggregate/fillers.
Jahanshahi notes also that in Western Australia there are some large-scale projects trialling the use of by-products from the mineral industry as soil conditioner.
“This is a five to seven-year programme that is showing promising results, but is yet to be completed before wider scale adoption may be approved.”
He notes however that many recycling programmes are not yet as efficient as they could be and that cement fillers of soil conditioners inevitably still carry marketable materials.
“We do not always capture full value of the by-product through limited processing before using it for a particular application,” he says.
A recent report published by the CSIRO tabled and ranked 17 different mining waste categories. Receiving the highest ranking was sulphide.
Its high ranking is critically linked to the acid mine drainage factor. Tailings contain various base metal sulphides which have the potential to oxidise and form acids and produce acid mine drainage, presenting both short and long term environmental issues. It has been suggested that by cheaply and simply separating the sulphide component of the tailings stream into a low volume stream that environmental management would be greatly improved.
However, sulphide tailings do present significant challenges. Streams are normally very high volume whilst being very chemically and mineralogically complex as well as quite variable. Sulphide tailings are often very finely ground to maximise recovery during previous processing. Sometimes they contain composite or non-liberated particles, mixtures of valuable or gangue constituents, making processing or further upgrading quite difficult.
Extraction technologies
As part of Towards Zero Waste, a number of sulphide tailings samples, representing different ore types and base metal operations, were selected for assessment and testing using the strategy outlined above and a procedure / methodology was developed.
The procedure involved detailed characterisation and a sequential set of testing regimes based on separation processes such as water washing, classification, gravity concentration, magnetic separation, bulk flotation and others.
The preliminary data from four of the sulphide tailings assessed revealed that there are good prospects for separating sulphides from non-sulphides relatively cheaply and simply using mineral processing techniques, and that some of the tailings contain other valuable components, which could also potentially be recovered into marketable by-products.
Bauxite residue or red mud received the second highest score. The Bayer process is used for the extraction of alumina from bauxite ore via alkaline digestion, which produces a large volume of bauxite residue waste, commonly referred to as red-mud.
The use of red mud as feedstock in the construction industry or as soil conditioner in the agricultural industry has been recently considered and trialled. But commercialisation of these opportunities hasn’t yet been reached.
Over the last 50 years, efforts have been concentrated to extract valuable minerals from red mud such as iron, aluminium, sodium and titanium, but with very little success. The CSIRO’s Jahanshahi notes that better industry collaboration may see a reversal of fortunes here.
For the business and sustainability cases to become viable, one needs “collaboration across normal business boundaries: between alumina, steel, mineral sand and cement industries, so that the benefits of industrial ecology can be realised,” he says.
“Normally, each industry is interested in its core business rather than the value chain.”
Nevertheless, there continues to be significant effort invested in squeezing more value from red mud repositories and a number of processing steps have been proposed, through either hydrometallurgical or pyrometallurgical processes. There are three main examples of this:
- Alkaline roasting or sintering of red mud with addition of soda ash and lime at around 1,000° can successfully recover soda and alumina from red mud
- Reduction of iron oxide from hematite to magnetite (or metallic iron) at around 800° offers an opportunity to separate iron from red mud via magnetic separation
- Smelting of the red mud to recover iron has also been proposed and studied, often in combination with other processing steps to recover alumina and titania
It is thought that by separating red mud into distinct value streams, the maximum potential exists to convert the wastes into useful feedstock materials for the steel, cement, pigment and construction industries.
The concept that is being explored is based on a whole-system approach.
This includes a sequence of mineral processing, smelting and leaching steps designed to achieve the necessary physical and chemical transformations and separations in order to extract value from red mud.
Of course, dwindling resources across the board are forcing companies to develop better mining and processing techniques. While it’s nice to think that this may result in reduced waste volumes, the opposite is just as likely as miners are forced to dig deeper and wider to recover minerals.
Future implementation
An area of mining which draws particular scrutiny in terms of its waste output and strategies for dealing with it is the uranium sector. Jahanshahi admits that this area has received very little attention relative to other mining disciplines, but that this would likely change as mining activity continues to rise sharply in line with global demand.
“There are some major opportunities and challenges in this area; we [the CSIRO] may direct some effort in this direction in collaboration with industry,” he says.
The CSIRO report tables 15 different waste categories after sulphide tailings and red mud, including mercury, iron oxide tailings, iron and steel making dusts, right down to tyres. Huge demand for rubber from China has seen many larger mining companies initiate recycling and other programmes to maintain their rubber supplies, including for the development of more sophisticated roads and even better truck drivers.
But Jahanshahi says that although there have been some ideas mooted to deal with the other materials that make up the total waste pie, apart from the use of byproducts such as slags and fly ash in construction industry, nothing is anywhere near commercial deployment yet.
“Some of these have been explored and strategies/technical solutions developed. Implementation has not occurred yet, possibly due to the economic case not being strong enough.”
It’s a point that’s often missed in discussions about waste management and waste reduction. Unless there’s a well-considered strategy directed towards commercial outcomes, waste management can very quickly become wasted money.