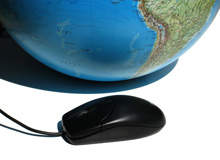
Automation and control are emerging as a major competitive factor for mining companies as they struggle to cope with spiralling labour costs and dwindling resources.
With much of the low-lying fruit already picked with respect to global resources, the current generation of miners is facing the prospect of having to drill deeper in more remote areas while also processing ore bodies of lower concentrations. This often means having to operate in more dangerous situations while creating more waste.
The new generation of automation and control (A&C) technologies is expected to play a key role in helping mining companies tackle these new challenges.
“Automation and control for leading companies are seen as a major differentiator,” says Bill Ellerton, mining expert with Siemens. A&C can give companies greater control over levels of granularity for what they’re managing, and, as Ellerton points out, ‘smart mines are more competitive from the start’.
Remote operation
While automation is not a new concept in manufacturing, its arrival in the mining sector has been relatively recent. Automation applications for mining tend to be far more complex due to detailed process chains. In the area of oil refining, for example, extremely complex applications are emerging to handle tasks like automated batch processing.
But almost every area of mining is set to use some form of automation within the next few years and reports are that industry demand is rising rapidly.

US Tariffs are shifting - will you react or anticipate?
Don’t let policy changes catch you off guard. Stay proactive with real-time data and expert analysis.
By GlobalDataSeveral new technologies define the ‘smart’ mine of today, including machines able to navigate underground and collect and transmit complex sample analysis data. Technologies for automated aerial mapping as well as explosives are important developments for the industry, alongside sophisticated new processing technologies to access mineral sands resources and uranium deposits.
All of these, according to Jock Cunningham, senior scientist and mining automation expert with Australia’s premier science and research organisation the CSIRO, develop through a somewhat evolutionary process.
“Once mining costs are reduced you can look at lower-grade resources – transforming uneconomic reserves into economic reserves,” he says.
Mining giant Rio Tinto has coined the acronym Mining In the New Dimension (MIND) to describe its efforts in this area.
“This means unambiguously going down the technology track towards better applications, including non-mining technology being introduced to mining,” says company spokesman Gervase Greene.
Rio Tinto Iron Ore will next year cut the ribbon on its state-of-the-art remote operations centre (ROC) in Perth in Western Australia, a facility that the company claims is an industry first and one which will galvanise the three-year lead in automation Rio says it has over its peers.
The ROC will employ around 320 people who will remotely manage mine operations in the Pilbara region 1,300km away. The company says it will also have remote-controlled “intelligent” trains, drills and trucks all operational by the end of 2008.
Commenting on the launch of the ROC in January, Rio Tinto chief executive Tom Albanese boasted to shareholders that “Rio Tinto is changing the face of mining”.
“We have at least a three-year start on the rest of the industry, which has focused on discrete technologies rather than modernising the whole mine-to-port operation,” Albanese says.
He says that Rio intends to become the world leader in fully integrated and automated operations. This would lead to more efficient operations and tackle the rising costs of supporting workers at remote sites while making the company a more appealing employer.
Importantly, the company sees itself as way-ahead of rival behemoth BHP Billiton, which has tried unsuccessfully to acquire Rio.
A trillion dollars Down Under
The CSIRO estimates that technical improvements to mining systems would assist in the conversion of around a trillion dollars worth of currently uneconomic resources in Australia to reserves by 2030. The implications then for the global industry are enormous.
The CSIRO’s Cunningham notes that important developments are occurring in the area of hard rock mining after ten years of research into new cutting and drilling tools.
“We [the CSIRO] are now reasonably well advanced in guiding machines based on geology instead of their geometry and location alone,” says Cunningham. “That in itself is a huge change.” New techniques are being trialled in underground coal mining with elements of tracking the seam and keeping machines inside the seam.
The mining sector is now moving into the third generation of automation, known as antonymous systems, as distinct from automated or automatic components of the mining process.
Solutions are now emerging which can allow companies to deploy intuitive, remote-controlled machines into remote and/or dangerous areas and do things like perform chemical analysis, as well as independently assess and react to geological conditions in real time.
Automated aircraft are also increasingly being considered to perform aerial mapping of mine operations. Underground loaders are being fitted with technology to allow mapping of tunnels in real time, while ore digging equipment is increasingly being fitted with sensors as a means of more quickly assessing mineral concentrations.
A key area of automation in mining is robotics. As Cunningham explains, much progress is being made in this area.
“The evolution of robots in mining is evolving from a position of automating existing mining machines – such as draglines and underground loaders – to the next stage of creating completely new machines which are designed to be a robot from the outset,” he says.
“For the first time, new mines are being designed as an automated mine.”
CSIRO is involved in a diverse range of automation projects: automated robot welding, sensing and navigation systems used in the automation of transport units in underground mines; laser beam automation to cut timber boards; automation systems for underground load haul dump units; and truck and shovel automation for open pit coal mines.
Progress is also being made in developing ‘robotic’ components for an automated explosives loading system, as well as systems for continuous calibration and checking for anomalies in machine operation. Such solutions will inevitably lead to more efficient mines and safer operating environments.
“One of the key drivers for automation is protecting people from hazardous tasks and environments,” says Cunningham.
“You need a whole level of protection to enable them to do that [be in those environments].”
He says that machines of the future will be able to autonomously adjust their speed and function depending on the operating environment. They will be able to communicate increasingly sophisticated information such as optimal operating speeds, potential breakdowns, the wear and fatigue of key components and appropriate maintenance schedules.
Similarly, high-wear machinery – such as that used in the oil and gas industry – will eventually be fitted with sensing machines that will have the ability to detect corrosion, wear and fatigue. The CSIRO is also developing new automated processes for underground mining. Transport is a major focus of current automation efforts.
Driving automation
The CSIRO is working with Rio Tinto’s aluminium business to develop automated vehicles capable of operating in conditions such as those with extreme heat, dust, bad weather and high magnetic fields. Safety is a prime factor.
For the past three years, CSIRO Light Metals Flagship scientists have been making important modifications to a hot metal carrier (HMC) shipped from Rio Tinto’s Bell Bay smelter in Tasmania. There they have been developing an automated system to transport and handle molten aluminum.
Siemens has been working with large ore truck companies to develop systems to manage vehicles switching between diesel and electric power via overhead tram lines, thereby reducing the amount of fuel that needs to be transported to and used on-site.
“This results in massive savings in diesel consumption,” says Ellerton.
Digging the future
The mining industry has benefited greatly from improvements in computing and communications technology over the last few years, with mobile communications playing an increasingly important role in automation systems.
The challenge now is how best to harness that technology.
“Most vendors claim they have great hardware, but increasingly it’s what you actually do with the hardware that matters,” Ellerton adds. A key focus for the mining industry moving forward is tighter integration between increasingly clever equipment and back-end systems such as enterprise resource planning (ERP).
One of the potential downsides of complex automation and control systems is that they could add significant new costs to mergers and acquisitions in cases where technologies are not compatible. The issue of standardisation is expected to play a bigger part in the development and deployment of automation and control systems.
“The challenge for a lot of mining organisations is that many of them don’t have standard operating environments at the automation and control level,” Ellerton says.
“Decisions are often made at the plant or individual mine site level.”
For new mining companies, this will not be so much of a problem. Much has been made of the competitive advantages gained by miners in China and India because of their access to cheap labour. However, Siemens’ Ellerton stresses that the real story lies in their early deployment of clever automated systems.
“The message is that they [mining companies] cannot compete against cheap labour from China and India, but this is a distorted message. The reality is that facilities in China and India are being built with the latest automation and control equipment.”