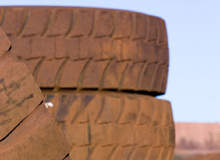
It is understandable that the resources sector was caught a little off-guard by the fact that economic growth in China, and to a lesser degree India, would have such an impact on industries worldwide because of a simple natural resource called rubber.
But a global shortage of rubber has held back production of mining companies around the world, struggling to pay the price for the wheels of the big trucks that keep the industry moving.
Team this with an insatiable demand for commodities in those nations that supply the rubber, or in this case can’t supply it, and you have an interesting predicament for mine operators everywhere.
According to Tim Riordan, a partner in Deloitte Australia’s energy and resources consulting business, the price of large tyres used for coal and iron ore trucks has more than tripled from $30,000 to around $100,000 in just a few years.
Such a hike has made operators look for new ways to reduce their tyre spend and seemingly opened up a new cottage industry as a result of this.
Behind the tyre shortage
With China’s rising profit comes a new class of people looking to put wheels on the road. The nation’s automotive industry consumes about 60% of China’s entire rubber diet alone.

US Tariffs are shifting - will you react or anticipate?
Don’t let policy changes catch you off guard. Stay proactive with real-time data and expert analysis.
By GlobalDataThe China Rubber Industry Association (CRIA) reports that China’s rubber consumption is expected to grow at 12% through to the end of 2008 to meet rising demand. This year alone China is expected to consume over 5 million tonnes of rubber, including 2.35 million tonnes of natural rubber and 2.7 million tonnes of synthetic rubber.
The International Rubber Study Group predicts that rubber supply will remain tight for another 14 years. It also points out that the gap between demand and supply would be 400,000t in 2010 and might touch 1.5Mt in 2020.
However, the growth rate of natural rubber production worldwide fell to 4% in the year to July 2005, from 8.7% for the previous corresponding period. Drought-induced supply shortfalls from world leaders Malaysia and Thailand were largely to blame. Climate issues also had a negative impact on India’s rubber industry.
Digging their way out of the skid pan
In 2007 mining giant Rio Tinto decided to take the wheel and come up with a way to overcome the rising cost of tyres. It opened an industry-first retread facility in Kewdale, West Australia, which today provides valuable data relevant to tyres, tyre usage and road design.
Rival BHP Billiton also boasts a number of R&D programmes it says have drastically lifted the performance of normal and large truck tyres. This trend, according to Deloitte’s Reardon, is likely to be seen across the world.
“Miners are putting a lot of effort into understanding the conditions and parameters for how to get the most out of their tyres,” says Riordan. “We’re seeing more miners carrying out R&D with their operations and collaborating with their suppliers.”
Like many of the world’s largest miners, Rio Tinto has huge investments in open-cut operations, in which large vehicles and trucks play a key role. The company says that its Kewdale facility is already leading to dramatic improvements in efficiency for tyre usage.
A major priority for the facility is understanding the behaviour of tyres and rubber under extremely harsh conditions, according to Kewdale Rio Tinto spokesman Gervase Greene.
“These are not just any tyres,” Greene says.
“These trucks carry 240t of iron ore in some of the harshest conditions imaginable. It is incredibly demanding.”
While truck tyres wouldn’t necessarily be immediately associated with cutting-edge science, Rio is finding that a few small tweaks – like learning how to connect retreads to tyre casings for different conditions – can require a reasonable degree of chemical engineering skill.
“There’s a fair amount of scientific innovation,” says Greene. Ultrasonic testing is also employed to identify where tyres are separating.
Behind the wheel
The Kewdale plant will also examine different operational methods of driving and will study in detail the impact of different road conditions, with a view to changing Rio’s approach to road building.
Greene says such blanket coverage should allow Rio Tinto to gain some of the most useful data on tyres and rubber performance to be found anywhere in the industry.
One of the company’s earlier findings has the potential to be extremely contentious well beyond the mining industry. “One thing we found was that in general, women drivers of our trucks were easier on the tyres,” Greene says.
Deloitte’s Riordan says that mining companies now have no choice but to adopt a more ‘life-of-asset-focus’.
“They need to ask themselves: how can we make the most efficient use of resources?” he says.
“They must understand conditions that impact tyre wear as well as equipment availability; this means being a lot more fact and analysis based.”
Bigger issues for big trucks
It is expected that the great tyre shortage will prompt mining companies to try to reduce the number of tyre suppliers to one key vendor, so as to collaborate closely and more effectively for improving performance.
“It [tyre supply] used to be managed site-by-site, now it’s more on a company basis and companies are arranging for long-term contracts with suppliers,” says Riordan.
Rio Tinto assures its stakeholders that the Kewdale plant features ‘an innovative combination of world-first manufacturing technologies and testing procedures’. At the beginning of the year it deployed its first 57in (inside diameter) retreads to the Pilbara region. Production is increasing steadily and is on track for 200 retreads of large truck tyres a year.
Rio’s head of global procurement, John McGagh, believes the project could prove an important component for the company’s long-term management of its worldwide mining operations.
“It is early days, but the initial trial results are promising,” he says.
“We are confident that the use of retreaded tyres will provide Rio Tinto with a more secure supply chain for tyres and will extend the life of a valuable resource.”
“The challenge of successfully retreading these tyres is at the forefront of technology, given the technical issues involved, the environment in which they must operate and the demanding performance and safety standards.”
The Kewdale plant and the retreading equipment were designed and procured by OTR Tyres Australia Ltd, a wholly owned subsidiary of OTR Tyres UK, Europe’s leading earthmover tyre specialists. OTR Australia is contracted by Rio Tinto to operate its factory with a team of local employees trained by OTR UK. The aim is to achieve the best result in terms of operating performance, safety and the environment.
Alternative investment
BHP Billiton is also looking into sourcing tyres from alternative sources, including emerging markets. “We have tyre-life improvement initiatives in place at our operations and they remain a key area of focus for our business excellence teams across the company,” a BHP spokesperson says. She adds that BHP’s tyre efficiency programmes have resulted in wheel loader tyre life being brought up to around 20,000 hours and large truck tyre life up to around 100,000 hours.
“Improvements to internal management processes have ensured that we have more accurate and consistent processes for forecasting supply and demand that enable our suppliers to grow capacity to meet our needs,” she says.
Riordan says that while it may make sense on some levels for mining companies to invest in their own rubber production, he feels that few companies would be able to achieve anything much without first incurring huge losses. “Cornering the market for tyres is not really the game,” he says.
Something that is certainly a big part of the game, however, is recycling, with countless mining companies having invested in recycling rubber and otter materials.
But while making mining companies look and feel very green, recycling will do very little to address the serious shortage of rubber. Making matters worse is the fact that in some countries, rubber producers themselves are running out of land. Leading suppliers such as Thailand, Malaysia and India have seen falling yields due to dryer climatic conditions.
However, relief may be on the horizon in the form of troubled third-world country Cambodia. As well as being famous for dangerous bushwalks and Hollywood A-List adoptions, Cambodia is also known for its fertile soil and abundant land for rubber plantations, plentiful water resources and low levels of rubber diseases.
On the economic front, the Cambodian Government provides incentives to promote rubber. Labour is comparatively cheap while the country itself is close to the world’s largest consumer of rubber, China, and only two hours from the economic hub of Singapore.
While acknowledging its potential for creating expensive delays, Deloitte’s Riordan says that the tyre shortage is one of many in an industry beset by shortages across the board. “It’s not like there is just one problem the industry is grappling with,” he says. However, the tyre shortage situation has highlighted the importance of better planning and cooperation, especially within large mining companies.