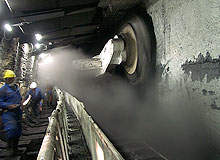
Despite serious health and safety regulations and technological advancement, coal mining remains one of the world’s most hazardous occupations. Explosions caused by the accidental ignition of methane are one of the most common causes of death in the industry, and strict safety protocols must be followed to minimise the chance of miners being killed instantly or becoming entombed under the earth.
2010 was a particularly painful year for the industry with two particularly high profile coal mining explosions, first at the Upper Big Branch Mine in West Virginia, US in April and then in November at the Pike River Mine in New Zealand. Each of these catastrophes claimed the lives of 29 miners and took place in countries with well-developed mine safety regulations and legislation.
So why, in the modern age, are mining explosions occurring with such alarming frequency? We talked to US mine safety expert and consultant Bruce Dial to find out the hard truths of working at the coalface. Dial has been immersed in the world of mining since he was 15 years old, working at his father’s mines. Since then, he has spent nearly a quarter of a century with the US Mine Safety and Health Administration (MSHA), as both mine inspector and safety instructor at the National Mine Academy. He now runs his own mine safety consultancy based in North Carolina.
Chris Lo: What are the most common causes of explosions in coal mines?
Bruce Dial: Explosions in coal mines usually start out with methane. Methane is liberated usually at the working section, either at the longwall or the entries that they use with continuous miners. Methane is a common gas that leaks out of the coal seam as you’re mining it. Once that methane has leaked out, you have to protect against any kind of spark that will set it off. Methane is very combustible – in the US, when it gets to 1.5%, they have to shut the equipment down. When it gets to 5%, if they can’t control it they have to evacuate the mine.
For example, the latest mining explosion in the US [Upper Big Branch Mine, April 2010] was caused by methane coming out of the coal of a longwall system, and they were mining a coal seam which also had some sandstone in it. As the teeth on the longwall were hitting on sandstone, it was causing sparks. Once it sets off the methane, then that explosion from the methane will stir up the coal dust in the air. Each particle of coal dust will actually explode – the coal dust then becomes the exploding part and if they don’t keep the coal dust cleaned up throughout the mine, then once it starts it automatically puts up more coal dust in front of it as it continues and it keeps exploding. The explosion at Big Branch in West Virginia went over two miles.
CL: What technologies are employed by mining companies to monitor gas levels and minimise the chances of an explosion occurring?
BD: Any type of equipment that is mining coal from a coal seam has to have methane monitors on it. These constantly monitor the air where they are mining the coal and once it gets to 1.5%, it automatically shuts the machine off and turns the electricity off. One of the problems is that a lot of companies will bypass those. They keep hitting pockets that set the machine off, and they don’t like that so they’ll just bypass those monitors. That’s one of the reasons we have these explosions.

US Tariffs are shifting - will you react or anticipate?
Don’t let policy changes catch you off guard. Stay proactive with real-time data and expert analysis.
By GlobalDataAnother problem is if they don’t keep the water sprays up, and that’s the latest thing they’ve discovered in the Big Branch explosion – the water sprays in this longwall were not working. The water sprays help put out any small flash from methane exploding, and they also wet down they coal to keep it out of the air. Then they don’t clean up the coal dust and it just lays on the ground ready to explode as soon as it gets an ignition source.
The monitors have to be calibrated every 30 days – there has to be a record kept of that. Besides the monitors on the machines, the foreman in charge of a work area has to have a handheld monitor, and he’s supposed to check the methane levels every 20 minutes. If he gets a sample above 1.5%, it means the methane monitor didn’t shut off the machine and it’s his responsibility to make sure the machine and the electricity is shut off. Many times, the foreman doesn’t do that, because he’s the one who actually had the methane monitors bypassed. So that’s a big problem there – the production takes precedence over the safety. We hate to admit that, but it’s an everyday occurrence.
CL: Do you think many companies have on overly lax approach to heath and safety in mines?
BD: Yes. Most common companies, small or large, are out for the production, and they’ll take every chance they get to make sure the machines don’t go down. But as more and more pressure comes on the guy on the frontline, the supervisor, the one at the bottom of the hill – everybody’s yelling at him so he’s doing everything he can to keep things going.
That’s where they start taking chances. You might get away with it a thousand times, but at some point something goes wrong.
Regulation has start to start at the top. If the person at the top is only looking for production and profit, this filters down and each person gets subjected to a little more pressure. Many companies have safety plans that look good on paper, but all that gets bypassed when it comes to the bottom line. That’s why every couple of years, we have a major mine explosion somewhere. Usually when you go back and look through the reports, it’s something that they knew about and was preventable, but they didn’t take care of.
CL: What techniques can be employed before mining starts to alleviate the potential dangers of gas build-up?
BD: When you drill a well to extract the gas, you’re usually getting natural gas. Methane is a byproduct of mining coal. What you have to do is take care of the methane while it’s in small amounts, which means you have to have good ventilation – pushing air throughout the mine and back out of the mine has is essential. We have some mines in the US that liberate more than a million cubic feet of methane per year, so you’ve got to handle it while it’s in small amounts.
CL: Is the Coalbed Methane Outreach Program, which is encouraging the industry in the US to capture methane to sell as a resource, having an impact?
BD: Not really; not yet. The biggest problem is that many gas companies say they own the rights to the methane or the gas, and the coal company says, “We own the right because we mine the coal and liberate the methane”. So they’re arguing in the courts and between themselves as to who owns the gas. So nobody’s willing to put a lot of money into capturing and selling the methane, which would be great. Nobody’s going to put the big bucks into capturing it until they can figure out who owns it and who’s going to make the profit.
CL: What is the best practice for rescue operations after an explosion?
BD: In 2006, MSHA passed some new regulations that said you have to have underground shelters that miners can go to and be protected until they’re rescued. That will supply trapped miners for about four days. But if the atmosphere of the mine isn’t adequate to send the rescuers in, then the miners are just stuck in there. You don’t want to send rescuers in there after dead bodies.
If we have no sign that they’re alive and we don’t know where they are exactly, sending rescuers in there is a hard decision. I think in 2006, there was another explosion in Utah, where they sent in rescuers and three of them were killed.
The new law that passed states that mining companies have to have a tracking system to keep track of where the miners are in the mine. They gave them three years to come up with the technology for that. In June 2009, that law came into effect, but there’s still not enough technology out there that every mine can do that. But there are some companies that are coming up with a wireless system that will keep track of the miners and know exactly where they are, even after an explosion because they’re not relying on wires to connect them.
So that technology is becoming available; it’s very costly but MSHA is saying companies have got to have it. If they don’t have it, or some plan to get it, MSHA will shut the mine down.
CL: Will the investigations of Pike River and Upper Big Branch shed new light on what happened and how explosions can be prevented in the future?
BD: Within 90 days, [MSHA] should have the final report out for the Big Branch explosion in the US. The one in New Zealand, I don’t think they’ll ever know because I don’t think they’ll ever get in there to investigate. It’s just going to be sealed, and that’s what they ended up doing at the Utah mine, they just sealed it and left the miners that were killed under there.