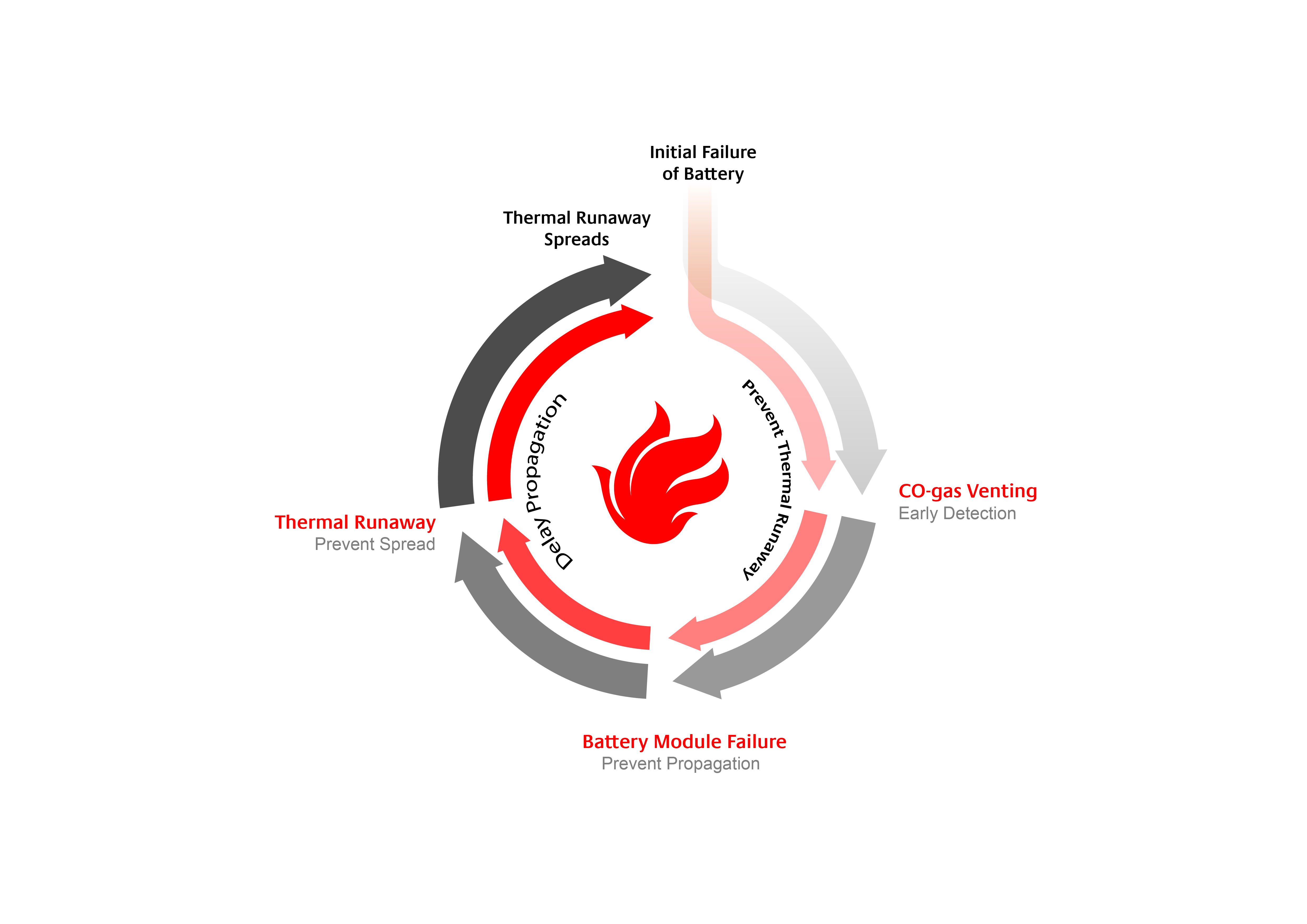
The global mining industry is evolving at pace, readily adopting new technologies, equipment and processes to advance every day site operations.
In line with global sustainability targets, reducing carbon emissions is key for many mine operators, which is seeing a mass transition to electrification – where traditionally diesel-powered vehicles and machinery are being switched out for environmentally-friendly, electric alternatives.
Marcello Sanchez, global sales manager – mining, Dafo Vehicle Fire Protection, explores how this global shift to electric vehicles for mines is impacting fire risks across the sector, unpicking how operators and OEMs can act to address these risks, maximising safety and minimising downtime.
Mining electrification
As governments around the world push ambitious sustainability agendas, many industries are looking to electric alternatives to the combustion-engine, diesel-powered vehicles, equipment and machinery that power every day operations – and mining is no exception.
From drilling rigs and loaders to dump trucks and excavators, many mine operators are making the switch to electrically-generated power – a move that’s predicted to be one of the biggest technology shifts seen in the mining industry to date.
Electrification presents different benefits for different types of mines. For underground mines in particular, electrification presents a critical opportunity to enhance safety while reducing costs, as vehicles and machinery will emit less fumes, reducing the need for expensive ventilation measures, while also improving the mine’s air quality for underground workers.
Shifting electrical risk
Although electrification offers many environmental, cost and health benefits for mines around the world, it does also bring about new considerations to ensure maximum fire safety.
Currently, electrical faults are one of the primary causes of fire for mines, a statistic that’s likely to be intensified against the backdrop of the electrification of site fleets and machinery.
The principal risk for many mining battery electric vehicles (BEVs) is thermal runaway. This is a process, which occurs as a result of an internal short-circuit in a lithium-ion (li-ion) battery’s cells. That short-circuit can be caused by a range of factors, such as mechanical failure, physical damage, overheating, overvoltage or overcharging.
In thermal runaway, a battery will begin to generate excess heat, which prompts exponential rises in temperature. If not controlled quickly and effectively, this can lead to the venting of toxic gases (such as carbon monoxide, CO) and fire in the mine, which can cause extensive damage and prolonged periods of downtime.
When in thermal runaway, a battery is also able to produce its own oxygen source, propagating flames from within. This makes suppression using conventional measures particularly challenging, and as a result, addressing it effectively often requires a unique solution.
Handling damaged electrical vehicles and equipment
Due to the harsh environment of live mine sites, many vehicles and machinery need to withstand the most extreme and challenging working conditions.
There is, inevitably, a risk – particularly for smaller mining vehicles and equipment – of physical damage, for example as it collides with other equipment or hard core. If BEVs are damaged in any way, thermal runaway becomes a much more pertinent risk.
If damaged on site, electric vehicles and machinery should be isolated and quarantined for a period of time to assess and contain any damage. To minimise this necessary period of downtime, damaged electric vehicles and machinery at mines should be monitored by a unique detection system, which will identify any low-level toxic gas emissions that may occur as a precursor to thermal runaway.
This system can then alert for the appropriate suppression action, getting ahead of the risk and preventing thermal runaway from developing and having the ability to cause further damage and downtime to the vehicle and surrounding assets.
Minimising risk to enable mining’s safe, sustainable future
Every new process or piece of equipment should begin with a full risk assessment. This will help to identify the most suitable detection and suppression solutions to minimise risk and maximise safety.