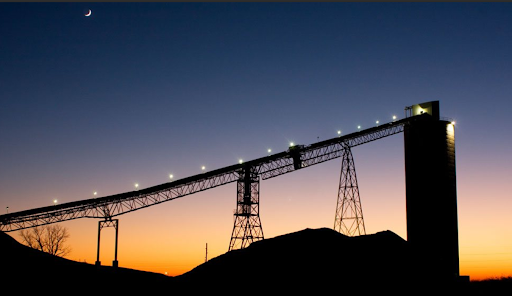
High-tension conveyor points no longer a maintenance headache for underground coal operation
What does it cost when conveyor rollers fail every two weeks? For Knight Hawk Coal, each failure meant at least 30 minutes of lost production time, with crews asked to navigate difficult-to-reach locations, manage lockout procedures, and complete complicated restart sequences.
Knight Hawk’s belt coordinator refused to accept this as normal so he tried several fixes, but nothing lasted. Then he tested a different approach to the problem. Now, the same rollers have been running for over nine months without wear which has eliminated maintenance headaches and kept coal moving reliably through their underground operation.
High-tension points creating constant downtime
Knight Hawk operates a room-and-pillar coal mine where more than 20 conveyor systems move coal through their underground operation. The belt coordinator knew that high-tension areas had the biggest problems, so he invited John Scott, Mining Account Manager at PROK to visit and help him troubleshoot.
“These things fail every couple weeks,” he told John. Together they examined the critical areas where the return belt comes down into the drive and exits the take-up unit. Here, the intense pressure on standard rollers created consistent failures, pulling maintenance crews away from other critical work.
Finding the root cause
The belt coordinator walked John through each problem area, showing how their conveyor configuration created unique challenges. At several points, the system needed to pass over or under air passages, requiring steep vertical transitions over short distances.
As Ray Anderson, Engineering Manager at PROK, explains: “Where return air passes over the intake air, the belt has to be elevated over about 30 feet. When you do that over a short distance, you increase belt tension putting more load on the idlers, particularly in the return path. This increases the risk of wear and misalignment.”
This vertical deviation created forces that standard components weren’t designed to handle. While the mine followed standard industry specifications, their particular setup demanded something more robust. Standard industry components were being asked to handle forces they weren’t designed for.
Engineering the solution
Next, John reviewed exactly what Knight Hawk was dealing with: “I went through a lot of the scenarios: overcast, undercast, different things like high pressure coming out of the drive, going into take-up, coming out of the take-up.”
Instead of offering a catalog solution, he proposed a practical trial, suggesting: “What if I build you a trial roller and you test it?”
The design process focused on four key issues causing standard rollers to fail:
- Shaft deflection under load
“You’re dealing with forces similar to a steel beam under load,” explains Ray. “When you increase shaft size through the middle, you reduce deflection. More deflection means increased bearing misalignment during operation, which leads to increased bearing failure. - Manufacturing precision
“We use tighter tolerances on our roller tube roundness, so the roller runs true,” Ray notes. “This reduces vibration and noise, as high vibration and noise can increase the potential of the rollers to fail.” - Environmental protection
“In underground coal mining, you’re dealing with extremely dusty, wet conditions. The sealing system needs to keep these contaminants away from critical components.” - Component quality
Premium bearings and precision-machined parts throughout the design eliminate common failure points.
Night Hawk’s belt coordinator then chose their most challenging location to test the new design.
From trial to mine-wide implementation
The Knight Hawk team installed two trial rollers in their most demanding location.
Within a month, the difference was measurable: “These things are so quiet and run so smooth. We haven’t lost a bearing yet,” he told John.
“We can walk along a PROK belt and have a conversation. With the old system, we had to shout,” reported the maintenance team.
This quiet operation indicated the rollers were running smoothly, with minimal vibration and no stress on components.
After two months of successful operation, Knight Hawk ordered enough rollers for all their high-tension points. Nine months later, the original trial rollers were still running without the bearing failures that previously occurred every two weeks.
Making the case for quality
When Knight Hawk needed to replace an entire belt line, their belt coordinator had to justify investing in premium components despite the higher upfront cost.
After nine months of proven performance from the trial rollers, he was convinced: “We’re getting it. We’re buying PROK,” he told John. “Their machined shafts, heavy-duty design for reduced deflection, and premium bearings and seals – when you put all that together, it’s just unbeatable.”
The business case focused on total cost of ownership:
- Labor hours spent on constant roller replacement
- Production losses during conveyor downtime
- Impact on workforce productivity
“That’s why they were able to make a business case to their management,” John explains. “It wasn’t just labor cost — it was downtime and production loss.”
Knight Hawk management approved the complete conveyor system upgrade, including PROK structure, rollers, and idlers. For their maintenance team, it meant they could focus on preventive maintenance instead of constant replacements.
Long-term results
The success of the upgrade had immediate operational benefits. Production became more reliable without the constant interruptions, and operators appreciated the quieter work environment. The conveyors ran quietly and reliably, exactly as engineered.
The original trial rollers were still performing well, without replacement, so the belt coordinator’s decision to focus on total operational costs had been justified.
“Now he’s looking at the 72-inch belt width for future purchases too,” John notes.
We’re looking forward to continuing to work with Knight Hawk to improve their uptime throughout the mine.
Results at a glance:
- Component life: From 2 weeks to 9+ months
- Maintenance: From emergency repairs to preventive work
- Production: Eliminated bi-weekly roller failures
- Noise reduction: Quieter operation indicates better performance
- Widespread implementation: From single trial to mine-wide standard