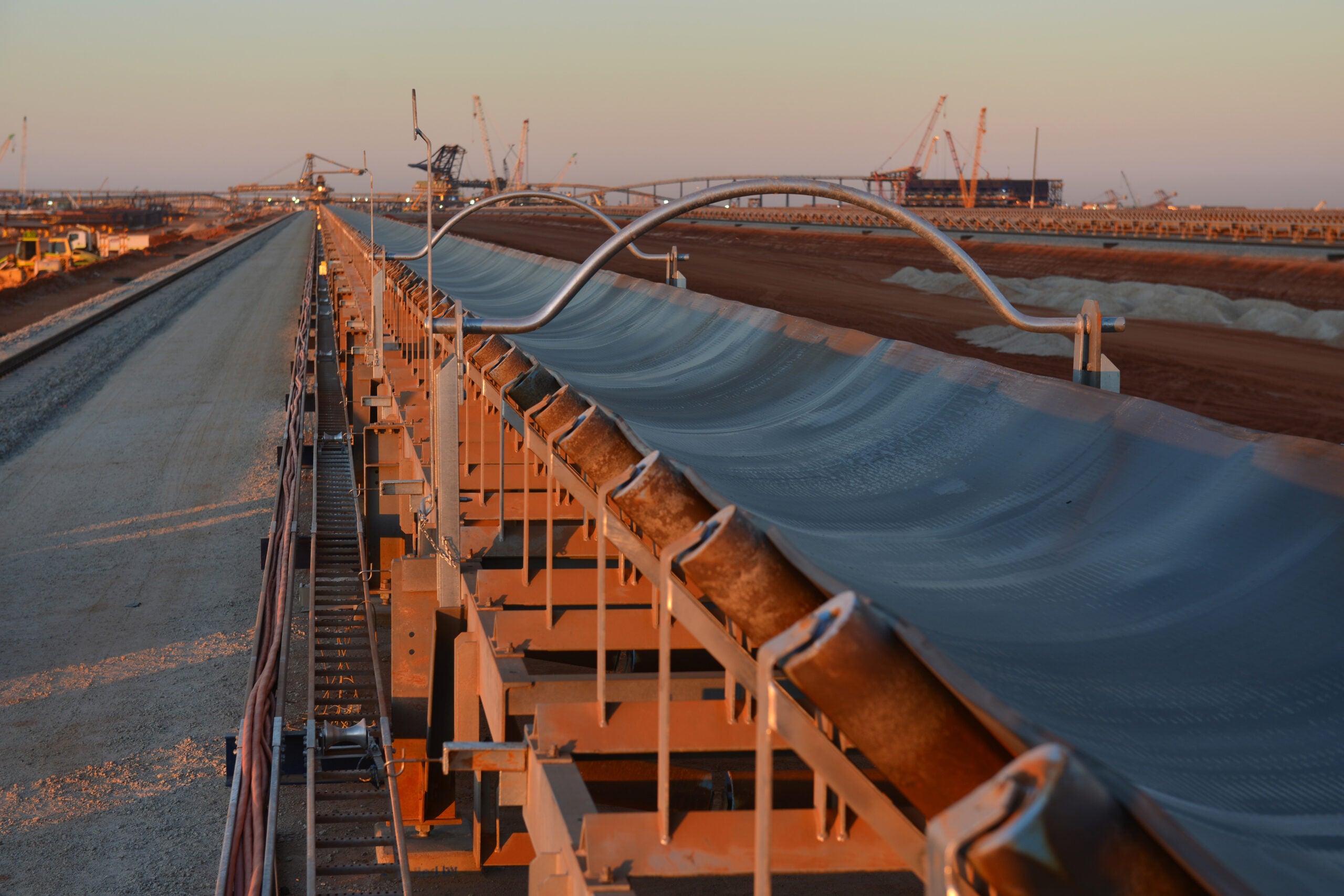
You know the feeling. Another roller seized up mid-shift. Another bearing that was supposed to last years, gone after months. Another emergency call that throws your whole maintenance schedule off track.
We’ve spent years watching maintenance teams battle the same roller failures over and over. The frustrating part? Most of these failures are completely preventable.
Here’s five things that we’ve learned to keep your conveyor rollers running longer and avoid those midnight callouts.
- Use a Quality Sealing System
Your sealing system is there to keep contaminants out. When water or dust gets past that seal, it mixes with your grease and starts breaking down your bearings from the inside.
But here’s the tricky part: if you make your seal too tight, you can introduce excessive drag and heat, potentially leading to material creep that will compromise the rollers’ performance.
“Getting it right is a balancing act,” says Brayden Kubala, Principal Engineer – Idlers at PROK. “Your seal system is the first line of defence against contamination, like rain, humidity, condensation, or water from washdown hoses. A good sealing system balances enough protection with low drag. You could create the world’s best seal, but if it introduces too much drag, it’s not viable.”
Watch out for seals. Their performance can change drastically after six months of operation. For example, radial oil seals that run directly onto your shaft often introduce shaft wear, and this creates grooves that allow contaminants to bypass the seal. This wear develops gradually and won’t show up initially in testing, but eventually they’ll wear a groove into the shaft. Instead, look for designs with a separate stainless steel running surface. It costs a bit more upfront but saves you from replacing shafts later.
And remember, your site conditions matter. Thermal expansion, production tolerances, even the humidity levels all affect how well your seals work. If your supplier hasn’t factored these in, you’re setting yourself up for problems.
- Choose the Right Idler Design
Sometimes contamination isn’t your problem, it’s the design itself. I’ve seen countless cases where the shaft is simply too thin for the job. When it flexes under load, it creates angular movement at the bearing. That’s a recipe for early failure.
“Many failures stem from bearings that are too small for the actual load, even if they technically fit,” says Brayden.
Here’s what makes it worse: on most sites, nobody has the exact load figures handy. You’re relying on specs from years ago or best guesses. A good supplier should be able to recommend the right setup based on similar conveyors they’ve worked with.
One sneaky failure mode to watch for is fretting corrosion. Tiny movements wear away protective layers, causing metal fatigue you won’t spot until it’s too late. A roller that should last seven years fails in two, and by then, the evidence is long gone.
Before you reorder the same spec you’ve always used, ask yourself: is this really the right bearing for the job? Sometimes spending 10% more on a bigger bearing saves you three changeouts down the line.
- Use Non-Rotating End Shields
Picture this: a rock gets wedged between your roller and the frame. Without non-rotating end shields, something’s got to give. Usually your frame buckles or the roller drops out completely. Now you’ve got structural damage, safety hazards, and a mess to clean up.
Non-rotating end shields prevent this whole scenario. They also handle high-pressure washdowns better and reduce the risk of someone getting their hand or clothing caught.
“If you don’t have a non-rotating end shield and something wedges in, the roller can drop out of the frame – that’s a serious safety hazard,” Kubala says.
If you’re running impact zones or anywhere that gets regular washdowns, these should be non-negotiable.
- The Decision to Shield or to Seal Matters
This one even trips up experienced teams. You’d think sealed bearings with rubber lips would always beat shielded bearings with metal covers for protection, right?
Not exactly.
Sealed bearings work great for brief water exposure during a 20-minute washdown, for example. But leave them sitting in water or constantly exposed to moisture, and they become a liability. The pressure difference slowly draws water inside, where it gets trapped. Your grease breaks down, and your bearing life plummets.
“Sealed bearing are superior for intermittent/short exposure, but they’re not suitable for exposure to humidity/moisture over extended periods of time where they will start to draw moisture into the seal” explains Brayden.
Plus, sealed bearings create more drag, generate more heat, and cost roughly double. When you multiply that across thousands of rollers, you’re burning money and energy for no good reason.
Shielded bearings paired with a proper external sealing system usually give you better protection at lower cost. If your supplier can’t explain why they’ve chosen one over the other, that’s a red flag.
- Understand Bearing Clearance and Fit
This silent failure mode catches everyone out eventually. You order the right bearing size, install it properly, and it still fails early. Why?
Internal clearance (the tiny gap between balls and raceways) changes once you press that bearing into place. Too tight a fit compresses the races and eliminates that crucial clearance. Too loose, and you get unwanted movement under load.
“You need to consider how the housing compresses the outer race and how the shaft expands the inner race; that affects the actual clearance inside the bearing once it’s installed,” says Brayden.
The worst part? Everything looks fine during installation. The failure shows up months later with no obvious cause. By then, you’ve probably installed dozens more the same way.
Get the Right Specs
Next time you’re ordering rollers, resist the urge to just replace what’s always been there. Those specs might have been wrong from day one, chosen by someone juggling a dozen other decisions during construction.
Ask your supplier the hard questions:
- Why this seal design?
- How does it handle our specific conditions?
- What’s the actual load capacity versus what we’re running?
- How are you accounting for fit and clearance?
If they can’t answer clearly, find someone who can.
Because at the end of the day, you’re the one who gets the midnight call when a roller fails. You’re the one explaining why the shutdown’s running over. And you’re the one who can stop it from happening again.
“Ask the tough questions about what’s already installed,” says Brayden. “There’s no point in doing the same thing and expecting a different result.”