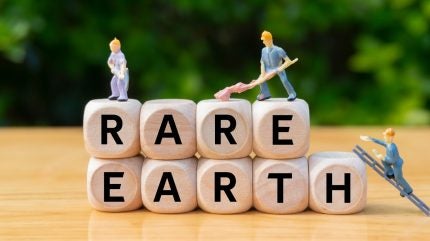
In April, China imposed a new round of export controls on seven rare earth elements (REEs) that are essential for modern technology ─ dysprosium, gadolinium, lutetium, samarium, scandium, terbium and yttrium.
These latest restrictions, which came in response to US President Donald Trump’s tariffs of up to 145% on Chinese goods, are not outright bans. However, they mean companies will need to apply for a licence to export rare earths, which could lead to a temporary pause in trade.
Discover B2B Marketing That Performs
Combine business intelligence and editorial excellence to reach engaged professionals across 36 leading media platforms.
Given that China is responsible for around 90% of rare earth processing, the latest limitations on REEs exports have had the anticipated disruptive effects. Numerous sectors are expected to face challenges, including automotive, energy, healthcare, and aerospace, according to GlobalData, Mining Technology’s parent company.
The US remains “highly exposed” in the event of prolonged trade escalation, but the controls will also have an international reach.
“Given the sprawling nature of supply chains, these restrictions will have a global impact, affecting trade partners and customers worldwide, not just those in the US,” says Isabel Al-Dhahir principal analyst at GlobalData.
US wants more domestic supplies of REEs
In 2024, the US imported an estimated $170m worth of rare-earth compounds and metals – mostly from China – producing 45,000 tonnes (t) of rare earth oxides worth $260m domestically, according to data from the the US Geological Survey (USGS).

US Tariffs are shifting - will you react or anticipate?
Don’t let policy changes catch you off guard. Stay proactive with real-time data and expert analysis.
By GlobalDataIn recent years the US has taken several steps to secure a domestic supply of REEs, including through federal funding, public-private partnerships and efforts to reopen or expand domestic mines.
These efforts stem back to 2022, when then-President Joe Biden invoked the Defense Production Act to accelerate the development of the US’ energy transition industries and also evoked the Inflation Reduction Act, says GlobalData strategic intelligence analyst Martina Raveni.
Since taking office, US President Donald Trump has issued several executive orders aimed at boosting domestic mining and production of the minerals.
In recent written testimony, US Energy Secretary Christopher Wright stated it is essential for the US to “focus on building domestic capabilities to extract, process, manufacture, and recover end-of-life critical materials for our [US] industrial needs, energy goals, and national security”.
The US Department of Energy (DOE) is already directly supporting these goals laid out in the executive orders “by identifying and expediting pending projects to support domestic mineral production… exploring the effectiveness of offtake agreements and pricing support and developing new programmes to bolster domestic mining and production”.
The DOE is also coordinating with other agencies including the US Department of Defense (DOD), which aims to have a mine-to-magnet supply chain to support all US defence sector requirements by 2027. Additionally, the US Department of Commerce has been directed to investigate whether imports of critical minerals, REEs, processed critical minerals and their derivative products threaten US national security.
Despite “leaps of progress” in the past few years, the US “is still playing catch-up when it comes to rare earth supply”, says Nicole Richards, CEO of Allonnia, a biotech company that is aiming to extract REEs from waste streams. She believes that extracting REEs from both ore and waste should be considered when building strategies to diversify sources outside of China.
Rare earth mining, processing and recycling in the US
MP Materials is currently the only major rare earth producer in the US, operating the Mountain Pass mine in California. The company is investing in expansion, and in April was awarded $58.5m to support construction of a rare earth magnet manufacturing facility in Fort Worth, Texas.
US DOD funding is supporting Lynas USA, which is focused on developing a domestic rare earth supply chain. The US subsidiary of Australian-listed Lynas aims to build a US separation facility for light REEs, with a further $258m allocated for a heavy rare earths processing facility in Texas.
However, the landscape for new rare earth projects is “notably sparse”, according to GlobalData, with just three projects in active development and facing considerable hurdles.
The projects are Rare Element Resources’ Bear Lodge in north-eastern Wyoming, NioCorp’s Elk Creek project in south-east Nebraska and the Bokan Mountain project in Alaska.
“The earliest projections indicate they will not come online until the latter part of this decade, with this timeline raising concerns, as the nation risks falling behind in a rapidly evolving market,” GlobalData explains.
The importance of recycling rare earths
Recycling is seen as vital to help mitigate shortages of REEs and is expected to become an important element of near-term supply chain diversification – despite recycling rates of just 5% today.
“Employing recycled materials reduces the dependency on issues such as mining output, ore grade, regional export quotas, geographic and political monopolies, and other unpredictable factors that make the market volatile,” says Raveni.
Recycling also helps reduce the environmental impact of mining – and is important to consider regarding emissions disclosure rules.
Furthermore, as new mines can take up to ten years to become operational, investing in recycling facilities is expected to play an “important role in offsetting near-term supply shortages until the new mines come online”.
Investment in new technologies
Richards points to “a wave of innovation and investment” in critical mineral recovery and recycling, including as part of US national defence initiatives.
In January, the DOD awarded $5.1m to REEcycle to enhance recovery of the materials from electronic waste. Investments in REE recycling facilities are growing in the US, with other leading companies including Canada-headquartered Cyclic Materials and MP Materials, according to GlobalData.
“E-waste is a more immediate way to blunt the spear point of economic and national security concerns,” Nathan Ratledge, co-founder and CEO of Alta Resource Technologies, tells Mining Technology. Alta has raised almost $10m to help develop and commercialise its platform for biochemical separation of REEs.
Developing new technology that can both improve rare earth recovery and minimise environmental impact is seen as key – both for recycling and processing of mined ore or tailings.
Tech giant Microsoft recently completed a US pilot project that recovered around 90% of the REEs, gold and copper, from around 220t of shredded end-of-life hard disk drives, mounting caddies and other materials.
The initiative, run in partnership with Western Digital, Critical Materials Recycling and PedalPoint Recycling, used acid-free dissolution recycling (ADR) technology. ADR was invented and initially developed at the DOE-led Critical Materials Innovation Hub, moving from lab to demonstration scale in eight years.
Biotechnology solutions are among those that can help increase yield and reduce the carbon footprint and environmental impact of REE processing, agree Ratledge and Richards.
Allonia claims its technology can increase metal production by 20%, with a potential 10% reduction in carbon footprint, while Ratledge says Alta’s platform is “far cleaner”, with less water consumption, air pollution and climate impact.
Richards also believes that bio-based solutions could be implemented faster than conventional routes.
Looking outside of the US for REE supply
With challenges building domestic capability, the US is also looking externally to bolster its rare earth supply chains.
Australia and Canada are good alternatives for sourcing REEs; however, these countries have limited production capabilities and infrastructure, says Raveni.
“The high costs, market volatility and environmental concerns associated with REE extraction and processing further complicate the objective of securing stable supplies outside of China,” she adds.
Lynas Rare Earths is seen as a significant player outside of China, operating Mount Weld mine in Western Australia and investing in downstream processing capabilities.
Vietnam also should not be ignored as a rising player in rare earths, Richards says. With an estimated 22 million tonnes of rare earth reserves – or 20% of the global total as of 2024 – Vietnam ranked second only to China, according to GlobalData. The estimates have since been revised downwards (see chart).
“As foreign investors grow interested in this supply, Vietnam’s separation and processing capacity will follow,” suggests Richards.
The path to overcoming China’s dominance
Regardless of the source ─ US mines, imports from friendly nations, or recycling ─ substantial investment and time is needed to diversify US rare earth supply.
China’s dominance in the global rare earth market is largely due to its lower production costs, often achieved by disregarding environmental regulations. The country has also mastered the complex process of separating and refining rare earths, giving it significant pricing power and supply control.
“Where rare earths are concerned, there are many processing steps requiring significant capital and expertise to take a resource from the ground to a finished product,” says Richards. “Shifting from China to domestic resources will take a sustained level of public and private partnerships to achieve success.”