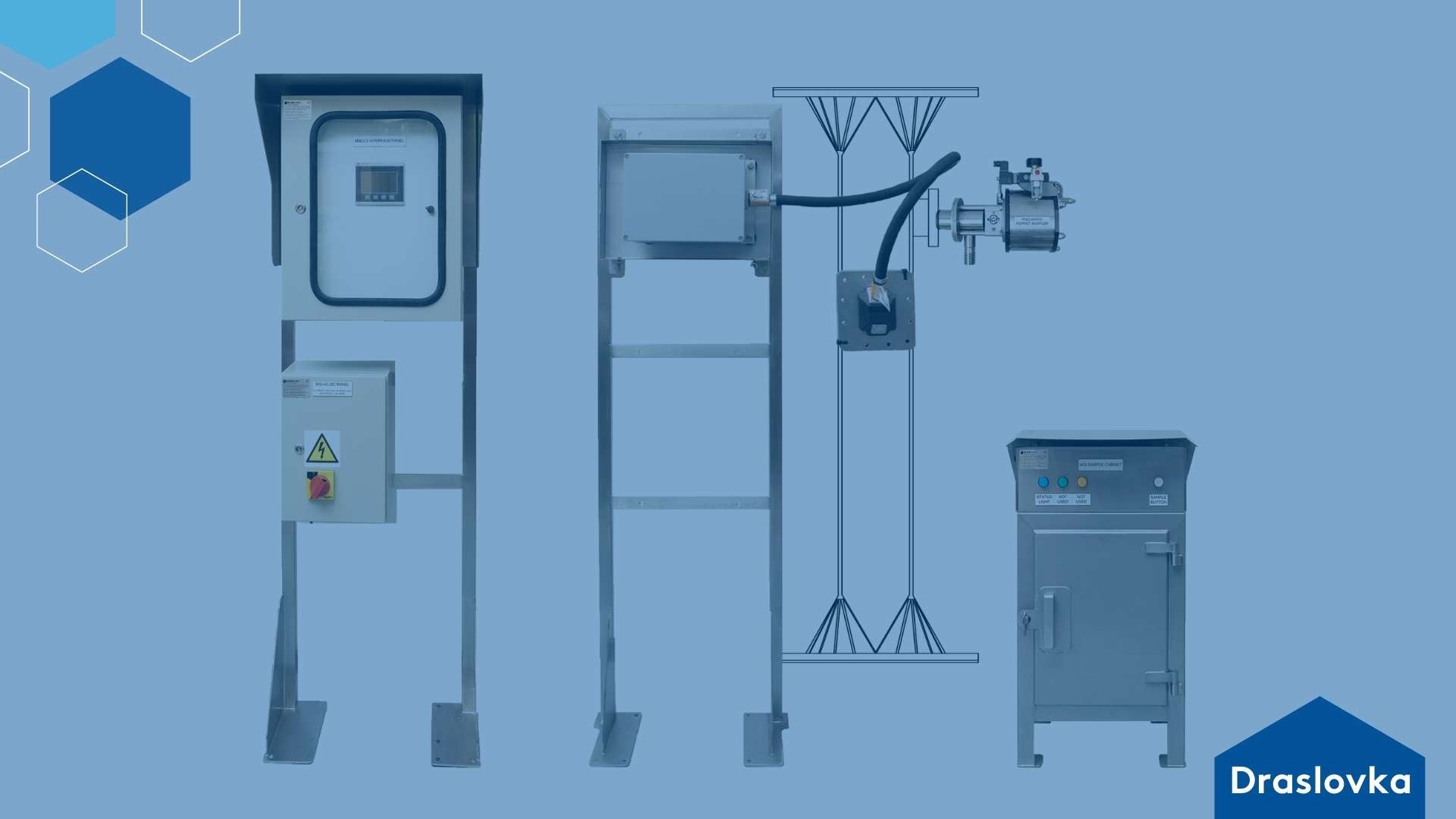
By providing reliable, real-time insights, our analyzer enables faster, more informed decision-making to optimize product grade and recovery.
It’s an in-line instrument that measures the composition of slurry streams in real-time. The analyzer continuously scans the contents of the process stream directly without removing it from the pipe, resulting in a measurement that is truly representative of the real process.
Blue Cube’s diffuse reflectance spectroscopy (DRS) analytical technique uses a broad band of light from ultraviolet, through visible, and into near-infrared, together with state-of-the-art machine learning techniques, to determine grade and other process parameters based on the spectra reflected from particles in the slurry.
DRS covers a much broader range of electromagnetic frequencies than XRF-based analyzers, capturing more information at much shorter integration periods. This allows Blue Cube to measure the grade of both light and heavy elements, minerals, as well as other process parameters such as particle size. Our optical technology can be applied to any quantifiable property that affects the spectra in this broad range of light.
The powerful combination of in-line measurement and DRS allows Blue Cube to update all measured parameters simultaneously every 15 seconds.
Benefits:
- In-line measurement: With a small footprint, the Blue Cube Slurry Analyzer is easy to integrate, requiring no sample streams, sample pumps, or multiplexers. It can measure pumped, upward-flowing process lines of any diameter greater than 25mm.
- Unmatched range: Measures both light and heavy elements, minerals, particle size and % solids, all in one instrument.
- Low maintenance: Mechanically simple – only two moving parts, no high wear components
- Fast response: 15 second updates to all parameters, simultaneously. These rapid measurement updates enable effective process stabilisation through automatic process control.
- Inherently safe: No radioactive sources or high intensity lasers
- Automatic manipulation of air addition, pulp levels and reagents are suggested for the control of grade and recovery in typical flotation circuits.
- Blue Cube can be used together with a mass flow indication to optimise recovery.
- Product grade can be optimised, and the impurity content minimised to eliminate penalties.
- Proven technology: 100+ analyzers deployed worldwide
How It Works
- Light is directed through a sapphire window onto the slurry stream as it passes through the pipe and the light reflected by the stream particles captured. The reflected light is digitized and used together with a calibration model to extract spectral features of interest and provide 15-second updates to the measured parameters.
- The BlueCube Slurry Analyzer monitors the process and automatically extracts one calibration sample per day when process conditions are appropriate using the integrated pneumatic sampler.
- The spectra captured while the calibration sample is drawn are recorded and uploaded to an off-site data centre via the cloud. The laboratory assays of the calibration samples (emailed to Draslovka weekly), are used together with the uploaded spectra to monitor performance and fine-tune the calibration model.
- The refined calibration model is automatically downloaded to the instrument to ensure accuracy is maintained through drifts in process conditions and lithology. This process is repeated on an ongoing basis, with new samples used to improve or adjust the model, and to report on the accuracy of the analyser.