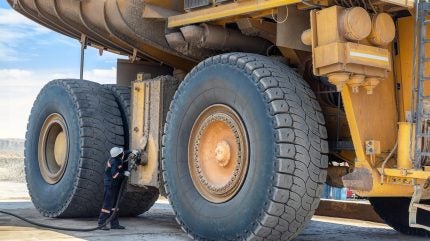
Mining is reliant on large, highly specialised, mobile mining equipment, which is predominantly diesel powered due to diesel’s high energy density, fast re-fuelling times and flexibility. Haul trucks make up nearly half the average diesel consumption of a typical mining operation, driven by their high utilisation rates and heavy loads.

Even by 2040, mining operators expect diesel to power more than two thirds of their haul truck operations.
Discover B2B Marketing That Performs
Combine business intelligence and editorial excellence to reach engaged professionals across 36 leading media platforms.

Our research shows that reducing GHG emissions is an important part of the strategy for the majority of mine operators but there are challenges, and it requires an agile, practical approach.

Mining is an energy-intensive industry with a commodity pricing model for most of its output. Mining operators therefore need to optimise productivity and efficiency to add value, all while maintaining a focus on safety and the local environment.
Measures to improve efficiency have the added benefit of reducing emissions per unit of production and can play a foundational role in the emission reduction roadmaps of mining operators. There are several options, including use of additized diesel fuels, like Diesel Efficient™ fuel from ExxonMobil. An important area of focus is to maximise the benefits of data integration and fleet management systems. Early adopters are also layering in additional benefits from autonomous operation.
A shift to lower carbon intensity electricity sources, like solar, and electrification of mining operations are part of the plan of many operators, but currently only around 2% of mining haul trucks are electrified.
Biofuel benefits
Measures to optimise productivity, efficiency and tailpipe/stack emissions are a solid start but mining operators now have the option to leverage the benefits of biofuels to reduce their lifecycle GHG emissions[1] using existing internal combustion engine-based platforms and on-site generators.
There are two main biofuel options:
- Biodiesel, also known as Fatty Acid Methyl Ester (FAME).
- Renewable diesel, also known as hydrotreated vegetable oil (HVO) or hydrogenation derived renewable diesel (HDRD).
Many fleet operators foresee a role for these product solutions in their operations, with an expectation that over one third of all diesel haul trucks by 2040 will be bio- or renewable diesel-powered. (Figure 2)
Biodiesel is a cost-effective choice to help reduce the carbon intensity of fuel for compression-ignition engines1. It’s primarily supplied in blends with conventional diesel, typically up to B20 (up to 20% by volume FAME content).[2]
Renewable diesel is produced via a completely different process to the one involved in biodiesel production. As a result, it can be used as a drop-in alternative, even in neat form (HVO100/R100), in many modern mining haul trucks.2
The power of collaboration
ExxonMobil understands that the mining sector is striving to reduce emissions while maintaining productivity. We engage with players across the transportation ecosystem, from OEMs to mining operators, so we’re well placed to help.
[1] Models and methodologies recognized by policymakers vary and cause the lifecycle GHG emissions estimates to also vary by jurisdiction. See for example Renewable Energy Directive 2018/2001/EU Annex V. To illustrate the potential difference based on feedstock, the default values in Annex V of the Renewable Energy Directive estimate a 47% reduction in the lifecycle GHG emissions of rapeseed biodiesel and an 84% reduction in lifecycle GHG emissions of waste cooking oil biodiesel compared to conventional transportation fuel.
[2] We recommend you verify fuel compatibility with your vehicle owner’s manual or by contacting your vehicle manufacturer