In this exclusive interview, Tomer Srulevich, Chief Business Officer at Razor Labs, shares how the company’s award-winning DataMind AI™ platform is transforming mining operations. Srulevich discusses the journey from overcoming data integration challenges to delivering predictive, AI-driven maintenance that reduces downtime, boosts safety, and maximizes asset life.
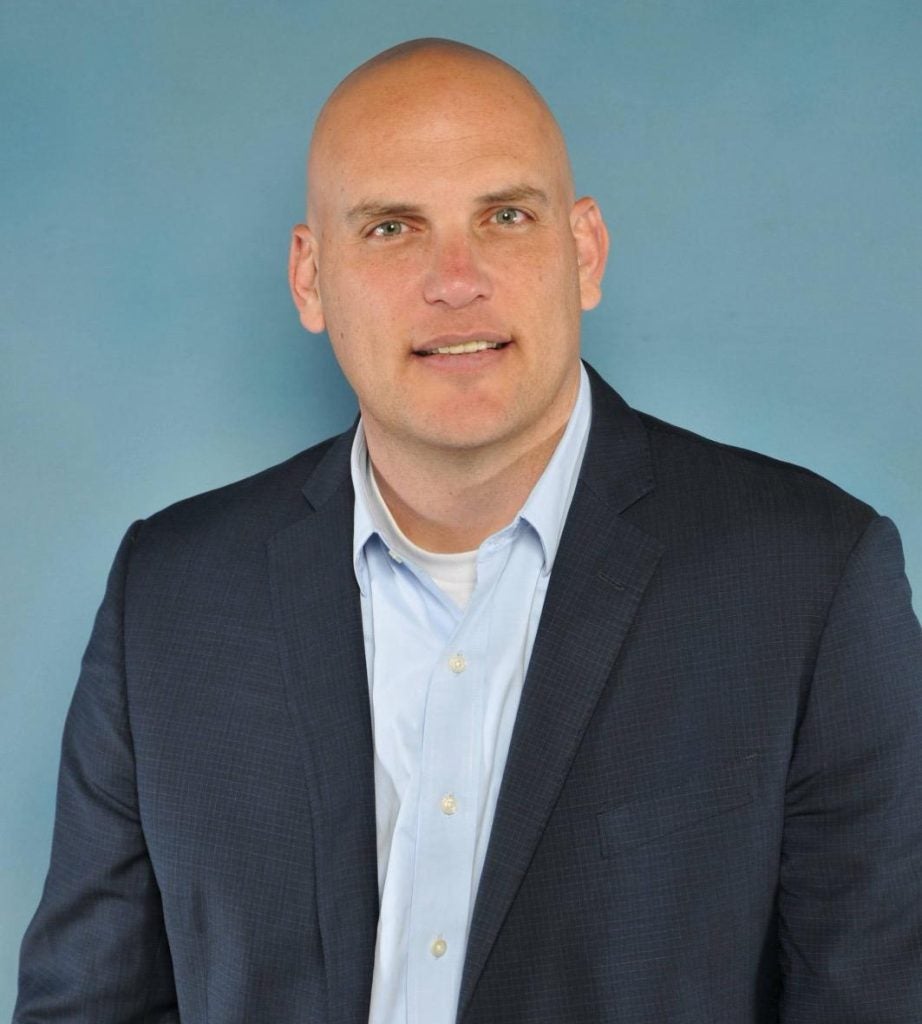
Mining Technology: Congratulations on winning the Innovation award in the Equipment Diagnostics category! What does this recognition mean for Razor Labs and your team?
Tomer Srulevich: It’s a proud moment for the entire team. This award recognizes the years we’ve spent developing, deploying, and refining AI solutions tailored for mining’s unique challenges. It’s not just a technology win — it’s a validation of the impact we’re delivering to the field. Our work eliminates blind spots, prevents breakdowns, and makes sites safer and more efficient. This acknowledgment also energizes us to keep pushing the boundaries of what AI can do in heavy industry.
Mining Technology: Can you elaborate on the vision behind DataMind AI™ and how it aligns with Razor Labs’ overall mission in the mining industry?
Tomer Srulevich: From the start, our vision was to replace reactive maintenance with predictive, AI-driven action — not just alerts, but full root cause insights and prescriptive steps. DataMind AI™ is built to be a single out-of-the-box solution that integrates with existing infrastructure or stands on its own. We aim to reduce unplanned downtime, maximize asset life, and give teams total visibility across critical equipment — whether that’s pumps, mills, crushers, or conveyors. It’s our way of embedding smart, real-time decision-making directly into site operations.
Mining Technology: DataMind AI™ clearly demonstrated significant cost savings and operational efficiency. How do you measure the success of your AI solutions in real-world applications?
Tomer Srulevich: We measure success where it matters most: downtime avoided, dollars saved, and reliability increased. For example, at an iron ore site, we identified rapid pump bearing deterioration that traditional inspection missed — saving the customer secondary damage and costly unplanned shutdowns. In another case, we uncovered electrical fluting in a conveyor motor bearing at a coal mine, enabling early intervention that extended the equipment’s lifespan. These outcomes saved hundreds of thousands of dollars — and just as critically, they prevented safety risks and disruptions to throughput.
Mining Technology: What were some of the key challenges you faced while developing DataMind AI™, and how did you overcome them?
Tomer Srulevich: One of the biggest hurdles was integrating fragmented, siloed data from vibration sensors, SCADA, and handheld tools into a coherent, AI-readable format. We tackled this by building a Sensor Fusion architecture — combining temperature, pressure, current, vibration, oil, and visual data into a unified model. Another challenge was adapting to low-speed equipment like kilns and stackers, where traditional vibration tools struggle. Our custom envelope demodulation and edge computing made it possible to detect issues at sub-100 RPM — something the market lacked until now.
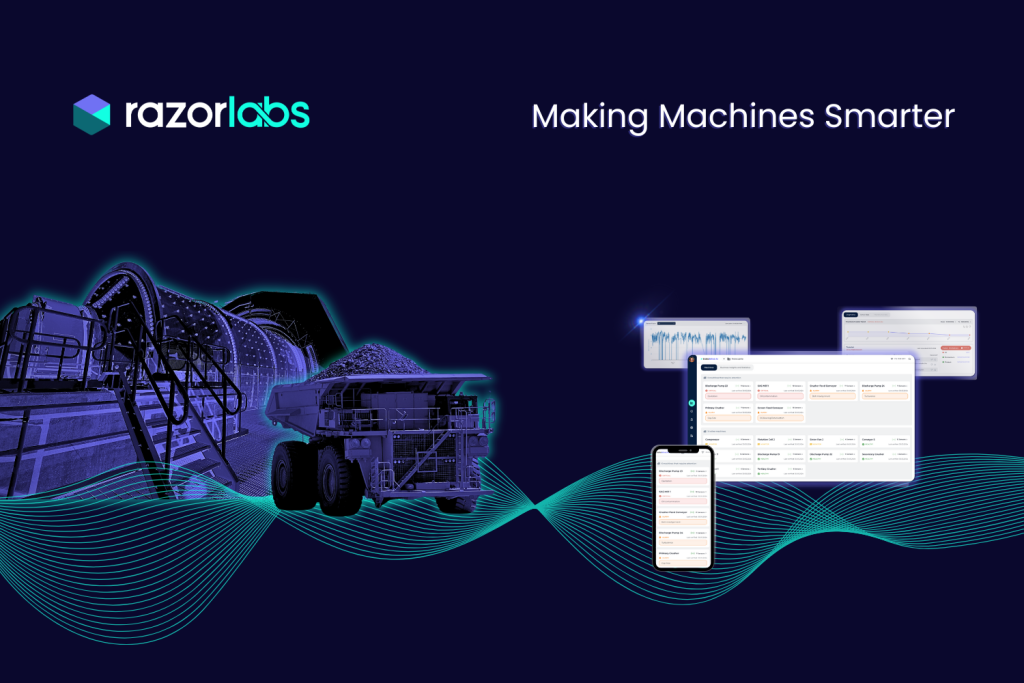
Mining Technology: How do you see real-time monitoring evolving in the mining industry, and what role will Razor Labs play in that evolution?
Tomer Srulevich: Real-time monitoring is evolving from basic alerting to automated diagnostics with prescriptive actions. It’s not enough to know something is wrong — you need to know what to do about it. DataMind AI™ is already leading that shift by identifying not only failure modes but root causes, and suggesting targeted corrective actions. We’re pushing toward an environment where maintenance is intelligent by default, and where downtime is scheduled — not imposed.
Mining Technology: Can you discuss how DataMind AI™ differentiates itself from traditional monitoring methods, particularly in terms of technology and data analysis?
Tomer Srulevich: Traditional methods rely heavily on threshold breaches or isolated sensor readings. That approach is reactive and limited. DataMind AI™ uses deep neural networks, multi-sensor fusion, and envelope demodulation to detect early, hidden signs of failure. For instance, at one site, our system detected fluting in a bearing due to stray electrical currents — a subtle issue that vibration velocity alone wouldn’t catch. Unlike legacy tools, we analyze vibration in the acceleration domain and fuse it with electrical current and pressure data for far greater accuracy.
Mining Technology: How do you ensure that your team stays updated with the latest advancements in AI and machine learning to continuously improve DataMind AI™?
Tomer Srulevich: We maintain a continuous feedback loop between our R&D team and field deployments. Every detection event, every resolved failure, and every false positive informs how we refine our models. We also collaborate with academic institutions and maintain internal research programs on semi-supervised learning, anomaly detection in rare-event environments, and edge AI deployment. And critically, we stay grounded — we spend time on-site, shoulder-to-shoulder with the teams using our product.
Mining Technology: What feedback have you received from clients regarding the implementation of DataMind AI™, and how has it influenced your product development?
Tomer Srulevich: Clients consistently appreciate our precision and clarity — not just saying “there’s an issue,” but showing what the issue is, where, and why. One client told us, “It’s like having an expert sitting in the control room 24/7.” That feedback has led us to enhance our visual diagnostics — things like showing the actual vibration signature or video frame triggering the alert. We’ve also improved integration with SAP, allowing sites to generate maintenance notifications directly from our dashboard.
Mining Technology: Looking ahead, what are some strategic goals for Razor Labs in the next 3–5 years, particularly in innovation and technology?
Tomer Srulevich: Strategically, we’re expanding DataMind AI™ across mobile assets like haul trucks and shovels, while deepening our edge analytics capabilities. We’re also advancing in process optimization — using AI not just to detect faults, but to suggest settings that improve efficiency or reduce energy use. Another goal is to make AI-driven reliability management more autonomous and intuitive — reducing dependence on site experts and enabling consistent best-in-class maintenance across all sites, regardless of their internal resources.
Mining Technology: Safety is a critical concern in mining operations. How does DataMind AI™ contribute to enhancing safety for workers on-site?
Tomer Srulevich: Safety is embedded in our mission. By catching faults early, we eliminate risky emergency interventions — like climbing on moving conveyors or opening live panels. For instance, in a centrifuge drum imbalance case, our system flagged an issue before manual testing could catch it. The site avoided both mechanical failure and the dangerous physical inspection that would’ve been required during operation. We’re turning reactive firefighting into calm, preemptive action.
Mining Technology: Can you share any upcoming projects or innovations that Razor Labs is currently working on that you believe will further impact the mining industry?
Tomer Srulevich: We’re currently developing “virtual sensors” — algorithms that estimate unmeasurable parameters like wear state or residual life based on fused input. And on the platform side, we’re enhancing self-service model tuning, allowing users to adapt diagnostics to specific local conditions without retraining the AI.
Mining Technology: What partnerships or collaborations do you see as essential for advancing the capabilities of DataMind AI™ and enhancing its impact on the mining industry?
Tomer Srulevich: Strong partnerships with OEMs and EPCMs help us integrate deeper into the equipment ecosystem. But just as important are our on-the-ground relationships with site maintenance teams — they’re the ones validating alerts and applying corrective actions. We also collaborate with software vendors like SAP and BI platforms to ensure seamless integration into our clients’ operational workflows. The future of mining reliability lies in open, interoperable ecosystems — and we’re committed to building them.
Mining Technology: Thank you, Tomer, for sharing your valuable insights into Razor Labs’ journey and the transformative impact of DataMind AI™ on the mining industry. Congratulations again on your well-deserved recognition, and thank you for your commitment to driving meaningful change in the industry.
Contact Details
E-mail: pr@razor-labs.com
Links
Website: https://www.razor-labs.com