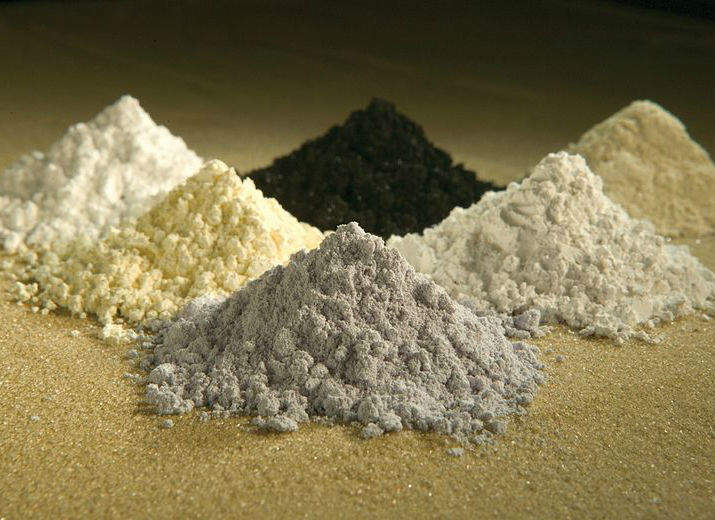
China’s rise has been a significant source of concern for politicians in the United States. Hilary Clinton, the clear frontrunner in the Democratic Party leadership race, has criticised China for ‘stealing commercial secrets, blueprints from defence contractors’ in its push for economic supremacy. Outspoken, current leader in the Republican Party race Donald Trump used China’s success to burnish his own economic credentials, saying: "When was the last time anybody saw us [the United States] beating, let’s say, China in a trade deal?" Adding: "They kill us. I beat China all the time."
One area in which China definitely has the upper hand is in the mining and production of rare earth elements, a not widely known but vitally important natural resource. Comprising a 15-element block at the foot of the periodic table along with outliers scandium and yttrium, rare earth elements have magnetic qualities making them integral to many technologies such as mobile phones, laptops, rechargeable batteries and catalytic converters.
Rare earths are not actually rare at all, but they are scattered – not many parts of the world have a high enough concentration to make mining economically viable. In addition, the extraction process is highly toxic and uses huge amounts of water. In the late 1980s, environmental and safety regulations started to put the brakes on rare earth mineral mining in the US. China, with its much more relaxed regulatory regime, stepped into the breach.
By 2010 China produced around 90% of the world’s rare earths, though for a long time this didn’t really matter to the US; China was willing to sell the country all it could want at a knockdown price. But later that year, China chose to put restrictions on some of its rare earth exports, sending prices skyrocketing in what many saw as a government attempt to exploit its monopoly advantage.
The move actually worked against China. Rather than forcing customers to buy the country’s rare earth at a higher price, it spurred other governments to initiate or ramp-up their own production, and many importers found a way around the restrictions, either by using substitute materials or those smuggled out by Chinese manufacturers. Still, the experience left a bitter taste in the mouth of the US Government and it began to look within its own borders for alternative sources to make sure it was never squeezed again.

US Tariffs are shifting - will you react or anticipate?
Don’t let policy changes catch you off guard. Stay proactive with real-time data and expert analysis.
By GlobalDataA rare stroke of fortune
At the University of Kentucky, in the Center for Applied Energy Research, Jim Hower found that his work was suddenly in fashion. As associate director of environmental and coal technologies, one of Hower’s ongoing projects is to analyse the mineral content of different collides in the US. In the early 1990s, his team was sampling a coal bed in Eastern Kentucky, known as Fireclay, which was found to have some of the highest concentrations of rare earth in the country. A decade later his team discovered that coal ash, the residue formed after coal combustion that is also known as fly ash, was another promising prospect.
"In 2001 we sampled fly ash from a power plant and the coal they were running was on a single coal seam from one line," Hower explains. "Our intention was to look at the mercury partitioning…It just so happened that it was that same coal that was high in rare earth elements so through that study we saw the high concentration of rare earths in the fly ash. In some respects we’ve been looking at this in various phases for 25 years so it has just been a very fortunate coincidence that we were doing a piece of work that turned out to get us some good information."
The US Government is starting to show real interest in such work. In June, the Department of Energy announced that it was to put $20m towards the development of bench-scale and pilot projects for recovering rare earth elements from coal and coal waste. Hower’s team has received some indirect funding from the government in the past, in collaboration with other universities, and is surely a good candidate for a slice of the $20m.
"Particularly with the fly ash, the coal has already been mined, sent to the power plant, the organics burned off, so it is in a fine state," he says. "So there are certain economic advantages that the process has over direct mining of an ore. The ores might have greater concentration [of rare earth elements] but with fly ash, even though the concentration might not be as great, we have those economic factors that help to level things out…We have to move from that level where there is just potential to at least demonstrating that it’s technologically feasible."
A potentially messy business
Although the potential and increasingly the funding is there, there are some big obstacles in the way. The price of rare earth elements is quite volatile and private companies might be less inclined to pump large amounts of cash into long-term projects if those projects become uneconomical by the time they reach completion. Many power plants don’t know the source of the coal they buy on the market – plants whose coal ash is to be used for rare earth extraction would have to ensure that their feedstock came from a seam with a high concentration of the elements, requiring some changes to the structure and transparency of the market.
The process of extracting metals from coal is also pretty dirty, involving lots of energy and toxic chemicals – the reason that mining rare earths from ore came to a halt in the US in the first place. Although the extraction process is likely to be cleaner overall than mining raw materials, is it worth producing such large amounts of waste for a very small rare earth payoff? Even if it was, the facilities to carry out the the job are, ironically, mainly based in China.
According to Lucinda Tollhurst, director of the Lucid Insight advisory group that has produced one of the most thorough explorations of the subject, one way to make this process more cost-effective is to take value from every coal byproduct. Instead of focusing on only extracting rare earths from coal, minerals such as aluminium and other bulk materials should be exploited for use in areas like construction, which would minimise waste and maximise value. Otherwise, if left as it stands, Tollhurst believes the process would be unfeasible.
"If you are just looking at rare earth in isolation, in terms of extracting value out of coal ash, I can’t see how that’s commercially viable," Tollhurst says. "There are groups in the US looking specifically for coal sources that have enriched levels of rare earth, say over 1,000 parts per million, but even at that level, and that’s very concentrated once you turn the coal into ash, the feedback I’ve had from experts is that rare earth processing downstream is quite tricky. And there are very few facilities that can actually do that – separating out the different rare earths and getting value out of it."